Corrosion is the reversion of a metal to its ore form. Iron, for example, reverts to iron oxide as the result of corrosion. The process of corrosion, however is a complex electro chemical reaction and it takes many forms. Corrosion may produce general attach over a large metal surface or it may result in pinpoint penetration of metal. Corrosion is a relevant problem caused by water in boilers. Corrosion can be of widely varying origin and nature due to the action of dissolved oxygen, to corrosion currents set up as a result of heterogeneities on metal surfaces, or to the iron being directly attacked by the water.
While basic corrosion in boilers may be primarily due to reaction of the metal with oxygen, other factors such as stresses, acid conditions, and specific chemical corrodents may have an important influence and produce different forms of attack. It is necessary to consider the quantity of the various harmful substances that can be allowed in the boiler water without risk of damage to the boiler. Corrosion may occur in the feed-water system as a result of low pH water and the presence of dissolved oxygen and carbon dioxide.
Starting form these figures, and allowing the amount that can be blown down, the permitted concentration in the make-up water is thus defined.
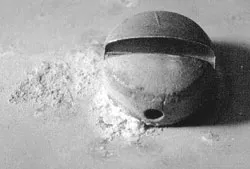
Corrosion is caused principally by complex oxide-slag with low melting points. High temperature corrosion can proceed only if the corroding deposit is in the liquid phase and the liquid is in direct contact with the metal. Deposits also promote the transport of oxygen to the metal surface.
Corrosion in the boiler proper generally occurs when the boiler water alkalinity is low or when the metal is exposed to oxygen bearing water either during operation or idle periods. High temperatures and stresses in the boiler metal tend to accelerate the corrosive mechanisms. In the steam and condensate system corrosion is generally the result of contamination with carbon dioxide and oxygen. Specific contaminants such as ammonia or sulphur bearing gases may increase attack on copper alloys in the system.
Corrosion is caused by the combination of oxide layer fluxing and continuous oxidation by transported oxygen.
Cracking in boiler metal may occur by two different mechanisms. In the first mechanism, cyclic stresses are created by rapid heating and cooling and are concentrated at points where corrosion has roughened or pitted the metal surface. This is usually associated with improper corrosion prevention. The second type of corrosion fatigue cracking occurs in boilers with properly treated water. In these cases corrosion fatigue is probably a misnomer. These cracks often originate where a dense protective oxide film covers the metal surfaces and cracking occurs from the action of applied cyclic stresses. Corrosion fatigue cracks are usually thick, blunt and cross the metal grains. They usually start at internal tube surfaces and are most often circumferential on the tube.
Corrosion control techniques vary according to the type of corrosion encountered. Major methods include maintenance of the proper pH, control of oxygen, control of deposits, and reduction of stresses trough design and operational practices.
Deaeration and recently the use of membrane contractors are the best and most diffused ways to avoid corrosion removing the dissolved gasses (mainly O2 and CO2).
Protection of steel in a boiler system depends on temperature, pH, and oxygen content. Generally, higher temperatures, high or low pH levels and higher oxygen concentrations increase steel corrosion rates. Mechanical and operation factors such as velocities, metal stresses, and severity of service can strongly influence corrosion rates. Systems vary in corrosion tendencies and should be evaluated individually.
Comments are closed