Do you know how diesel engines are started in ships? Equivalent in size to a four-story building, the main propulsion engine is started with the help of compressed air at a pressure of 30 bar. Learn more about where a ship gets its compressed air supply from.
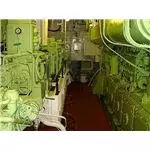
We discussed diesel engine starting problems in our previous article and saw how various methods are used to overcome this problem. We also saw how a marine engine is different due to its size and location, and that compressed air is the solution to starting the diesel engine.
As you know that a ship is a mobile power plant or a moving mini-city. It has all facilities, sometimes better than what we find ashore.
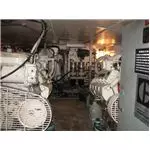
These moving giants have a pre-designed and erected compressed air system, which facilitates many activities onboard a ship. There are mostly 4 to 8 and sometimes 10 air compressors found onboard. These air compressors take suction from the engine room atmosphere which is already under a slight positive pressure. These air compressors compress the air in stages and fill up the huge air bottles, which acts as accumulator. They compress usually up to 30 bar and keep the air bottles filled up all the time. The number of air bottles and its volume(capacity) depends on the power (size) of the main propulsion engine. Air compressors are of varying capacity and used as per the requirement onboard.
Role of Compressed Air on a Ship
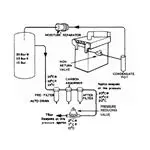
The role of compressed air onboard is of a very vast nature. Every ship will have a “DEAD-START” or “The FIRST START” arrangement. This is nothing but when the ship is totally “Dead” i.e, with out any power and no machineries running and no compressed air in the air bottle to start the generator engine(auxiliary diesel engine), then a provision is given for every ship to get the air bottle filled up to bring back the ship to safe, normal, working condition. This is provided either by a “Emergency Air Compressor” driven by a small diesel engine or electric motor getting its power supply from “Emergency Generator”. The various uses of compressed air onboard ship are listed below:
1. To start main propulsion engine
2. To start Auxiliary diesel engine(power generation)
3. To blow ship’s whistle
4. For Engine Room general service and cleaning.
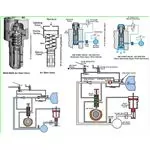
5. For the operation of pneumatic tools
6. For deck services, to carry out chipping.
7. For Automation & Instrumentation of various machineries,
8. For fresh & sea water hydrophores,
9. Fire alarms & operation of Quick closing Valves,
10. For Soot Blowing Exhaust Gas Economizer
11. And more!
Compressed Air System Layout
The compressed air system onboard typically has a set of 4 to 6 compressors, out of which 3 will be main are compressors, 2 service air compressors & one topping up air compressor. The Emergency air compressor is not to be counted as a normally used machinery.
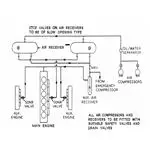
Main air compressors: These are used only when a ship enters or leaves a port, mostly during maneuvering only. They are of higher capacity of all. During maneuvering, these compressors when put in use, fills up the air bottle faster than other compressors, thus enabling the ship to berth herself in the port.
Topping-Up air compressors: These are comparatively of lesser capacity than the main air compressors. They are just used when the ship is sailing in the mid-seas where the consumption of air is very less (only for engine & deck services).
Service Air compressors: These are general service air compressors, which are used either for engine or deck service. They are of lesser capacity and their are designed for their pure strict oil free air quality. These compressors are used for pressing up the control air bottle and thus the control air of high purity is used for various automation purposes in the engine room and the pump room for oil tankers.
There may be set of main air bottles, service air bottle and a control air bottle for their respective purposes. The system also incorporates many pressure reducing valves and driers(de-humidifiers) to get rid of the moisture present in the compressed air.
Starting of an Auxiliary Diesel Engine
The auxiliary diesel engine is mostly started with the help of compressed air,depending upon the size of the engine. Other means of starting includes Electric start(battery) and air motor(engaged in the flywheel). The most common method is the use of compressed air. The lay out for starting the auxiliary engine is given below.
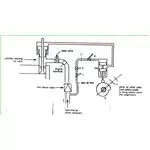
Before starting the auxiliary engine, the following safety checks must be carried out:
1. Turning gear disengaged(if available).
2. Lubricating oil sump level normal
3. Turbocharger oil level( both turbine & blower)side normal
4. Lubricating oil priming pump running.
5. Fuel oil/diesel oil booster pump running.
6. lube oil, cooling fresh water, fuel oil pressure normal.
7. Rocker arm tank level normal.
8. All valves in compressed air line open to the engine.
Referring to the above starting diagram of an auxiliary engine, the” main air” from the main air bottle arrives at the air starting valve. There is a tapping from the main air starting line, “pilot air” going to the starting air distributor. When the engine rotates, the camshaft also rotates which in turn rotates “the starting air distributor cam”. This cam is designed as per the firing order of the engine such that, the distributor rotates and lets the pilot air to the particular unit. The pilot air reaches on top of the air starting valve, opening it, in turn making the long awaited main air to let inside the combustion chamber. The main air which is at 30 bar, pushes the piston down making the crankshaft to rotate. This leads to continuous rotation of the crankshaft making the engine to achieve the minimum r.p.m at which firing of the injected fuel takes place. When the engine picks up on fuel, the air is cut off and drained. Thus the auxiliary diesel engine is started with the help of compressed air.
In the next article, we will take up the study of the various valves mentioned in the starting air systems namely master air starting valve, cylinder valves and so forth.
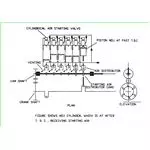