The controlled movement of parts or a controlled application of force is a common requirement in the industries. These operations are performed mainly by using electrical machines or diesel, petrol and steam engines as a prime mover. These prime movers can provide various movements to the objects by using some mechanical attachments like screw jack, lever, rack, and pinions etc. However, these are not the only prime movers. The enclosed fluids (liquids and gases) can also be used as prime movers to provide controlled motion and force to the objects or substances. The specially designed enclosed fluid systems can provide both linear as well as rotary motion. The high magnitude controlled force can also be applied by using these systems. This kind of enclosed fluid based systems using pressurized incompressible liquids as transmission media are called as hydraulic systems. The hydraulic system works on the principle of Pascal’s law which says that the pressure in an enclosed fluid is uniform in all the directions. The Pascal’s law is illustrated in the figure.
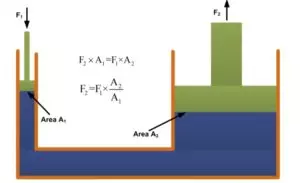
The force given by fluid is given by the multiplication of pressure and area of cross-section. As the pressure is same in all the direction, the smaller piston feels a smaller force and a large piston feels a large force. Therefore, a large force can be generated with smaller force input by using hydraulic systems.
Working:
The hydraulic systems consists a number of parts for its proper functioning.The schematic of a simple hydraulic system is shown.
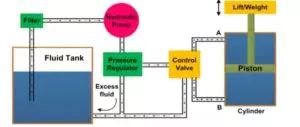
It consists of:
• a movable piston connected to the output shaft in an enclosed cylinder
• storage tank
• filter
• electric pump
• pressure regulator
• control valve
• leakproof closed loop piping.
· The output shaft transfers the motion or force, however, all other parts help to control the system.
The storage/fluid tank is a reservoir for the liquid used as a transmission media.
· The liquid used is generally high-density incompressible oil. It is filtered to remove dust or any other unwanted particles and then pumped by the hydraulic pump.
The capacity of the pump depends on the hydraulic system design. These pumps generally deliver constant volume in each revolution of the pump shaft. Therefore, the fluid pressure can increase indefinitely at the dead end of the piston until the system fails.
· The pressure regulator is used to avoid such circumstances which redirect the excess fluid back to the storage tank. The movement of piston is controlled by changing liquid flow from port A and port B.
The cylinder movement is controlled by using control valve which directs the fluid flow. The fluid pressure line is connected to the port B to raise the piston and it is connected to port A to lower down the piston. The valve can also stop the fluid flow in any of the port.
The leak-proof piping is also important due to safety, environmental hazards and economical aspects.
Hydraulic Pumps:
The combined pumping and driving motor unit is known as a hydraulic pump. They can be of two types:
1. Centrifugal pumps: Centrifugal pump uses rotational kinetic energy to deliver the fluid. The rotational energy typically comes from an engine or electric motor.
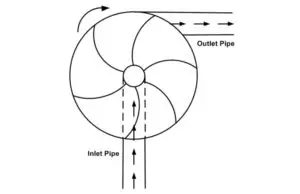
2. Reciprocating pumps: The reciprocating pump is a positive plunger pump. It is also known as positive displacement pump or piston pump. It is often used where relatively small quantity is to be handled and the delivery pressure is quite large. The construction of these pumps is similar to the four-stroke engine.
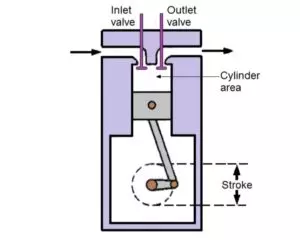
Applications of hydraulic systems:
The hydraulic systems are mainly used for precise control of larger forces. The main applications of the hydraulic system can be classified into five categories:
1. Industrial: Plastic processing machinery, steel making and primary metal extraction applications, automated production lines, machine tool industries, paper industries, loaders, crushes, textile machinery, R & D equipment and robotic systems etc.
2. Mobile hydraulics: Tractors, irrigation system, earthmoving equipment, material handling equipment, commercial vehicles, tunnel boring equipment, rail equipment, building, and construction machinery and drilling rigs etc.
3. Automobiles: It is used in the systems like breaks, shock absorbers, steering system, wind shield, lift, and cleaning etc.
4. Marine applications: It mostly covers ocean-going vessels, fishing boats, and navel equipment.
5. Aerospace equipment: There are equipment and systems used for rudder control, landing gear, breaks, flight control and transmission etc. which are used in airplanes, rockets, and spaceships.
Advantages and disadvantages of Hydraulic Systems:
Advantages:
• The hydraulic system uses incompressible fluid which results in higher efficiency.
• It delivers consistent power output which is difficult in pneumatic or mechanical drive systems.
• Hydraulic systems employ high-density incompressible fluid. The possibility of leakage is less in a hydraulic system as compared to that in a pneumatic system. The maintenance cost is less.
• These systems perform well in hot environmental conditions.
Disadvantages:
• The material of storage tank, piping, cylinder, and piston can be corroded with the hydraulic fluid. Therefore one must be careful while selecting materials and hydraulic fluid.
• The structural weight and size of the system is more which makes it unsuitable for the smaller instruments.
• The small impurities in the hydraulic fluid can permanently damage the complete system, therefore one should be careful and suitable filter must be installed.
• The leakage of hydraulic fluid is also a critical issue and suitable prevention method and seals must be adopted.
• The hydraulic fluids, if not disposed of properly, can be harmful to the environment.