Piston rings are manufactured and classified on the basis of function and usability. The primary usage of the piston ring is to seal the chamber (where the piston is moving), which can be a combustion chamber of a 2 stroke or a 4 stroke engine. Marine engines have three or more types of rings fitted on the circumference of the piston.
The piston ring is an essential piston part, and its numbers and functionality differ depending on the type and capacity of the engine. In 2-stroke large engines, compression type piston rings are used to seal the combustion chamber and wiper rings are installed below them to wipe the deposits from the liner and distribute oil on the liner surface.
However, in smaller marine engines, different types of piston rings are used for dedicated purposes. E.g. oil scraper ring is used in 4 stroke engine as itβs a trunk type engine, and the crankcase oil has direct access to cylinder liner and piston. In this article, we will have a look at the different types of piston rings used in marine engines.
Types and Functions of Piston Rings
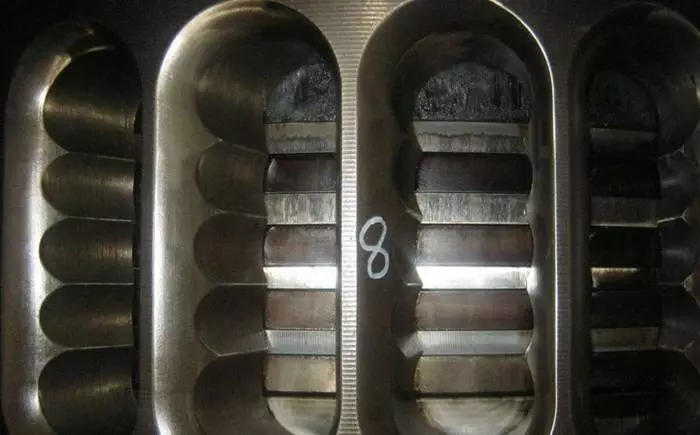
Compression Rings or Pressure Rings
The compression rings provide sealing above the piston and prevent the gas leakage from the combustion side. The compression rings are located in the first grooves of the piston. However, this may differ according to the design of the engine. The primary function of these rings is to seal the combustion gases and transfer heat from the piston to the piston walls.
The oil is controlled by shearing the layer of the oil left by oil ring, thus providing the top compression rings enough lubrication. Moreover, it also provides help to the top compression ring in sealing and heat transfer.
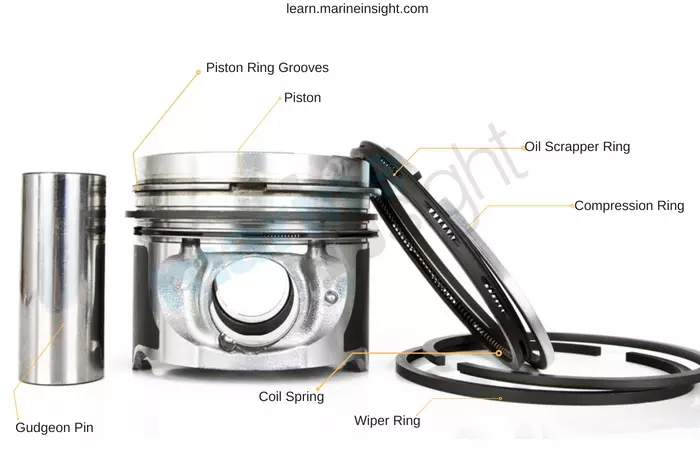
Wiper ring: The wiper ring, also called as Napier ring, or backup compression ring, are installed below the compression ring. Their main function is to clean the liner surface off the excess oil and to act as support back up ring on stopping any gas leakage further down which escaped the top compression ring. Most of the wiper rings have a taper angle face which is positioned toward the bottom to provide a wiping action as the piston moves toward the crankshaft.
If the wiper ring incorrectly installed with the tapered angle closest to the compression ring, it results in excessive oil consumption. This is caused by the wiper ring wiping excess oil toward the combustion chamber.
Oil Control / Scrapper Rings
The oil control rings control the amount of lubricating oil passing up or down the cylinder walls. These rings are also used to spread the oil evenly around the circumference of the liner. The oil is splashed onto the cylinder walls. These rings are also called scraper rings as they scrap the oil off the cylinder walls and send back to the crankcase. These rings do not allow oil to pass from the space between the face of the ring and the cylinder.
In the oil ring, holes or slots are cut into the radial center of the ring which allows the excess oil to flow back to the reservoir. Oil rings can be one piece or two pieces. To increase the contact pressure between the ring and the liner surface, the rings can have chamfered edges on either the outer sides of the lands or facing the combustion chamber to reduce the oil consumption through improved oil scraping from the bore.
Two-piece oil control rings consist of a cast iron or profiled steel ring and a coil spring which is made from heat-resistant spring steel to act around the whole ring circumference for maintaining the pressure and contact.
Piston ring material:
One of the most prominent materials used in making piston rings is cast iron. This is because it contains graphite in the lamellar form which itself acts as a lubricant assisting the sliding motion between the rings and the liner. Alloys and coatings are done on the piston rings, and it will vary as per the type of the ring as the functionality of these rings are different from each other. The most common form of alloying cast iron is chromium, molybdenum, vanadium, titanium, nickel, and copper.
The piston ring material is kept harder than the cylinder liner to provide maximum life
The Piston of Main Engine: The combustion chamber of a 2 stroke marine engine is a large space producing an enormous amount of heat and stresses. The upper rings of the piston are directly in contact with the combustion chamber, hence they need better protection and coating to tackle the thermal stress and provide proper sealing.
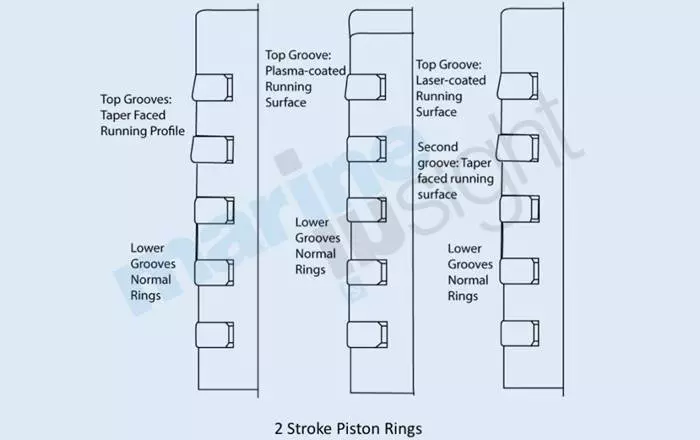
Many new designs were introduced specially for the large two-stroke marine engines. Some of the important design introduced are:
MAN engine: The uppermost piston ring is of Controlled Pressure Relief type in which several oblique shallow grooves (hard chrome plated) are provided on the face allowing some gas pressure to pass through to the 2nd ring thereby reducing the load on the top ring. It has βSβ type joint at the ring ends.
A new design was also recently introduced which is a modified version of CPR rings known as CPR Port on Plane rings (CPR POP). The modification is done on the position of the grooves which are now placed in the lower side of the ring as it was noted that the wear of CPR rings grooves in the running side was faster than usual.
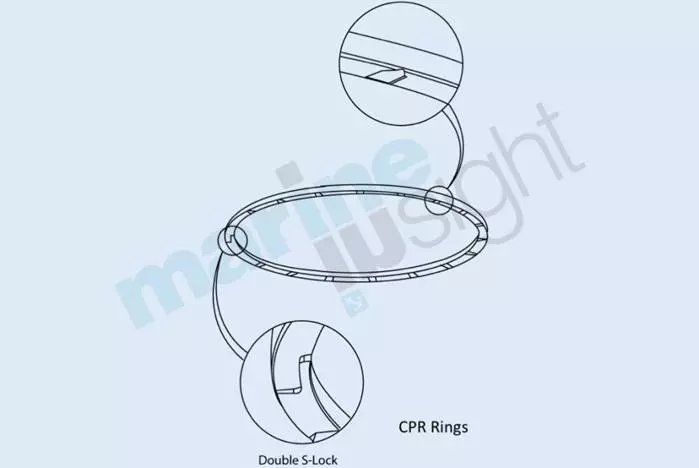
Second or Intermediate Rings: The other rings have an oblique cut at the ring ends. All the piston rings are aluminium-coated on the outer surface for helping in running-in.
Wartsila Engine: In the Wartsila 2 stroke engine, the piston ring grooves on piston surface are hardened for excellent wear resistance. The top piston ring (also known as Gas Tight (GT) ring in Wartsila) have overlapping ends to avoid gas leakage with an asymmetrical barrel shape. They are chromium- ceramic (CC) coated along with running-in coating (RC).
The number of piston ring will vary depending on the size of the engine. E.g. an RTflex 35 will have a very short skirt and is equipped with three piston rings, but an RTA engine may have 5 piston rings.3
Four stroke engine:
The piston ring requirement in a 4 stroke engine is different as the piston liner assembly is open to the sump. Hence, oil scraper rings are additionally needed in the 4 stroke piston ring-pack. It typically consisting of 2-5 rings depending upon engine type and specification. Usually, 2-4 compression rings are provided to seal the gases from the combustion chamber, and 1-3 oil-control rings are provided to excess avoid oil ingress in the combustion chamber.
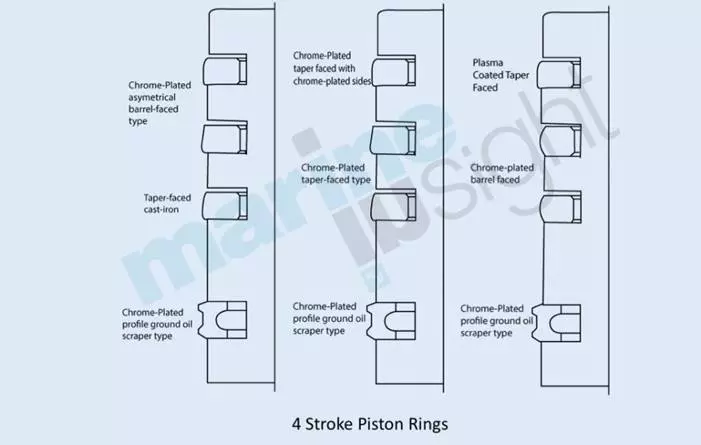
The compressor rings are usually of barrel type with taper face for efficient gas sealing. The oil-control ring profiles comprise two lands and an inserted coil spring to support the pre-tension of the ring.
Things to be Checked During Inspection of Piston Ring
Inspection of the piston rings is an important task to determine the proper working of piston rings followed by either cleaning or replacing piston rings (if broken or worn out).
In 2-stroke cycle engines, the port containing the top ring usually is at a higher position than the 4- stroke engineβs top ring groove.
During Routine Inspection
During normal scavenge space inspection, the piston rings are pressed with the help of a screwdriver. This is done to check the spring action or tension of the rings. This also tells whether the ring is broken or not. If the ring is broken there will be no spring action.
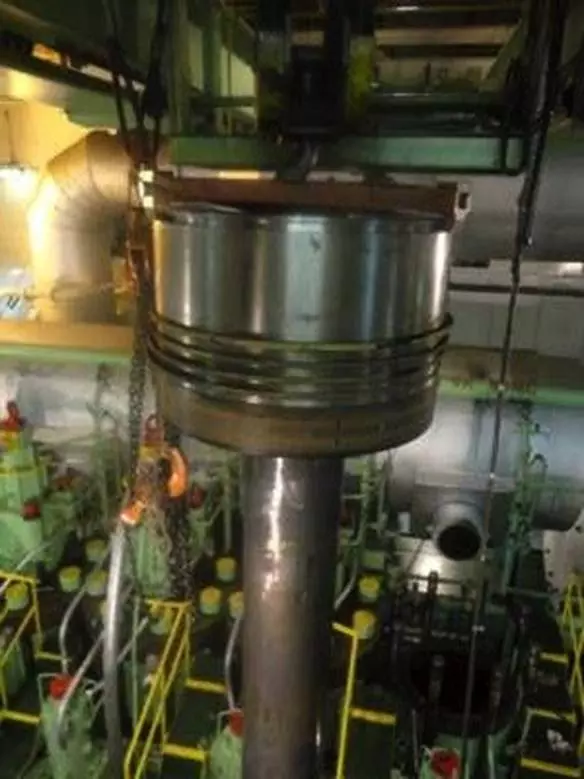
The rings are checked for their freeness in the grooves, as they might get stuck due to carbon deposits and might finally break causing a lot of damage to the liner. The clearance between the ring and the groove is also checked and the wear is calculated. The ring is checked for scuffing marks and damage, and the overall condition is also assessed.
During Major Overhaul
During major overhauls, the piston rings are changed completely with the new set. But following steps need to be considered for scrapping the rings:-
1) If the piston ring is found stuck in the groove.
2) If the axial height of the rings is reduced and the clearance in rings and groove is large.
3) If the chrome layer is peeled off or damaged.
During overhaul, the grooves have to be properly cleaned off carbon deposits and checked for damage in the ring grooves.

Before putting the piston rings, it should be first rolled rounded in the grooves. In this process, the ring is entirely moved inside the grooves. With this test, we can check that the grooves are more in-depth than the radial width of the ring. While inserting the piston with replaced rings in the liner, use the adequately lubricated piston ring compressor tool which will ensure the rings will not stick to the liner face while going inside the combustion chamber.
The piston rings are put inside the worn liner, and the butt gap is also checked. For rings of the small piston (e.g. compressor), the ends can be treated using a piston ring filer, but for marine engines, the rings have to be sent to shore workshop for reconditioning if the butt gap is unusual. While putting rings, they should be checked for markings as to which part is up or down and also check different marking for different positions.
Rings should be put with the help of proper toll, i.e. with the help of ring expander. The clearance between the ring and the groove is checked with the help of the feeler gauge.
The axial and radial clearance of old ring is checked and recorded to assess the amount of wear for a number of running hours.
Comments are closed