Steamships normally have two high pressure superheated steam boilers driving the turbines, either two drums one above the other or three drums with two on the bottom and one on top. The bottom are water drums and the top is a steam drum, with vertical water tubes interconnecting the drums.
Ships main engine and auxiliary power generators require a large supply of high pressure superheated steam. This steam is produced by single or multiple water tube oil fired marine boilers. The boilers are all similar in operation but vary by the number of drums they have. These drums are horizontal pressure vessels with domed ends. Depending on the manufacturer they can have two drums or three drums connected by straight vertical banks of water tubes, kinked inwards at both ends where the entered the boiler drums, which allows for thermal expansion of the tubes.
Again depending on the make of boiler, sometimes there were larger bore water tubes which were normally out-with the heat radiated from the furnace. These were known as down-comers running between the steam and water drum, and their purpose was to agitate the circulating water between the water drums and steam drum through the smaller water tubes. Also there may be water tubes along the walls of the furnace, both to keep the furnace walls refractory cool and provide extra water heating.
The following sections examine a typical two drum oil fired water tube marine boiler
Marine Two Drum Water Tube Boilers
In a two drum boiler the bottom drum is known as the water drum, and the other drum positioned above it is the steam drum. Banks of water tubes connect both drums, along with larger down-comers if used circulating the hot water.
The Superheater
Exiting the steam drum, the saturated steam is fed through a superheater, which is a nest of coils suspended from the underside of the steam drum in the path of the exhaust gases. These hot gases raise the saturated steam to a high temperature, producing dry superheated steam that is supplied to the main and auxiliary steam turbines.
Boiler Safety Valves
Both the superheater and steam drum are protected from overpressure by a set of safety valves that lift and release the steam if the operational pressure is exceeded.
Ships Boiler Standards/Regulations such as ASME specify two safety valves to be fitted on the steam drum, along with one safety valve on the superheater outlet manifold.
The superheater safety valve is set to lift before the steam drum valves to ensure a supply of steam through the superheater coils. If the drum valves lifted first this would starve the superheater coils of steam, causing them to rupture under the high temperature of the exhaust gases.
Boiler Water Level
The boiler water level is maintained by the feed-water control valve. This is situated just after the economizer and before the feed water check valve, where it enters the steam drum. The water level of water in the steam drum is indicated on the water level gauge glass that should be just over half full. There is a set of gauge glasses on the boiler with a corresponding set on the engine/boiler room bulkhead visible from the control platform.
Steam and water supplies to gauge glasses should be “blown down” through the drain valve regularly to ensure the steam and water inlets are clear of obstruction and the gauge is reading accurately
Boiler Feedwater Supply and Control of Impurities
The feed water is supplied by the boiler water feed pump via the economizer, which is a heat exchanger having a set of internal tubes. The feed water passes through the tubes, with the furnace exhaust gasses passing on the outside of the tubes and heating the feed water.
The feed water must be regularly monitored for impurities, which can corrode the inside of the tubes. When I was at sea I carried out water tests every twenty four hours on evaporators, distilled water tanks, boiler water, and the boiler water feed tank. There tests looked for alkalinity-carbonates/bicarbonates, hydroxides and phosphates, also acidity, softness, and salt ppm.
All these undesirables are treatable by chemicals injected into the system by an injection pump, and by dilution through the boiler blowdown valves whilst adding make-up feed water.
Boiler Furnace Fuel and Air Supply
The boiler is initially fired up with light gas oil and changed over to heavy fuel oil when heated through. The heavy fuel oil is dirty and very viscous, so it is passed through several sets of filters and oil heaters before being pumped under pressure to the furnace oil burners.
Forced draught fans supply the combustion air, drawing it from the top of the boiler room and discharging the pressurized air through an air heater before being swirled and spiraling with the fuel oil into the furnace. This is carried out through the air register, a device which mixes the heated air and fuel, usually allowing 25% excess air to provide complete combustion of the oil.
Boiler Tube Sootblowers
The passing of the combustion gasses over the water tubes provides the steam, however this process also causes the outside of the tubes to become encrusted with soot, dramatically reducing the transfer of heat to the water inside the tubes. To counter this, a soot blower is used to literally blow the soot off the outside of the tubes. (If I recollect right, the economizer had a soot-blower as well.)
Steam is blown through several strategically placed perforated pipes which are rotated by a motor but can also be turned by hand manually as the motors, usually air driven, are prone to seize. Many a happy hour (I donβt think!) did I spend as a Junior Engineer, stuck halfway up a stinking red hot boiler, usually in the Persian Gulf, rotating the soot blowers manually with a spanner. The Second Engineer used to watch the funnel (a black mass would be ejected out the flue as the blower rotated) to make sure you were operating them and not skiving!
Boiler Controls
The control of combustion through the oil burners and air registers, boiler steam pressure/flow and feed water supply is automatically controlled by a Bailey Boiler Control Board. This is located in the boiler room. The boiler can also be controlled manually from the main boiler room control board.
I spent my last years at sea as an engineer on steamships, but I much preferred the thump of a big two-stroke diesel to the continuous high pitched whine of the steam turbines and the whistle of superheated steam through the supply pipes.
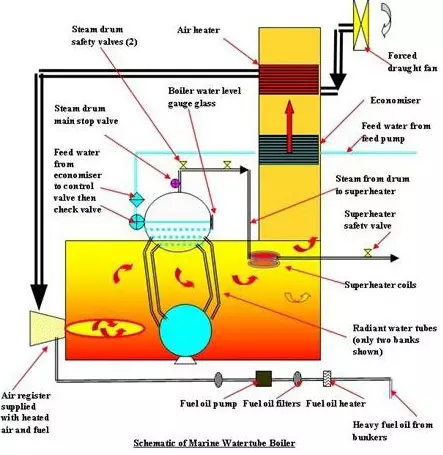
Comments are closed