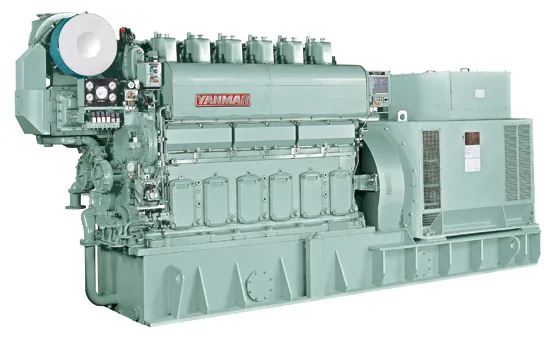
Diesel driven generators can be expensive in terms of fuel cost and maintenance requirements. Continuous operation at sea and in port exacts a high price particularly if distillate fuel is used. This has led to the use of residual fuel and the introduction of fuel blenders so that heavy residual fuel can be added to the distillate as the load increases to give cost savings. Blenders improve fuel economy but running hours still mount up and routine maintenance is likely to be increased by the use of poor quality residual fuels.
A better economy in the provision of electrical power is achieved with the use of a generator which can be operated at sea, on power derived from the main propulsion system. The ship’s electrical load can be provided by a turbo-alternator using steam from a waste heat boiler. The waste heat available from the exhaust of a very large slow-speed diesel engine is sufficient in many installations for the full electrical load at sea.
Savings in fuel costs for such a system amount to about 10% with additional savings in maintenance. However, the continuing search for improvement in diesel engine and propeller efficiency has resulted in the development of very long stroke, very slow-speed engines with constant pressure turbocharging and the waste heat available from the exhaust has gradually diminished.
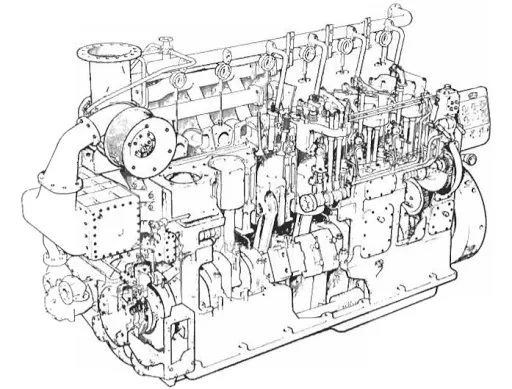
The quest for electrical power from the ever-decreasing quantity of exhaust gas energy, has fostered progress in the area of harnessing otherwise wasted heat energy. Mechanical generator drives from the main engine, gearbox or the propeller shaft temporarily lost popularity when alternating current power replaced direct current, because frequency demanded a constant speed.
Constant speed drive schemes are now available for use with variable speed engines (and a number of electrical solutions to the problem ). Power turbines, driven by the exhaust gases from the engine in the same way as the turbo-charger, are used to convert waste heat into mechanical energy which is delivered to the main propulsion system through a fluid coupling, or used to provide an integrated drive with a diesel for a generator.
Tracing faults :
The failure of an engine to start or problems while running may be traced to faults with the fuel injection system or other possible causes. Instruction manual guidance on fault finding and remedies will include some of the typical problems listed below.
Difficult starting
- Fuel system not primed through to the nozzle.
- Starting-air pressure too low.
- Water in the fuel.
- Air intake filter choked.
Poor compression due to any of the following causes:
- Exhaust valve seats in bad condition.
- Exhaust valve spindle sticking.
- Starting-air valve sticking.
- Piston rings stuck or liners worn.
- Engine uneven.
- Sticking fuel-pump control racks or linkage.
- Fuel pump delivery valves sticking.
- Overload or governor fault.
- Smoky exhaust.
- Check fuel pump timing.
- Check maximum firing pressure and exhaust temperature.
- Injectors fault.
- Overload or unsuitable fuel.