Just installing a boiler on a ship doesnβt guarantee efficient working of a boiler. There are several mountings and attachments required to be fitted on the boiler to ensure its safety and quality performance. The article describes a comprehensive list of boiler mountings without which a boiler cannot operate on a ship.
Boiler operation can be carried out safely and efficiently by only using the mountings described below:
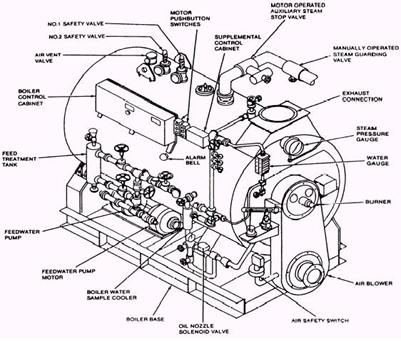
1) Main steam Stop Valve: The steam generated in the boiler is supplied to the main system through this v/v. It is normally non-return type of valve.
2) Auxiliary steam Stop Valve: If there is separate steam line provided for small auxiliary system, it is supplied through this valve. The valve is smaller in size and usually of a non-return type.
3) Safety valve: In the event of unsafe excessive pressure inside the boiler, the safety valve comes in action to release the overpressure. The lifting pressure of the valve is set prior to its installation and locked in the presence of a surveyor so that it not changed later on. Safety valves are generally installed in pairs.
4) Water level gauge glass: Gauge glasses are also fitted in pairs for manually checking the water level inside the boiler drum. It is on the basis of the boiler pressure that the construction of the gauge glass is decided.
5) Air release valve or boiler vent: This valve is fitted in the headers, boiler drum etc, to avoid imploding of boiler when it is depressurized or when initially raising the steam pressure.
6)Feed check and control v/v: This valve controls the supply of steam supply as per the demand and is fitted in both main and aux steam line after the stop valve. They are non-return valves with a visible indication of open and close position.
7) Pressure gauge connection: This pressure gauge can be fitted in super heater, boiler drum and wherever it is necessary to read the pressure reading.
8) Blowdown valve: It is used to empty the boiler completely for maintenance purpose or for water treatment of boiler when the chloride level becomes very high.
9) Scum blow down valve: Itβs a shallow dish type arrangement fitted at the normal water level which allows the blow down of floating impurities, oil foaming etc from the water surface.
10) Sampling connection: Generally, a sampling water cock arrangement is also fitted with cooler in series so that water sample can be collected at any time for feed water analysis.
11) Whistle valve: If there is a provision for steam whistle in the ship, then steam is supplied directly from the boiler through a small bore type non-return valve known as whistle valve.
12) Low Level alarm: A device used to initiate audible warning at low water level condition.
13) Soot blowers: Required to blow the soot and the combustion products from the tube surfaces. It is operated by steam or compressed air.
14) Automatic feed water regulator: Device which is essential to ensure appropriate water level in all load conditions and is fitted in the feed line. Multiple element feed water control system is used in boilers with high evaporation rate.