The design of marine propellers, or “props,” involves a series of trial-and-error testing to balance the vessel, engine, shaft, and blades (among other factors) to find the best optimal efficiency for that particular craft. Advances in the past couple of decades with the advent of computers and the ability to perform computer simulations have drastically improved how testing is done. But design achievements aside, many of the fundamental principles remain the same.
The Basics of Propeller Design
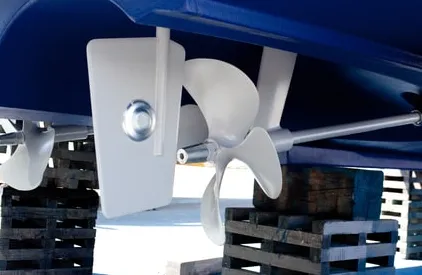

With marine propulsion, the motor drives a horizontal shaft to create a torque that then turns the blades. There are typically between two and six blades on each marine propeller. The void they create while turning fills with water and pushes the boat forward. Nearly all marine props are of a screw propeller design and are designed with a variety of materials, typically aluminum, steel, or brass.
1. Optimize the Number of Blades
A lesser amount of blades tends to equal a higher theoretical efficiency while a larger number increases the propulsion. As blades are added to the design, they increase the amount of drag but improve the ability to move water, resulting in a smoother (and less vibrational) motion. Choosing an optimal number of blades is especially important in performance craft as their hull design is more greatly impacted by it. Determining the number of blades based on the type of vessel, size, and intended performance characteristics is one of the important initial aspects of efficient propeller design.
2. Select a Low RPM of Compatible Frequency
A low RPM design can increase the efficiency of a propeller by up to 10 to 15 percent. A challenge in choosing an appropriate RPM is to ensure that the rotational speed is different than the resonant frequency of other vessel components such as the shaft and hull. The selection of RPM goes hand-in-hand with diameter as an important input to optimize fuel efficiency, as well. There are various sets of simulations and calculations that can be used to identify an optimal RPM range for a particular target marine design.
3. Select Propeller Diameter Based on Vessel Specs
The diameter of the propeller, defined as the diameter of the circle traced around the tips of the blades, has a direct impact on power. As with most factors in prop design, there is a balance to be struck, and the diameter should be optimized based on the expected power delivered to the shaft from the engine and the RPM. Generally, power increases and RPM decreases as the diameter of the propeller is increased. Because of this, larger vessels and those carrying heavier loads could benefit from larger diameters, while performance vessels built for speed may benefit from smaller diameters. The larger diameters become necessary as horsepower increases.
4. Skew Blade Shape for Reduced Noise
There are two sides to each blade on a prop, the leading edge that cuts through the water as it turns, and the trailing edge which follows. One design concept popularized by the Navy is to curve the leading edges of the blades on the prop, instead of leaving them symmetrical. This has the effect of extending the arc of the blade during rotation, which minimizes the effect of cavitation, thereby reducing drag which can have a positive benefit to the efficiency.
5. Find an Optimal Pitch

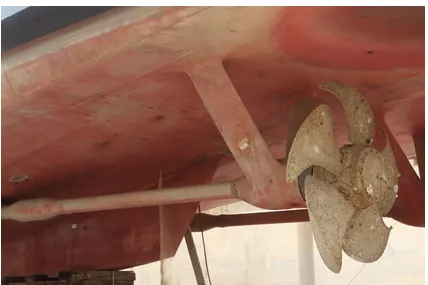
The pitch is defined as the forward movement of a propeller as if it was moving through a solid object (picture it as a screw). It is measured as a length and referred to as “true” pitch if the pitch length between the leading and trailing edges of the blade are the same and “progressive” if there is a low pitch for the leading edge and longer pitch for the trailing. Since pitch has a direct impact on RPM for any given vessel, it can be used to optimize the performance. There are benefits and drawbacks to true and progressive pitch designs and they should be considered in the context of all the other parameters being balanced.
Modern marine propeller design is very much an art and requires an intense focus on theoretical design considerations and real-world applications given particular vessel and engine designs. Even though the basic components of marine props are essentially the same and have been optimized in terms of their basic design, their parameters can be altered to have a dramatic effect on overall performance. The best designs take into consideration all of these factors. Engineers and designers who can work with a number of different vessel applications often lead to greater innovations.