The machinery systems fitted on board ships are designed to work with maximum efficiency and run for long hours. The most common and maximum energy loss from machinery is in the form of heat energy. This loss of heat energy has to be reduced or carried away by a cooling media, such as central cooling water system, to avoid malfunctioning or breakdown of the machinery.
There are two cooling systems used on board for the cooling purpose:
1. Sea Water cooling system: Sea water is directly used in the machinery systems as a cooling media for heat exchangers.
- Freshwater or central cooling system: Fresh water is used in a closed circuit to cool down the engine room machinery. The fresh water returning from the heat exchanger after cooling the machinery is further cooled by sea water in a sea-water cooler.
Understanding Central Cooling System
As discussed above, in the central cooling system, all the working machinery on ships are cooled down using circulating fresh water. This system comprises of three different circuits:
Sea water circuit
The sea water is used as a cooling media in large seawater cooled heat exchangers to cool the fresh water of the closed circuit. They are the central coolers of the system and are normally installed in a duplex.
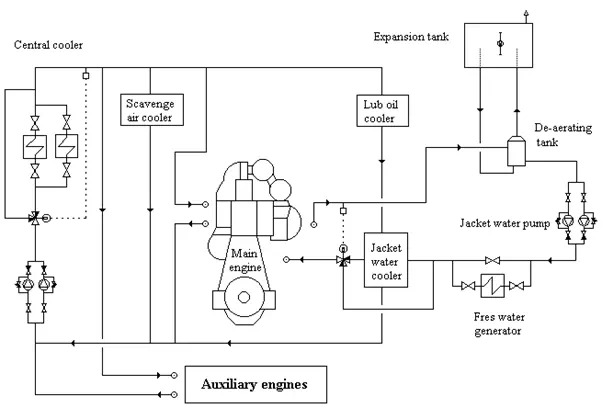
Low-temperature circuit
The low-temperature circuit is used for low-temperature zone machinery and this circuit is directly connected to the main sea water central cooler; hence its temperature is lower than that of high temperature (H.T circuit). The L.T circuit comprises of all auxiliary systems.
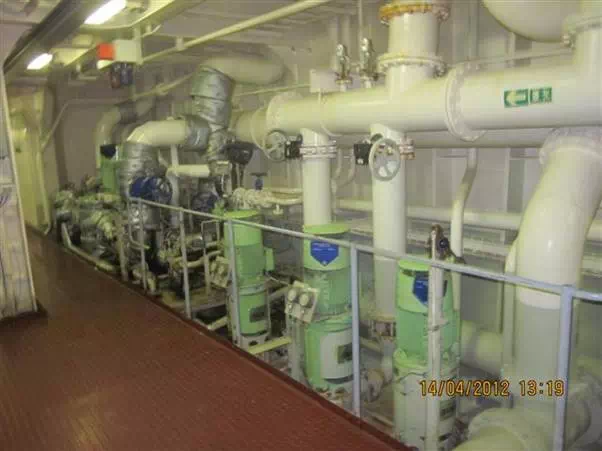
The total quantity of low-temperature or L.T fresh water in the system is maintained in balance with the H.T. fresh water cooling system by an expansion tank which is common to both systems.
The expansion tank used for these circuits is filled and makeup from the hydrophore system or from the distilled water tank using the F.W. refilling pump.
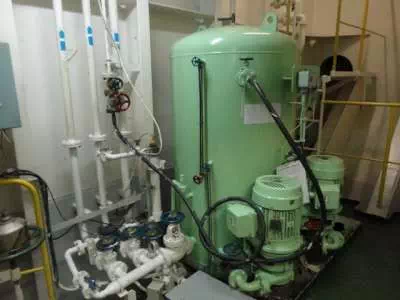
High-temperature circuit (H.T)
The H.T circuit in the central cooling system mainly comprises of jacket water system of the main engine where the temperature is quite high. The H.T water temperature is maintained by low-temperature fresh water and the system normally comprises of jacket water system of the main engine, FW generator, DG during standby condition, Lube oil filter for stuffing box drain tank.
The HT cooling water system is circulated by electrical cooling water pumps, one in service and one standby.
During standby, the DG is kept warm by the circulating system from the DG in service.
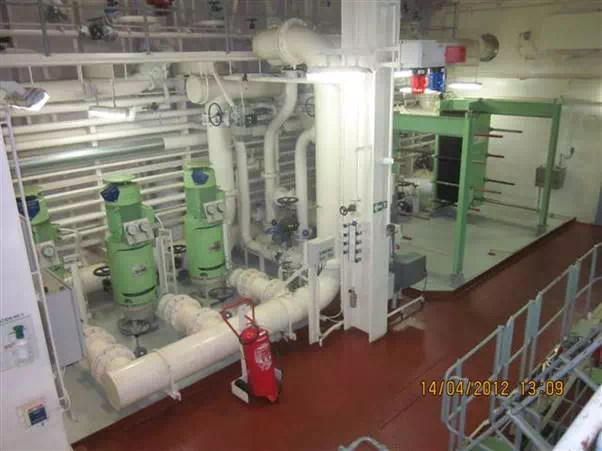
When ME is stopped, it is kept warm by HT cooling water from DG. If this is insufficient, the water may be heated by steam heated FW heater.
Expansion tank
The loss in the closed circuit of the central cooling fresh water system is continuously compensated by the expansion tank which also absorbs the increase in pressure due to thermal expansion.
Temperature Control Valves
The heat absorbed by the H.T circuit is transferred to L.T circuit at temperature control valve junction.
The outlet temperature of the main engine cooling water is kept constant at 85-95 by means of temperature control valves by mixing water from the two central cooling system i.e. LT system into the HT system.
Things to remember
· The cooling water in the system to be treated with chemicals
· The makeup of central cooling system normally takes place from FW expansion tank, which is filled with drinking and wash water system, or, from the distilled water tank using the FW refilling pump
· If it is necessary to refill the system with a larger amount of water, this shall be supplied from the distilled water tank by the FW refilling pump via the LT system connection
· During overhaul/repair of the main engine, which requires FW cooling water inlet and outlet valves to be closed, the FW cooling pump and high-temperature circulation must be stopped and air to control valve must be closed
· In standby condition, the transfer of surplus heat from diesel generators can be used for FW generator service. In the feed water inlet to the FW generator evaporating section the high load orifice is to be replaced with the low load orifice, see maker’s instruction.
· The circulating rate will depend on sea water temperature, engine load, the pressure drop across pumps and required heat removal from the system. The circulating rate can be adjusted by operating one or more pumps
· Generally, two fresh water pumps are installed and one complete spare pump is stored close to the working pumps area for quick installation in case one of the working pumps should fail
· The central coolers in the fresh water system are generally of plate type with plates of titanium material
· In the case of manual cleaning, the F.W. inlet and outlet valves shall be closed. In the case of chemical cleaning of S.W. side the F.W. side may be kept open.
Advantages of central cooling System
· Low maintenance cost: As the system runs with fresh water, the cleaning, maintenance and component replacement reduces.
· Less corrosion: Since the sea water system is only in the central part, the corrosion of pipes and valves decreases.
· The Higher speed of fluid hence better heat exchange: Higher speed is possible in the fresh water system which results in reduced piping and low installation cost.
· Use of cheaper materials: Since the corrosion factor decreases, expensive materials are not required for valves and pipelines.
· Constant temperature level maintained: Since the temperature controlled is irrespective of sea water temperature, stable temperature is maintained which helps in reducing machinery wear down.
· Less wear of engine parts: Less wear of cylinder liner as the jacket is maintained warm avoiding cold corrosion.
· Ideal for unmanned engine room: The greater reliability and temperature controlling of the system offered by the central cooling system makes it an ideal choice for unmanned engine room
Disadvantages of the central cooling system
· High installation cost
· Limitation of low temperature
Comments are closed