The rotational power of a ship’s propeller is determined by the power produced by the marine engine to rotate the crankshaft. The crankshaft of the main engine is supported and connected to the connecting rod via main Bearings whose main function is to transmit the load without any metal to metal contact.
This is achieved by choosing special materials for manufacturing main bearings which float the journal pin of the rotating crankshaft when lube oil is supplied to it.
Forces on Bearings
A ship engine comprises of heavy rotational parts which exert different forces on various parts of the engine crankshaft. One of the significant load-bearing parts of the crankshaft system is the main bearings.
The bearings in a marine engine are subjected to multiple forces which include:
– Gas pressure generated inside the liner
– Dynamic Inertial forces due to different reciprocating and rotating motion of the engine parts. – Centrifugal forces due to different reciprocating and rotating motion of the engine parts
– Friction between the crankshaft and bearing due to engine vibration
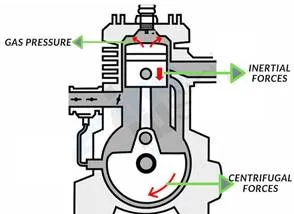
The main bearing is thus designed to tackle various forces along with supporting the crankshaft rotating at high speed. Hence, the material used in making the bearing is essential so that it can support the crankshaft journal and also adjust to minor surface irregularities.
The engine bearing cannot do the work alone. They need a compatible lubricating oil to bear the load and allow the rotation of crankshaft journal smoothly. The lubricating oil enables the bearing to withstand abrasive particles which create friction between journal and bearing.
Properties of main bearing materials
For selecting the main bearing for a marine engine, it must have the following features:
· It should be anti-corrosive in nature to avoid corrosion of bearing material and associated parts such as journal and bearing keep
· It should be frictional resistant so that there is minimum energy loss between the bearing and the journal
· It should have an excellent load-bearing capacity as dynamic load acts on it
· It should have good running in and grinding-in ability
· The bearing must support the oil film which allows smooth rotation of the journal
· The bearing material should be such that it does not react with the lubricating oil
· The bearing should have suitable embeddability property so that small particle embed in the bearing surface without harming the journal pin
· The bearing material should have an excellent compressive and tensile strength
· It must have a thermal resistant property to avoid any damage if it’s running hot
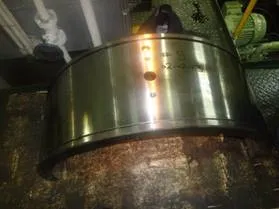