· Development of hull multipurpose polymeric materials with unique property package and development of manufacturing technologies of large-sized shaped and curved structures;
· development of high-strength polymeric materials for machine building and instrument making industry products (anti-friction carbon fiber-reinforced plastics and electrically insulating glass-reinforced plastics) and development of manufacturing technologies of sliding friction unit parts including with operating temperature up to 2000С, antenna domes, radio and radar facilities, ship propulsor parts;
· development of spherical plastics, vibration-absorbing and waterproof anti-skid polymeric composite materials and coatings;
· development of advanced technologies of their use in machine building, bridge engineering, pipe-line transport;
· development of heat-insulating, structural finishing and furniture materials for compartments, enclosures, cladding and interior finishing of ships of all types, classes and purposes, marine oil and gas production facilities;
· development of systems of electrochemical and integrated protection against corrosion of hulls, shaft and screw system and ship tanks, marine facilities and metal-intensive equipment operated in sea water including under ice conditions;
· selection of paint materials and development of optimal protection systems of anticorrosive, antiicing and antifouling paint materials for above-water and underwater hull structures of ship and marine facilities, ballast tanks, ship indoors and outfitting elements.
Hull multifunctional polymeric composite materials
One of main task of shipbuilding is a reduction of consumption of structure and part materials with simultaneous increase of service life and reliability. Solution of this problem is largely ensured by use of polymer composites having a number of advantages over traditional shipbuilding materials (wood, metal) – non-magnetization, impenetrability, radio- and sound transparency, water resistance, low density, high specific strength and rigidity, endurance capability (service life is 30 years and more).
Research and Production Complex team has a long experience in development and use of polymers and polymeric composite and hybrid materials for shipbuilding of all classes and purposes and construction of marine facilities.
In1964 in the country based on materials and technologies for the first time worldwide the Research and Production Complex performed a serial building of trawlers with glass-reinforced plastic hulls with draught more than 200 tons.
Beginning from 1967 a serial building of trawlers with glass-reinforced plastic hulls was performed based on the PN-609-21M styrole-free polyester resin. More than 100 trawlers were built and a part of them were delivered to foreign countries. Effective life of trawlers with glass-reinforced plastic hulls achieved 38-40 years. Over a period of their operation a wide experience and data on operability, reliability, serviceability and some economic parameter were obtained; this experience is used by the Institute specialists in works on further improvement of materials and technologies of ship hull structures manufacturing from polymer composites.
Work strategy of new generation polymer composites creation was based on development of three-layer structure material with base layers made from fire resisting glass-reinforced plastic with different intermediate layer of low density. According to examination results a polymer three-layer structure composite with an intermediate corrugating reinforced layer made from plastic foam. Together with Krylov State Research Center comprehensive tests of specimens and structures made from new three-layer polymer composite were performed. Production of the FOM-II phosphorus-containing monomer was mastered together with Volgograd Khimprom OJSC and production of the MOK organometallic catalysts was mastered together with SKTB Tekhnolog to ensure construction of ship erection and hulls from three-layer polymer composites.
Deck erections from three-layer polymer composite ensure reduction of a structure weight by 50-60 % compared with a steel structure and by 10-15% compared with an aluminium structure as well as increase a ship stability and a hull fire safety compared with an aluminium hull.
Structural polymeric materials based on a polyester resin binder filled with hollow ash microballoons and an environmentally friendly styrol-free glass-fiber reinforced polyester were developed for building of sport and pleasure boats, structures of amusement park and other consumer packaged goods; combined machine roofing and machine parts, acoustically-treated panels in productions shops with high noise level.
![]() | ![]() | |
Pleasure boat made from glass-ash-sphero-glass-reinforced plastic | Boat made from styrole-free glass-fiber reinforced polyester |
Anti-friction carbon fiber-reinforced plastics
In the 80-s of the 20th century attention to ecological cleanness of sliding friction units of modern ships, hydraulic turbines, pumps, flood gates and oil-production equipment operated in water was increased sharply.
![]() | ![]() | |
Anti-friction carbon fiber-reinforced plastics |
For the first time in global practice our specialists solved a problem of creation of anti-friction carbon fiber-reinforced plastics of the UGET and FUT types, having an unique set of tribotechnical, physical and mechanical and processing characteristics, with strength, wear resistance, shock resistance, dimensional stability, manufacturability at the level of metals but contrary to them capable to operate without lubrication or with water or aggressive liquid lubrication.
Technology of manufacturing of heavy-duty high-speed sliding friction units with diameter of 2.4 meters for marine auxiliaries and systems, hydraulic turbines and pumps as well as application in valve industry, heavy engineering and other branches.
Spherical plastics, vibration-absorbing and deck antiskid waterproof materials
Spherical plastic is a light high-strength material ensuring a buoyance of deep-water and underwater facilities. Our specialists achievement is a development of high-technology spherical plastics for deep-water manned and unmanned systems with immersion depth up to 6 km. Volume of buoyancy blocks achieves 3 m3.
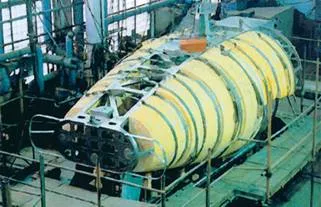
Buoyancy blocks for deep-water manned vehicle on shipbuilding ways
According to contracts with MP Mostotrest Bridge Construction Authority, Lenmostostroy JSC, JSC «Mostostroy №6», Defor LLC protective waterproof coatings based on polymer bituminous composition and technology of their application were developed.
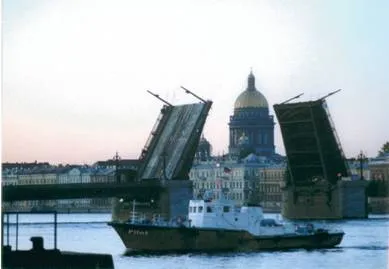
St. Petersburg bridges. Wear-resistance coatings and waterproofing compound of structure
Materials and technologies manufactured and delivered by us with our technical support were used for application of wear-resistance coatings and waterproofing compound of structure of more than 20 brides in St. Petersburg (Blagoveshchensky, Dvortsovy, Troitsky, Lyteiny, Bolsheokhtinsky, Volodarsky, Grenadersky, Sampsonievsky, Bolshoy Krestovsky etc.) and other municipal facilities of St. Petersburg. In particular arrangement of anti-skid waterproof coating of stylobate (2000 m2) of Navy Museum on the Spit of Vasilyevsky Island was performed.
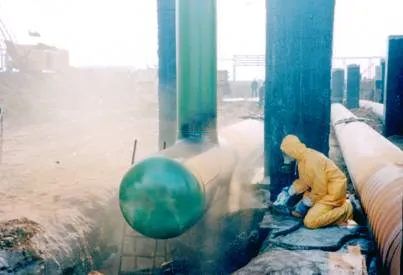
The BIURS spray coating system for main gas pipelines
The BIURS spray coating system for main gas pipelines was successfully developed and implemented.
Heat-insulating and structural finishing materials
Use of environmentally friendly, non-toxic and flameproof heat-insulating and structural finishing materials in living accommodations of ships and marine facilities is one of main conditions for comfort and safe life environment and safety of life in sea in accordance with International Convention Solas-74.
In collaboration with companies of related branches more than 30 new grades of competitive heat-insulating, structural finishing and furniture materials complying with up-to-date requirements of national shipbuilding and IMO international safety requirements were developed and implemented that allowed to provide shipbuilding yards with required materials.
Development of noncombustible asbestos-free materials is one of main task which was successfully solved. Such materials were developed and enjoy wide application in shipbuilding. Among these are the Neva BA deck mastic coverings, the OMP-BA fire-resistant coating, the TIMM-K mastic compound where asbestos is replaced with basalt, glass and multisiliceous fibers.
Institute has Certificate of Conformity to Requirements of Register of Shipping of Russian Federation entitling to make conclusions on possibility of use of non-metallic materials in ships in a part of constructive fire protection and fire resistance tests.
Electrochemical cathodic and galvanic protection against corrosion of ships, marine facilities and equipment operated in sea water
FSUE CRISM “Prometey” being a Russian leading organization in protection against sea-water corrosion has a long experience in development and use in shipbuilding and fleet of electrochemical cathodic and galvanic protection systems of hulls, shaft and screw system and ship tanks, ships, marine facilities and equipment operated in sea water including under ice conditions.
Beginning from 60s over a period of more than 40 years from the start of works almost all vessels built in the country, ships and marine facilities were equipped with means and systems of electrochemical cathodic and galvanic protection of hulls, shaft and screw systems and cargo and ballast and ballast tanks and different purpose vessels developed by FSUE CRISM “Prometey”.
About 4000 t of protectors from aluminium and zinc alloys were used annually; more than 100 serial produced superships including supertankers such as Krim and Pobeda, lighter-carrier ships such as Aleksey Kosygin, transport refrigerator vessels such as Bukhta Russkaya, fishery base such as USSR Semicentenary, bulk carriers such as Nikolay Zhukov and Geroi Panfolovtsy, Sevmorput atomic lighter-carrier ship, floating docks such as Dvina were equipped with cathodic protection system.
Feedback with fleet existing at that time expressed in author supervision of mounting and operation of used electrochemical cathodic and galvanic protection systems allowed to not only approve their high efficiency but obtain operational data for the further improvement. Experience and scientific engineering potential formed the basis of further development of electrochemical protection systems and expansion of scope of application.
Over the last years in order to provide in-service reliability of marine facilities used under ice conditions of the Arctic and Far East basins (atomic icebreakers, offshore ice-resistant oil and gas production platforms) special and second to none ice-resistant platinum-niobic anodes with increased mechanical and chemical resistance were developed ensuring a possibility to extend service life of cathodic protection up to 25-30 years.

Ice-resistant Pt – Nb anodes with texturized platinum coating on the Prirazlomnoye oil and gas production platform caisson body
Performed research studies showed demonstratively a potential of use of bimetal consisting of niobic support with texturized platinum coating with a desired crystal orientation for work electrode of cathodic protection anodes. Advantage of such coating developed to special technology by means of ion-plasma spraying in vacuum and magnetic field of platinum particles with size of 0.1-10.0 nm is a quantum jump of main performances of anodes: increase of adhesive properties of platinum-niobic work electrodes, reduction of platinum consumption at increased current density and extension of service life.
Paint coatings
Paint coatings still are one of main means of anticorrosive protection for metal structures.
To estimate efficiency of used paint coatings the Research and Production Complex specialists developed methods of accelerated tests allowing to forecast reliability and endurance of tested coatings under specific operating conditions: above-water shipboard structures, ship indoors, underwater hull, ballast tanks.
Specialized laboratory of the Research and Production Complex performs the following:
· selection of paint coatings and development of optimum paint coating systems for hulls, outfitting elements and items;
· development of operating procedures of surface preparation and application of paint coatings;
· engineering support of paint works;
· training and certification of personnel performing visual and dimensional inspection of paint work quality;
· certification tests of paint coatings as per quality performance for compliance with normative and technical documentation requirements;
· accelerated laboratory tests of paint coatings in case of use of new paint coatings and polymer structural materials with forecast of their life under service conditions.
Over the last years the laboratory developed and approved two procedures of accelerated tests of polymer composites:
· for polymer structural materials;
· for unloaded polymer composites;
Laboratory of paint materials and accelerated tests as part of the Sudatomenergotest Laboratory of CRISM “Prometey”. At the suggestion of Russian Maritime Register of Shipping the test laboratory of CRISM “Prometey” performs preparation to certification by Register as an independent test center of corrosion-resistance coatings.