An alternative to the traditional method of chocking using cast iron chocks, is the use of epoxy resin or resin chocks. The biggest advantage of using resin for chocking is the saving in time and man power, which earlier methods required.
Especially the time required for machining of foundation surfaces, which was very long, has now been cut down. The engine needs to be correctly aligned, with respect to the shafting, taking suitable allowance for compression of the chock (about 1/1000 of choke thickness).
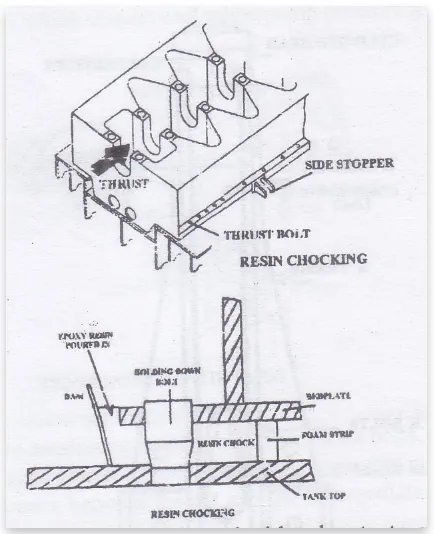
The surfaces are suitably cleaned with solvents, to remove all impurities like oil, rust and so on, which could affect the bonding. Dams are prepared to contain the resin, when it is poured in.
The holding down bolts are now fitted after spraying with a suitable releasing agent, to prevent the resin from adhesion. A slight head is given to the resin when pouring, so that it completely fills up the spaces. The deflections of the crankshaft should be checked, especially after the resin has set, to confirm that they are within the limits.
Resin chocking was initially developed as a repair technique, which considerably cut down the time (which would have been required for machining metal chocks).
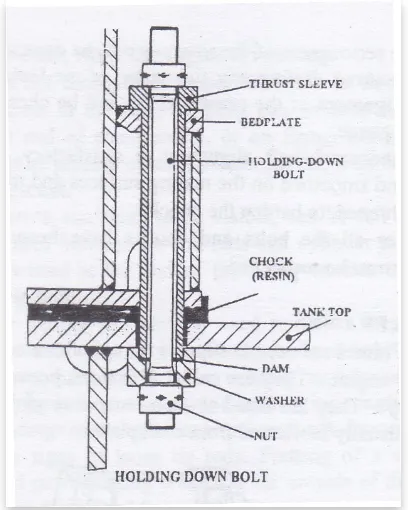
Resin curing will take place in about 18 hours, if the ambient temperature is between 18-25 degree Celsius. This can take up to 48 hours, if ambient temperature is lower. During the chocking operation, a sample of resin material from each batch is sent for testing purposes. This method lowers the bolt tension by a factor of 4, compared to metal chocks.
Comments are closed