Corrosion has been a menace, for decades, to global development, especially in oil and gas assets, mostly in coastal and marine environments. Maintenance is a better option than replacement as this prevents loss of time and cuts cost. In order to improve the quality and minimize the time taken for the process of maintenance with the consideration of the fleeting environmental regulations, new anticorrosion coatings are being developed, giving cognizance to improved service life, better protective performance, and improved mechanical properties in aggressive marine conditions. These coatings have a minimum thickness that gives tolerance for turbulence effect of seawater in order to withstand degradation. As a result of fluid turbulence on asset regions close to sea level, there is excessive deposition of salt content on the coating surface due to saltwater splashes; corrosion is of high level of proneness if pores are present in the coatings. Localized chemical attacks take place, resulting in catastrophic failure of oil transport vessels during service.Porosity is an important issue to consider in examining the life expectancy and performance of coated structures as it may exist due to dissolution of prime elements from the coating into the environment. For instance, the effect of the dissolution may be the formation of galvanic cell between substrate and electroless nickel coating on steel immersed in an acidic environment; hydrogen evolution takes place, increasing the pore dimension and speeding up localized corrosion of the substrate. Porosity is a critical factor to be considered in the design of coatings as many researchers have implemented and provided various methods to curb its existence.
Firstly, electrodeposition offers a variety of appropriate techniques for the fabrication of tailored metallic and composite coatings, which include powder metallurgy, nitriding, metal spraying, and vacuum deposition. It is, simply, the use of current flow to mitigate the desired cation of a material in a solution for coating of the material to be attained as a uniform, thin film on a conductive metal substrate. It is a successful way of dealing with the issue of porosity in coatings because this technique is compatible with the deposition of a wide scope of materials, such as nickel, zinc, cadmium, aluminum, and their respective composites in severe marine environments. Secondly, electrodeposition offers the flexibility of controlled processing of these corrosion-resistant coatings. However, expertise is highly appreciated in the full knowledge of the manipulation of the system and design parameters employed for optimum deposition characteristics. Computational analysis of the effect of these parameters and their interactions on the deposition quality can be achieved based on various designs of experiments (DoE). These DoE offer the possibility of understanding the cause-and-effect of the parameters on the final product and finding the interactions between variables and running effective experiments in a cost-effective manner. They also provide the opportunity of building mathematical models to support the correlation between product properties and significant processing parameters, establishing a platform for future consideration.
Marine corrosion
Corrosion occurs fastest in the marine environment as a result of the high concentration of salt content in the atmosphere. The contained salt increases the susceptibility of marine assets to degradation.
SALINITY
In relation to chemical perspective, seawater is a solution of salts dissolved in water. Typically, the salinity of an ocean can be measured at a value between 3% and 4% [1]. The concentration of [Cl−] ions in water determines the degree of salinity [2]. Evaporation of water can probably pose as a determinant of the occurring differences in local salinity, which, in turn, increases the degree of salinity of seawater [3]. When water exchange is restricted in a certain region of the sea, a free water inflow into the sea will lead to a drop in the salinity of seawater [4, 5].
TEMPERATURE
Another factor that affects the salinity of seawater is temperature; as the temperature decreases, concentration of dissolved salt decreases, that is, there is a drop in solubility [6, 7]. This drop in solubility reduces the conductivity of the seawater, increases its electrolyte resistivity [8], and encourages the dissolution of oxygen. With an increase in the oxygen dissolution, corrosion rate becomes greater [2].
GEOGRAPHICAL OCEANS
Influence of corrosion rates on marine equipment, assets, ships, and oil platforms can be influenced by geographical factors. The combined effect of salinity and temperature can be seen in various oceans, which eventually lead to variation in corrosion rates. Oceans situated at regions close to the North and the South poles are prone to ice formation due to low temperature. Brine is trapped within crystals, thereby depleting the level of salinity. Oceans close to the equator possess higher degree of salinity as this can have a higher influence on the corrosion rate of machinery.
Corrosion
Corrosion is referred to as the degradation of a material’s properties and performance as a result of the material’s reactivity with its environment. Most of the time, the reaction turns out to be inexorable. This enables the rapid consideration of research and development, seeking for better paths of eradicating its effect. Polymers and ceramics undergo degradation in the form of aging and selective dissolution, respectively. Corrosion is majorly associated with metallic structures, especially structures that are in the vicinity of marine regions. Ships, oil platforms, and vessel assets are the major victims of corrosion based on the highly induced attack by seawater. With increasing industrialization, the cost of battling corrosion has consistently been rising as the years go by. Based on the thermodynamic phase for corrosion, it is of little wonder that the attributed cost with corrosion has skyrocketed. Many studies conducted for more than three decades have revealed that the yearly expenditure on corrosion control is close to 3.1% of the Gross National Product (GNP) of the country. This works out to a value above $275 billion annually [9]. In 2001, the United States experienced an uprising in its cost of corrosion control to a shocker of over $600 billion, representing about 5% of the GNP of the country. This could be interpreted in such a way that for every family of four, the net annual expenditure on fighting corrosion is $8,000. In addition, corrosion seems to be the nation’s most significant cause of financial calamity; it costs more than natural disasters and automobile accidents [10]. Figure 1 shows the result of the study on corrosion cost distribution of the United States carried out by the United States Federal Highway Authority in collaboration with the National Association of Corrosion Engineers (NACE) in 2001.
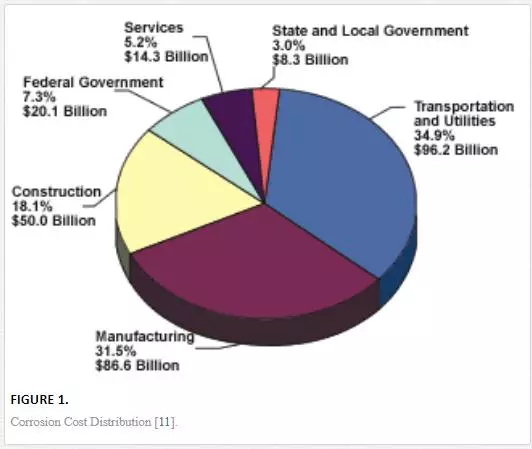
Chemistry of corrosion
Corrosion is defined as the deterioration of a component that occurs due to its interactive reactivity with the environment. When a metal comes in contact with a liquid, an electrochemical reaction is set up involving a transfer of electrons across the metal/liquid boundary. Conservation of energy is observed as metals return to their original state; the energy required for corrosion to occur is the energy responsible for converting the ores to metals. This energy responsible for the conversion is a free energy known as Gibb’s free energy. When an atom leaves the crystal structure of a metal, it exceeds the interatomic forces binding the atoms together in the crystal matrix. The surface atom experiences lower attractive forces compared with the internal atoms, a significant increase in temperature can enable the outer atom to leave the structure, leaving its electrons behind [12]. This is why corrosion is rapid with increased temperature in a corrosive medium. The equation below illustrates the electron transfer of a metallic atom leaving the surface of the metal, an oxidation reaction:

where ‘M’ symbolizes the metal and ‘n’ is the number of electrons left by the metal atom on the bulk metal.
As the atom leaves the surface, it immediately appears as an ion in the liquid. With subsequent dissolution of the metal atoms to form ions, the weight of the bulk material reduces, creating a rough metal surface. The metal ion reacts with dissolved oxygen present in the liquid to form the metal oxide. Most times, the corrosive medium appears stagnant, thereby leaving the oxide product on the corroded surface; in the case of iron, the oxide formed is known as ‘rust’. The oxidation and reduction mechanism is shown in Figure 2. Even though it appears that corrosion takes a generic routine, there are different forms of corrosion as a result of the localization, nature of corrosive medium, and chemistry of the metal itself. Corrosion is independent of distinct electrodes, as it may occur at micro scale. Numerous anodic and cathodic sites may appear on a single surface where oxidation and reduction reactions take place [13].
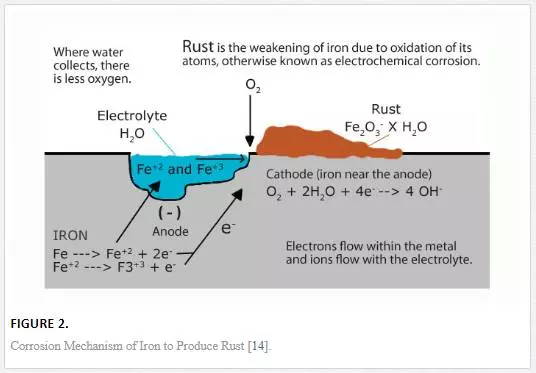
Forms of corrosion
Useful information of the history of corrosion of a failed material can be carefully acquired if adequate observation is made. Based on the appearance of the corroded component, there are eight different forms of corrosion.
UNIFORM OR GENERAL CORROSION
Uniform or general corrosion is the most common form of corrosion. It is frequently attributed with electrochemical reactions, which prevails in a homogeneous manner across the surface of the component that is exposed to the atmosphere. As corrosion proceeds, the component reduces in dimension as failure becomes imminent. This form of corrosion is known to be the most disastrous form of corrosion, which may lead to a massive deterioration of metal. As its name appears, it affects a wide span region unlike the other forms of corrosion that are localized in nature. Therefore, its effect may be predicted experimentally [15]. It can be controlled by cathodic protection or by applying coatings and paints and also by introducing dimensional allowance (Figure 3).
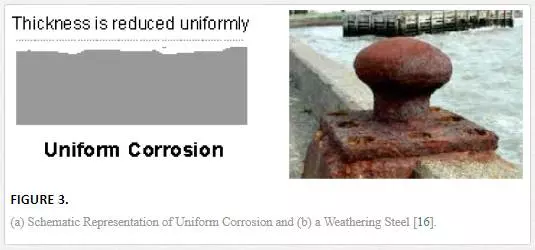
The degradation of coating structures for surface protection usually results in uniform corrosion. Characteristics observed on such surfaces are muting of shiny metallic surfaces, discoloration of iron-based materials, and rough impressions by corrosive media. Surface degradation is the result of a negatively altered coating system and consideration should be given to repair; otherwise, it may lead to worse situations of corrosion attacks [16].
CREVICE CORROSION
Crevice corrosion is a localized form of corrosion attack. It exists with metals and alloys, which have unstable passive films in the presence of chloride and hydrogen ions. It is common with nonferrous metals, such as aluminum, zinc, titanium, and copper, but not with stainless steels. This form of corrosion attack occurs at crevices, joints, riveted regions, flanges, or isolated regions beneath where debris deposits can be found. Sand and dust deposits with scales and products from degradation can act as preferred sites where corrosive electrolyte can be reintroduced with high level of challenge [17]. For crevice corrosion to take place, the opening must be spacious for accommodating and retaining the electrolyte. Though there are no specific dimensions for crevices, this form of corrosion can be present where there are gaps of few micrometers. The presence of high level of chromium can reduce the possibility of crevice corrosion [18]. Also, considering flanges and joints, compromise must be made in terms of the opening because extremely narrow openings may lead to galvanic or cell corrosion, whereas a larger opening will allow accumulation of electrolyte that initiate crevice corrosion (Figure 4).
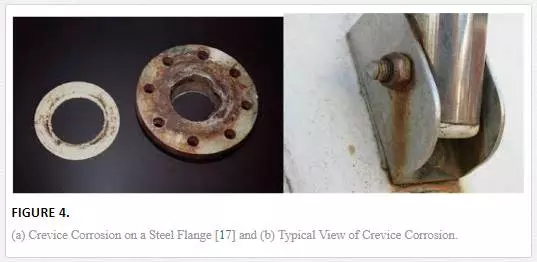
INTERGRANULAR CORROSION
This form of corrosion is observed at the microlevel of metals situated at grain boundaries. Rapid attack of neighboring grain boundaries will eventually lead to cracking of the grain structures. Sometimes, elements and phases may be precipitated out of the grains and migrate to the grain boundaries as a result of processes, such as aging; these migrated precipitates can be a mismatch with the grain boundary composition, in this manner, causing a depletion of intergranular bonds. Also, adjacent grains may lose significant elements such as chromium to chromium-rich grain boundary precipitates, leaving those regions deficient of chromium and susceptible to corrosion in a corrosive medium (Figure 5).
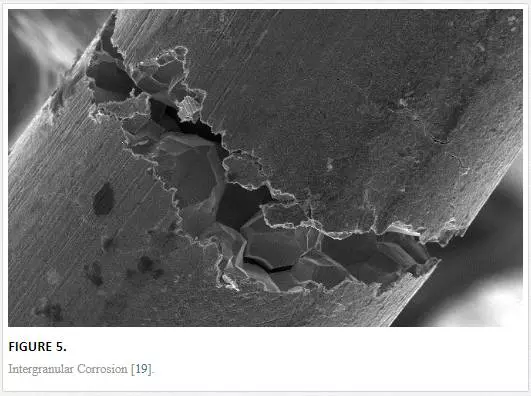
PITTING CORROSION
Pitting corrosion has been one of the most expensive forms of corrosion because of its unpredicted manner of attack. It is a form of confined degradation which yields effects in the form of pits and holes. This form of corrosion may exist in stainless steels whether in acidic or neutral chlorides. An example of such media is the seawater. Pitting corrosion concentrates on the weakest link, which is a region where passive layer might not be tough enough. The mechanism is very rapid as a damaged surface experiences successive deterioration within a short period of time (Figure 6).
Pitting is dependent on temperature, the chloride concentration, and pH value. A low-corrosive environment will aid a natural repair of a steel grade pit in the presence of oxygen. Natural seawater causes more harm in terms of pitting than any other chloride-contained corrosive media as a result of its biological interaction. This requires the prevention of microorganism growth by applying biocides in seawater piping systems [20].
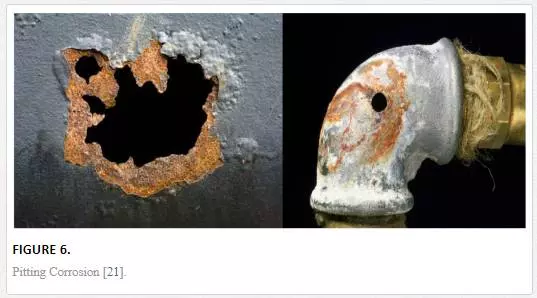
EROSION CORROSION
Erosion corrosion is a rapid rate of corrosion action on metals and alloys as a result of relative movement of corrosive fluid to the metal of alloy surface. With rattling flow of the fluid, the inner surface of a pipe or a tube can be washed resulting in erosion and then a leakage. This form of corrosion attack can occur due to bad internal design of component, for instance, a protruding inclusion which was meant to be trimmed can perturb a laminar flow of the fluid. Subsequent washing of a localized region on the inner surface by high-velocity fluid flow can initiate erosion corrosion. Pitting may result from a collaboration of erosion and corrosion. For erosion corrosion to be mitigated, pipe diameters should be increased while turbulent flow will be eliminated. Also, highly affected regions, such as elbows and bends, should be designed with thicker materials [16] (Figure 7).

The other three forms of corrosion are hydrogen embrittlement, stress corrosion cracking, and galvanic corrosion. Hydrogen embrittlement can be experienced in acidic media where the hydrogen ions act on the surface of the metal in contact; stress corrosion cracking occurs with materials having a combination of stress-induced conditions under corrosive environment; and galvanic corrosion takes place between two dissimilar metals in contact.It can be seen that necessary ways of protecting metals from the actions of corrosive media, mostly in the marine environment, should be looked into. This will drastically reduce the massive amount of expenditure on corrosion control, especially in industries such as marine, defense, and oil and gas sectors.There are two major forms of corrosion that dominate the morphology of degradation: galvanic corrosion and electrolytic corrosion.
Surface engineering
Surface improvement of engineering components is expedient in order to protect these components from premature failure and effect of corrosion during service [23]. Surface engineering can be described as a broad set of technologies that focuses on the design and modification of surface characteristics of a component. Surface engineering can be seen in two major ways for improved surface characteristics and bulk material, that is, surface coating and surface modification, whereas surface shape design is a secondary type of surface engineering. Surface coating processes entail deposition of layers in the form of molten or semi molten material on the surface of a metal (substrate). Part of the prime reasons for surface coatings is to enhance the surface behavior rather than altering the bulk composition of the material. There are various techniques of applying surface coatings, which include chemical and physical vapor deposition (C & PVD), thermal and plasma spraying, cladding, and electrodeposition [24]. With surface modification, processes like surface hardening and alloying performed either by flame, laser, electron beam, induction, or elevated energy treatments (ion implementation, carburizing, and nitriding) are considered. Surface modification processes are employed to regulate surface tribological properties. Sometimes, there can be a combination of surface coating and surface modification, as in the case of laser cladding [25]. The major challenge of these techniques is the presence of porosity as this coating defect lays a strong platform for localized forms of corrosion, even a general form of corrosion.
Electrodeposition
Electrodeposition can also be referred to as electroplating since electroplating occurs during the process of electrodeposition. This is a process that makes use of electric current to mitigate cations from a preferred solution and migrate them as a thin-film coat on a conductive plate immersed in an electrolyte. Deposition of coatings can be achieved to obtain an improved surface with an excellent protective coating via electroplating technique [23]. The deposition of the material (the cations receive electrons at the cathode and are reduced to their metal atoms) as coatings on the conductive plate can be influenced by various factors, that is, the nature of cathode, electrolyte (salt bath), electric current, and so on (Figure 8).
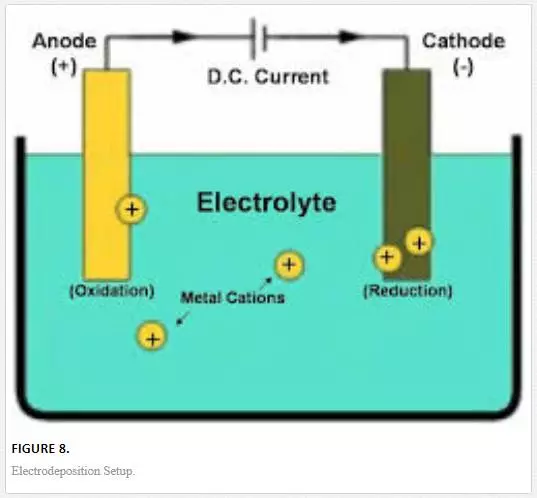
Porosity is among the major causes of discontinuities in electrodeposited coatings. The other causes are elevated internal stresses, corrosion, and wear of the plated surface. Porosity may be deleterious as its presence can expose coated surfaces to corrosive media, deplete mechanical properties, and affect density and diffusion properties in a negative manner. Pores that are created based on increase in temperature during service can lower the adhesion ability of a deposited layer. The presence of pores in metal coatings that readily produce thin passive film may be given less consideration compared with noble metals. For instance, if zinc is coated on a steel substrate, the zinc will be sacrificial by cathodically protecting the steel substrate. Furthermore, the presence of pores can allow the degraded products to accumulate on the substrate surface, leading to a localized form of corrosion, such as pitting. A material that contains pores or voids formed during electrodeposition is prone to deterioration of properties. The mechanical feature of a pore-contained coating is identified by a massive reduction in toughness and strength with increasing pore volume as ductility is also decreased.
ELECTROLESS PLATING
Electroless plating can be defined as a method of application of protective coatings: a chemical reduction–oxidation reaction that takes place as metallic ions are automatically aided in reduction. This can be achieved in an aqueous solution, which includes a reducing agent while deposition is made without flow of electrons [26]. Deposition of coating and its quality in electroless plating can be influenced by various variables that include the bath concentration, bath volume, acidity or basicity of the bath, bath history, temperature, and bath additives [27]. Electroless plating has better yield and quality with better surface profile compared with conventional electrolytic deposition; this is due to the flexibility of manipulating process parameters to obtain tailored coating dimensions. Figure 9 illustrates this benefit.
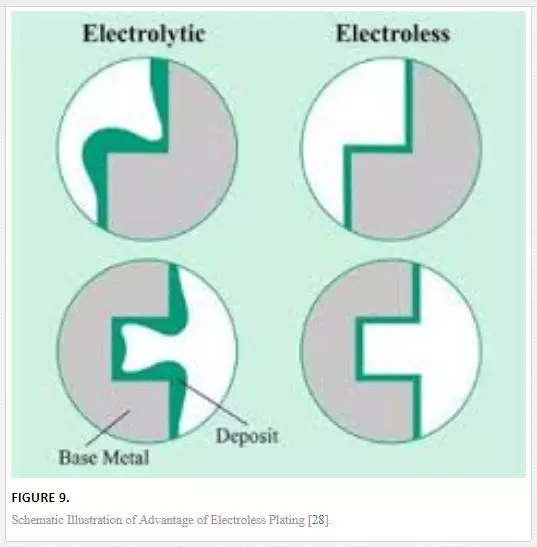
Process parameters
For optimized system of uniform deposition and elimination of porosity in deposited coatings, the knowledge of the influence of deposition parameters is essential. Current density, time, nature of electrolyte, voltage, salt bath composition, temperature, stirring rate, pH value, and substrate type are the prime parameters that influence the deposition rate. Adequate control of the relationship between these parameters will yield an optimized deposition. Current density is inversely proportional to time while, theoretically, conductivity of the substrate varies inversely as the time [29]. This shows that a mathematical relationship can be achieved for various electrodeposition setup depending on the aforementioned parameters.
CURRENT DENSITY
The current density is the rate of movement of a certain quantity of electricity per unit volume within the electrolyte. It is observed that the larger the current density, the more nucleation sites are widely distributed across the cathode [30]. Also, the current density favors the formation of larger grain sizes, with a lower strength compared with smaller grain sizes. Therefore, large current density produces more nuclei sites, whereas small current density will support small grain growth; adjusting the current density will tailor the quality and the properties of the coating to a better performance [31].
DEPOSITION TIME
The time taken for deposition of uniform coating can be affected by other variables, for instance, a larger current density will reduce the time of deposition or an electrolyte with higher molecular mass will slow down the deposition process and increase the deposition time. The stability of an electroless bath strongly influences the time of coating deposition. Higher stability of bath may lead to increase in time of deposition, and thus a steady renewal and replacement will be achieved with respect to unit area [32].
SUBSTRATE TYPE
Properties of the substrate, such as the conductivity, surface profile, and chemical composition, can determine the substrate’s affinity for rapid coating deposition [33]. High electrical conductivity will ensure faster movement of electrons to the cathode (substrate) surface where reduction will occur. The more the supply of electrons, the faster the rate of metal deposition.
BATH COMPOSITION (ELECTROLYTE)
The bath composition is dependent on the molecular mass of the additives and also their viscosities. Bath age, bath formulation, bath temperature, and stability are integrated in the net influence on coating deposition rate. Usually, a rise in the bath temperature has a way of inducing an increase in metal solubility and stability in the electrolyte, resulting to a surge in transport number and conductivity of the specie, though the viscosity of the electrolyte is reduced [34]. Another bath parameter that influences deposition rate is the stirring rate; a higher stirring rate will lead to increase in bath agitation and decreased time to attain adsorption on the cathode surface, hence deposition rate is increased.
Computational analysis of process parameters
Predictive models, simulations, and theories have been developed over the years to subdue the hardship of material development. Response surface model, artificial neural networks, and Taguchi models are forms of predictive models which have been used to achieve optimal deposition. These models have also eliminated the use of trial and error methods in experiments. The high cost of resources, time, and labor has been taken care of by the advent of DoE. DoEs make experiments easier by linking data compilation with experimental procedures to analysis of results and prediction of optimized output and performance.
Generally, several experiments are often needed to be carried out considering different plating parameters and plating functionality in order to achieve a model. An artificial neural network model was developed for the deposition of copper and then compared with regression model. Validation was performed by conducting another set of experiment with the same conditions and then comparison was made. The validation showed a percentage error, which was less than 1.0 [34].
The future
Studies are ever increasing on the development of new and effective techniques on electrodeposition. Oil platform assets, ship vessels, and marine components will be able to function at optimized performance for longer duration without the cost and labor of repair and maintenance. Coatings that will be able to be highly unresponsive to severe marine environments and adhere strongly to underlying substrate are becoming more achievable irrespective of harsh cascading of saltwater splashes on ship hulls, propeller panels, and rig supports. Consequently, the global cost on corrosion control will diminish to an appreciable extent, though it will still be a serious discussion ever-present in the world of engineering and technology.
Comments are closed