Usually all smaller ships are single bottomed, as they do not need a double bottom to withstand the load of the cargo. In these ships, the plate floors (see the figure to understand the context of ‘Floors’ in shipbuilding) themselves act as the stiffening members of the bottom shell plating. Plate floors (as shown in the figures) constitute transversely running plates at every frame spacing.
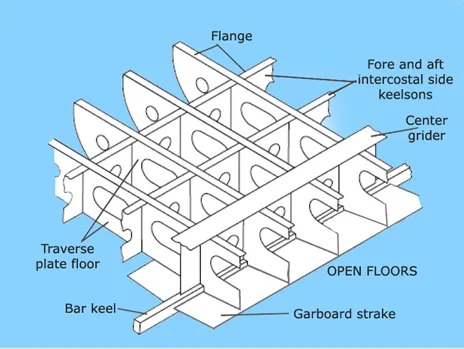
Figure 1: Single Bottom (transversely framed)
Note how the upper edge of each plate is flanged to increase the bending strength of the plate floor. Now, fall back to the basics for a while. When the hydrostatic pressure under the bottom shell exerts a bending moment in the bottom shell, the plate floor takes up the bending stress. So, designers treat all such members taking up bending stresses as beams. Empirically, the bending moment in a beam increases with the increasing span. So, what if we could reduce the span of the plate floor to further increase its stress capacity?
This is why, intercostal girders are used (see the image). The number of intercostal girder would however increase with increasing beam of the ship, since that would also result in increased length of a plate floor.
A uniform wood ceiling is provided on top of all the plate floors, to provide stowage of cargo. But that doesn’t make it a double bottom structure as the wood would not take up any stresses exerted onto the bottom structure.