Boiler tube-melt down in shore-based industry can be repaired easily. Have you ever wondered how melted boiler tubes have been repaired onboard in mid-ocean without any assistance? Read here to know about the series of events which caused failure of boiler tubes resulting in a huge financial loss.
The steam plant had two oil-fired auxiliary boilers and two exhaust gas economizers connected to each other as shown in the drawing below. During port stay, the auxiliary boiler #1 and #2 were used alternatively depending upon the steam demand. The exhaust gas economizers were out of action as the main propulsion machinery will remain stopped in port. The steam pressure on the auxiliary boiler and economizer will be almost equal as both the steam spaces are connected to each other.
The boiler is fed by the boiler water feed pumps, which take suction from the hotwell or the condensate return tank. The economizer circulating pumps take suction from the auxiliary boiler and feed the economizer when the main engine is running. In port, the economizer circulating pumps will usually be stopped after the economizer cools down sufficiently. At sea, the exhaust gas from the main propulsion machinery will heat up the water in the economizer, which ultimately becomes steam in the auxiliary boiler steam drum.
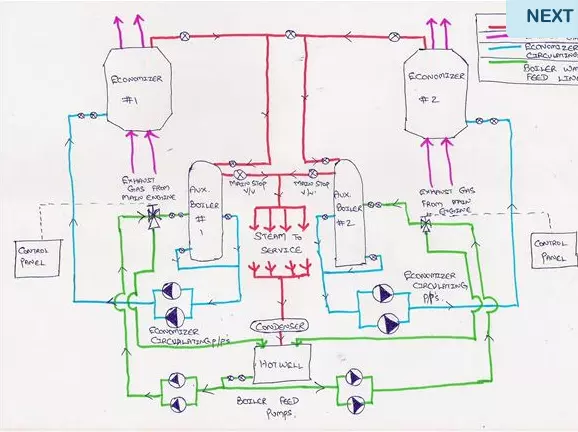
The Incident
The auxiliary oil-fired boiler burner limit switch (burner swing out limit switch), was giving trouble with its electrical contacts. Thus the 2nd Engineer and the Electrical Officer planned to change the electrical limit switch at the departure port, as the cargo operation was going. Due to tight loading schedule and hectic work pressure, the risks involved were not assessed specifically for this job. One of the previous generic risk assessments was used and discussed. The entire low voltage electrical isolation permit was filled up and the tool box talk carried out. The cargo operations completed, and the vessel sailed towards the discharge port.
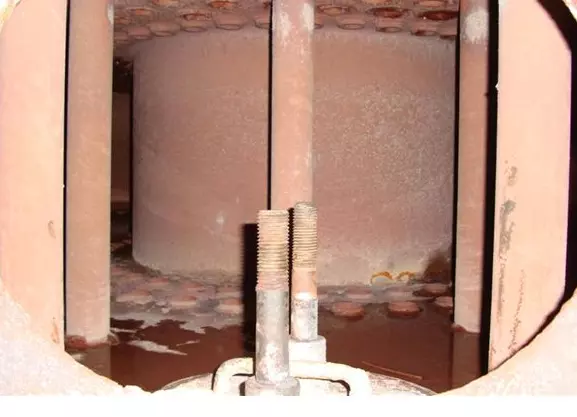
After clearing the maneuvering area, when full away was ordered, the main propulsion engines reached the maximum rpm, and the steam plant stabilized as the economizers started steaming as required. The auxiliary boilers oil firing section was stopped. Since the oil firing section was not being used (the economizers being capable of coping with the sea-going steam demand), the auxiliary boiler control voltage was switched off and โLocked out for life”.
The 2nd Engineer and the Electrical Officer started the work with the permits and proper isolation.
After ten to fifteen minutes, the duty engineer (4th Engineer) came up to 2nd Engineer and said that the steam condensate hot well tank was overflowing. Both of them started checking for the cause and could not find it. All the expansion tanksโ levels, the condenser for sea water leakage, and many other checks were done, but no clue about the overflowing hotwell was revealed. The situation was so bad that for every 30 minutes, approximately ten cubic meter of water was overflowing to the bilges and thus increasing the engine room bilge accumulation. The 2nd Engineer decided to complete the job of replacing the limit switch and instructed the 4th Engineer to look for the cause.
How this happened
When the ship was steaming full ahead, the maintenance on auxiliary boiler # 1 was started by putting off the control power switch to the burner. Because of this act, the control power to the auto-feed valve on the boiler lost power supply, which remained in shut position after that. Because of this loss of control power to the valve actuator, the valve was in closed position, causing no water to enter the boiler. But as discussed earlier, the economizer circulating pumps take suction from the boiler and circulate through the economizer. Thus this made the water level continuously drop inside the auxiliary boiler drum. The circulating water became steam and finally got condensed into the hotwell. Since the steam production and the boiler feed water quantity were not equal, the hot well started to overflow. Prolonged steam production and subsequent loss water made the auxiliary boiler completely empty, and thus the economizer circulating pumps started to lose suction. But the steam pressure was shown on the pressure gauges of the economizer circulating pump. Prolonged usage of economizer without circulating water made the tubes melt and the tube plates to leak simultaneously.
The Result
The ship was stopped for approximately 78 hours to rectify and plug the damaged tubes. A temporary repair was carried out over the tube plates to make the ship safe enough to reach the next port. The delay, with cargo loaded on board, amounted to a loss of a few million dollars, which no manager will be ready to accept due to a simple reason and cheap mistakes.
Comments are closed