The rotational power of a ship’s propeller is determined by the power produced by the marine engine to rotate the crankshaft. The crankshaft of the main engine is supported and connected to the connecting rod via main Bearings whose main function is to transmit the load without any metal to metal contact.
This is achieved by choosing special materials for manufacturing main bearings which float the journal pin of the rotating crankshaft when lube oil is supplied to it.
Forces on Bearings
A ship engine comprises of heavy rotational parts which exert different forces on various parts of the engine crankshaft. One of the significant load-bearing parts of the crankshaft system is the main bearings.
The bearings in a marine engine are subjected to multiple forces which include:
– Gas pressure generated inside the liner
– Dynamic Inertial forces due to different reciprocating and rotating motion of the engine parts
– Centrifugal forces due to different reciprocating and rotating motion of the engine parts
– Friction between the crankshaft and bearing due to engine vibration
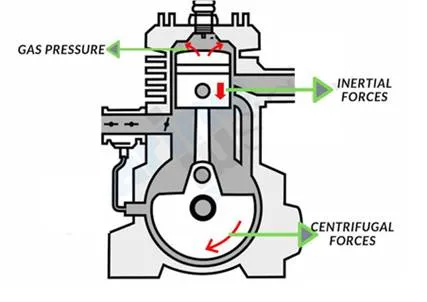
The main bearing is thus designed to tackle various forces along with supporting the crankshaft rotating at high speed. Hence, the material used in making the bearing is essential so that it can support the crankshaft journal and also adjust to minor surface irregularities.
The engine bearing cannot do the work alone. They need a compatible lubricating oil to bear the load and allow the rotation of crankshaft journal smoothly. The lubricating oil enables the bearing to withstand abrasive particles which create friction between journal and bearing.
Properties of main bearing materials
For selecting the main bearing for a marine engine, it must have the following features:
· It should be anti-corrosive in nature to avoid corrosion of bearing material and associated parts such as journal and bearing keep
· It should be frictional resistant so that there is minimum energy loss between the bearing and the journal
· It should have an excellent load-bearing capacity as dynamic load acts on it
· It should have good running in and grinding-in ability
· The bearing must support the oil film which allows smooth rotation of the journal
· The bearing material should be such that it does not react with the lubricating oil
· The bearing should have suitable embeddability property so that small particle embed in the bearing surface without harming the journal pin
· The bearing material should have an excellent compressive and tensile strength
· It must have a thermal resistant property to avoid any damage if it’s running hot
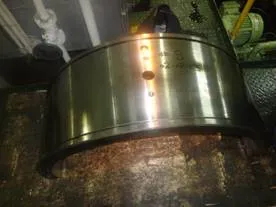
Related Read: Monitor Bearing Condition and Reduce Bearing Breakdown in Modern Marine Engines On Ships
Common defects in bearings
Corrosion: If the oil in which the bearing is placed is acidic, it may lead to corrosion. The surface of the bearing will become discoloured and rough due to corrosion
Abrasion: If the oil is not filtered and treated correctly and contains minute particles, which are common in engines burning heavy fuel oil, it may cause fine scratches on the bearing surface
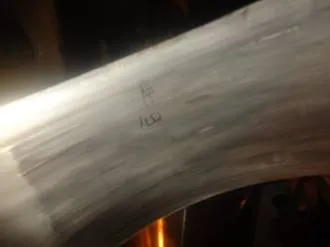
Erosion: When the oil supply pressure is not appropriate, or there is a rapid and unusual journal movement, it will lead the stripping of the overlay layer of the bearing. These phenomena are more common in medium-speed engines.
Fatigue: When the engine load over the bearing is too high, it may lead to the removal of the bearing lining. The bearing surface loads cracked paving.
Wiping: It is the process when the overlay layer removes due to high temperature. When the bearing is new, wiping is required to remove the initial layer, which helps in re-alignment of the bearing to the journal. However, too much metal wiping can lead to increase in clearances affecting the performance of the bearing
Spark Erosion: When the propeller is at rest, the stern tube, propeller shaft and bearings are in contact with each other. Similarly, main engine bearing and journal are in contact with each other, maintaining continuity of the circuit. When the ship is running, due to the rotation of the propeller and lubricating oil film the shaft becomes partially electrical insulated. It may also happen on the tail shaft using non-metallic bearing which acts as an insulation.
The propeller at the aft is a large area of exposed metal which attracts protective cathodic current which produces an arc while discharging from the lubricating film. This results in spark erosion of bearings, which can lead to a worse situation if lube oil is contaminated with seawater
Crankshaft misalignment: Crankshaft of a marine engine is a massive component when fully put together in the engine. Initially, the complete crankshaft is aligned in a straight line (connection drawn from the centre of the crankshaft makes a straight line) before setting it on the top of main bearings. But with time due to various factors, the straight line may deviate and misalign which can lead to damage to the main bearings
Hence, the increase in the clearance between the bearing and the journal pin can be due to the above-listed factor as well as the following:
-If the bearing is operated above the operating temperature for a longer period
-If there is significant and prolong variation in the engine speed, e.g. over speeding of the engine
-If the lubrication oil film thickness is reduced due to change in the oil flow
–If there is a change in the viscosity of the lubricant
-If the lubrication oil temperature is high
-If the lube oil used has a different load-bearing capacity than the recommended.
-There is a change in the engine ambient temperature.