he analysis, design and construction of offshore structures is undeniably a very demanding set of procedures that an engineer has to face. Apart from the usual difficulties met by land-based structures, offshore structures are placed in a hostile environment where high wave and wind loads become major considerations in their design (Haritos, 2007).
The loads that an offshore structure is subjected to are divided in two categories: those due to the function on the structure (Functional loads) and those due to the environment (Environmental loads). The first category includes static or dynamic loads from the operation of the structure, the weight of the structure, the buoyancy etc. The second category includes loads that come from the direct or indirect interaction of the environment with the structure, such as wind load, wave load, earthquake load, current load etc. (Mavrakos, 1999).
The two main loads that are being calculated in this project are wind load on the tower and on the rotor of the turbine and wave load on the jacket legs.
Wind Loads on pile
In order to calculate the wind load on the turbine tower we make the approximation that it is a cylindrical body, although the diameter of the tower decreases as we get closer to the rotor.
In accordance with DNV, the force due to wind that an element is subjected to is calculated from the equation:
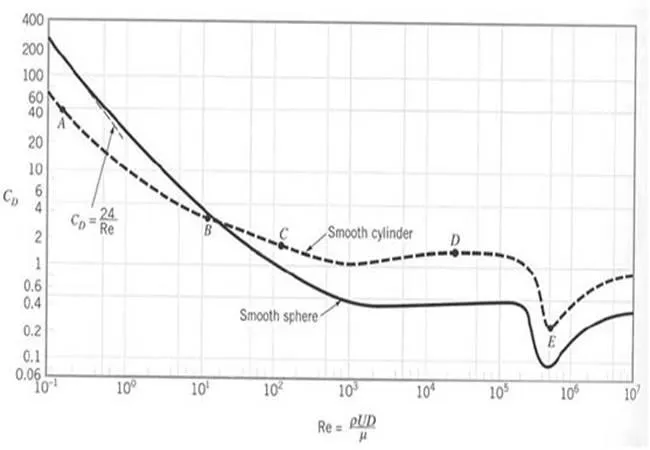
A: projected area of the element vertical to the direction of force.
q: air pressure.
a: angle between wind direction and axis of the exposed element.
ρ: air density 1.225 kg/m3
C: shape coefficient calculated from the equation.
C = KC∞
C∞: shape coefficient for elements with infinite length given in accordance with Reynolds number.
Re = DVtz/v
Graph 1: Shape coefficient C∞ as a function of Reynolds number (University of Waterloo, 2005).
K: Reduction coefficient of C∞ due to finite length of the element as a function of the l/d ratio where l is the length of the of the element and d is the dimension of the cross section (height or width) measured vertically to the wind direction.
l/d | 2 | 5 | 10 | 20 | 40 | 50 | 100 | inf |
Circular cylinder subcritical flow | 0,58 | 0,62 | 0,68 | 0,74 | 0,82 | 0,87 | 0,98 | 1 |
Circular cylinder supercritical flow | 0,8 | 0,8 | 0,82 | 0,9 | 0,98 | 0,99 | 1 | 1 |
Flat plate perpendicular to wind | 0,62 | 0,66 | 0,69 | 0,81 | 0,87 | 0,9 | 0,95 | 1 |
Table 1: Reduction coefficient k due to finite length of the element given as function of l/d (Mavrakos, 1999).
Vtz: Average value of the wind β speed at height z m from the average sea surface for time t which is calculated from the equation:
Vtz = αV1hr10(z/10)β
V1hr10 Average wind velocity value at 10m height from the sea surface for 1hr time.
α, β Values used when the average time used for velocity measuring is not the same as the one for V1hr10.
Coefficient | Average measuring time | |||||
1hr | 10min | 1min | 15sec | 5sec | 3sec | |
α | 1 | 1,06 | 1,18 | 1,26 | 1,31 | 1,33 |
β | 0,15 | 0,13 | 0,113 | 1,106 | 0,102 | 0,1 |
Table 2: α, β coefficients (Mavrakos, 1999).
For the purposes of this project we have taken into consideration:
Vtz: Average value of the wind β speed at height z m from the average sea surface for time t which is calculated from the equation:
D: = 5m
L: = 90m
a: = 90deg
V1hr10 = 9m/s (so that the velocity at the top of the tower is V = 12.5m/s which is the rated power of the turbine)
and the coefficients we choose from the graphs and matrices are
α: = 1
β: = 0,15
C∞ = 0,61
K: = 0,884
All the other values are calculated with the equations provided.
With the aid of MATLAB program we have produced the graph of the distributed wind load along the height of the tower using the force per meter equation:
Fw /dz = CqDsina
The distribution curve is as illustrated below:
Distributed Wind Load.
As we can imagine the force is bigger as we get higher from the sea level. By integrating the force along the height of the pile we get the total force which is Fp=3201 N.
Wind loads on rotor
As far as the force on the rotor is concerned, we have run a BEM code to calculate the overall thrust load on the blades. We assume a 6MW turbine with 130m diameter. First we define the blade geometry using a typical aerofoil profile for wind turbines:
Blade profile option, 3 blade on rotor.
The output data at a rated speed of 12.5 m/s are shown below using the BEM prediction code:
Output data using BEM prediction code.
We can see that the total force on the rotor is quite significant with its value being Fr=867771,7 N.
By repeating the same procedure for higher speeds we have the summarized results:
Summarized results for higher speeds.
Thrust load MN / CT.
Power MW / Blade pitch angle, deg.
The procedure here was to operate turbine at constant rotational speed, so that tip speed ratio was adjusted as wind speed was varied. This procedure is called feathering and it is used so that maximum power is obtained at each speed. Beyond rated speed of 12.5 m/s, the blade pitch was varied to maintain power constant at about 7.2 MW (with 83% conversion of mechanical power to electrical). As we can see from the results, rotor thrust in fact reduces as a result of the blades being set to run at very small angles of attack (low lift and low drag). Thrust coefficient Ct falls dramatically as a result (Ragheb, 2009).
Another way of controlling wind turbines and keeping power output at the rated value when the wind speed goes up is passive stalling, where the blades turn gradually the other way and avoid the abrupt stalling as the wind speed reaches its critical value. We can see that now the thrust loading goes up as the wind speed rises, but not significantly. It increases a little and then stabilizes at a relatively high value. Thrust coefficient falls but not so dramatically as in the case of feathering. The results from the code as well as the pitch angle and thrust graphs can be seen below where we note that the thrust load for the rated speed is the same for the two approaches (Ragheb, 2009).
the pitch angle and thrust graphs.
Blade pitch angle, degrees.
Rotor thrust load, MN.
Thrust Coefficient CT.
Wave loads
For the calculation of the force on a body (one jacket leg in our case), which is in a non-permanent flow of a real fluid, the inertia forces (Froude-Krylov and radiation forces) and the drag forces are combined .This assumption was made from Morison who calculated the force per meter of a cylindrical body with the presence of harmonic waves. For a hydrodynamically thin body (D/λ <1/5) the difraction forces can be neglected and so from Morison equation we have:
Fx = CF1sin(ωt) + CFD |cos(ωt)|
CF1 = – 1/8cM ρg πD2H sinh(kd)/cosh(kd)
CFD = 1/16cD ρgDH2 2kd + sinh(2kd)/sinh(2kd)
cM: inertia coefficient
ρ: water density 1025 kg/m3
g: standard gravity 9.81m/s2
D: cylinder diameter
H: wave height
k: wave number which is calculated by the equation:
k = 2π/λ
λ: wave length
d: water depth
ω: wave frequency which depends on the water depth and can be calculated with the following equations:
k = 2π/λ
shallow | intermediate | deep |
ω2 = k2gd | ω2 = kgtanh(kd) | ω2 = kg |
kd<π/10 | π/10<kd<π | kd<π |
T: wave period where
T = 2π/ω
cD: resistance coefficient
For the purposes of this project we have taken into consideration South West of England Regional Development Agency, 2006 and Coastal engineering technical note, 1985:
H = 5m
D = 1,05m
D = 40m
λ = 45,52m
Cm = 3
Cd = 1,5
All the other values are calculated with the equations provided.
Using the MATLAB program the force plotted along with the time has the following form:
Wave force (N).
We can see that the maximum value of the wave load is Fw=65299.3 N.
By multiplying this force by 2 we will have, in approximation, the total force of the two legs at the wave front. So Fw=130598.7 N. Of course we must not forget in reality The angle of the wave may be different between these two legs, brackets will also accept significant wave forces as well as the other two legs will accept radiation forces.
Again with the aid of MATLAB program we have produced the graph of the distributed wave load along the height of the tower using the force per meter equation:
Fx(Z) / dz = -cM ρπH2/2 D/4 ω2cosh[k(z+d)]/cosh(kd) sin(ωt)
+ cD ρ/2 D H2/4 -cM pπH2/2 D Hω2/4 ω2coshω2[k(z+d)]/sinhω2(kd) cos(ωt)|cos(ωt)|
As the equation depends on time we have plotted the amplitude of the force using the transformation
Fx = Asin(ωt) + Bcos(ωt)==> Fx = Ccos(Ωt)
where
C = √A+B
The distribution curve is as illustrated below:
Wave distributed Load.
We can see that the maximum force is closer to the sea surface, as the amplitude of the motion decreases with depth.
Tidal Stream loads
One more load at the jacket leg that could be taken into consideration is from tidal. Most wind farms though are not in areas with strong currents, so the forces produced are fairly small. The current speeds that could be encountered in such places are around 1m/s. Also, as the forces from currents are exerted below the water surface and so they do not exert a large bending moment that could be a dangerous load to the structure.
The calculation of the current force will be made using the drag equation which is presented below:
FC = 1/2Cd ρU2A
where
Cd: drag coefficient as a function of Reynolds number, here taken approximately 0.38 (Graph 1)
Re = DU/v
v: kinematic viscosity of water, here taken 1,307??10?^(-6) m^2/s (The Engineering Toolbox website) at temperature of 10? (National Oceanographic Data Center website)
ρ: water density 1025 kg/m3
U: stream velocity, here taken as 1m/s uniformly distributed
A: is the reference area
So the total force along the jacket leg is Fc=8179.5 N.
As a conclusion we can say that the wave load and wind load of the rotor are of the same magnitude, but in our case the latter is about seven times bigger. The force on the pile can be considered relatively small in comparison with the others. Also, load from currents as well as wind load on the pile is comparatively not important and given the fact that it does not generate big bending moments it is not a major factor in design. So to sum up, wind load is probably the one that need to be taken into serious consideration when designing and building an offshore wind turbine.