Pure Iron is almost never used as a cast material because it is soft and weak. As the carbon content increases to 0.9%, so does hardness and strength. These alloys are called βSteelsβ.
The carbon content of Cast Iron ranges from about 2% to 4% and it is the form that the carbon takes in the structure which has a major influence on the properties and subsequent applications of the material.
A very small amount of the carbon is dissolved in the pure iron matrix. This component of the microstructure is known as Ferrite. Further amounts of carbon can either form Iron Carbide, [Fe3C], which is hard and brittle, or Graphite, which is almost pure carbon and is soft and has little strength. The form the carbon takes is determined by the rate of cooling during solidification, by the influence of other alloying elements and by subsequent thermal treatment.
Where there is little or no graphite in the structure the cast iron is very hard and brittle. These alloys are known as White Iron because of the characteristic silvery fracture, in contrast to the grey fracture where graphite is present. Where larger proportions of graphite are formed, the shape and size of the graphite has a significant effect on the properties of the cast iron.
Other elements which are present in the alloy affect the form of the graphite and the structure and properties of the material matrix.
Typical Cast Iron Microstructures
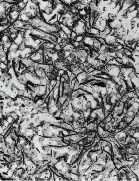
Grey Iron (x50)
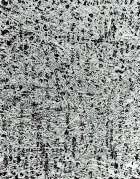
White Iron (x50)
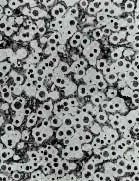
Ductile Iron (x50)
Comments are closed