There are several common reasons for high exhaust temperatures in marine diesel engines, but MOST causes can be attributed to a scavenge fire and/or a defective fuel valve, both of which are caused by a fuel system fault.
Articles here at Bright Hub have previously examined the fuel combustion process of
marine diesel engines along with the various types of process cycles, namely the diesel cycle, Otto cycle, and dual cycle. We also know that irrespective of the cycle, the exhaust process is a feature in all marine engines. The diesel exhaust gas temperature is already quite high because of being a product of combustion ignition, but it still it needs to be controlled within a reasonable range to avoid thermal stressing of other components.
The following sections explain the causes of exhaust gas temperature rise, the first section giving an overview of a modern two-stroke marine diesel engine exhaust valve design and operation.
Exhaust Valve Operation
Modern efficient two-stroke engines use a hydraulically operated exhaust valve where the spring action is provided by a pneumatic arrangement instead of mechanical spring. A closeup view of the action is shown below.
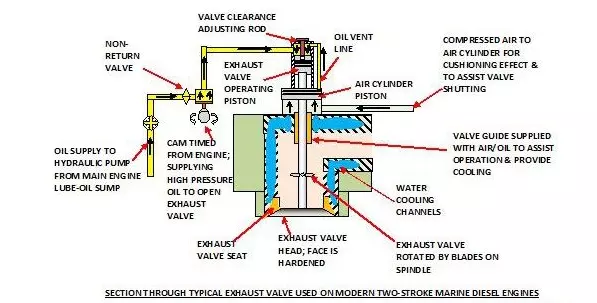
Design of Exchaust Valve Mechanism
Both the hydraulic action of oil and pneumatic pressure are used for operation. The function of the oil is to open the valve; it achieves this by using oil from the lube oil system of the engine. This is supplied by a hydraulic pump to a cam that is timed and set to open the valve, ejecting the exhaust gasses following combustion.
The role of the air is to assist in valve closure as well as to provide a spring-cushioning effect. The air is also mixed with a minute quantity of lube oil for lubrication purposes as well as keeping the valve guide cool through using a bleed-off from this air supply.
The exhaust valve is enclosed in a water cooled cage with fresh water being circulated through channels cast or machined within the cage. Valve rotation is achieved with the use of blades welded onto the lower end of the valve spindle. These projections rotate the valve by a small amount each time exhaust gases exit from the chamber, allowing uniform wear to the valve head and seat.
Materials of Construction
The exhaust valve cage is made of cast iron, as are the valve guides. These require a malleable, self- lubricating material due to the continuous action between the guide and the valve spindle. The valve seat is renewable and is made from a hard wearing material such as molybdenum steel while the spindle itself is made out of Nimonic, a superalloy comprised of nickel, chromium, titanium, and aluminum. The seating face of the valve is specially treated to increase its toughness/wear properties.
Symptoms and Causes of Exhaust Gas Temperature Rise
Any rise in the exhaust gas temperature outside the standard range has a great effect on the life of the exhaust valve and also on the wear of the piston rings and the cylinder liner. It is therefore important to be aware of the various symptoms and causes for an exhaust gas temperature rise in order to ensure that the temperature stays within in the safe zone. We have listed some of the most common causes here:
1. Increase in Engine Load
· The fouling and the deformation of the ship’s hull can increase resistance to a fairly great extent; liable to increase the engine load.
· Damage to propeller blades due to drifting wood or going aground, can subject the engine to an increased load.
2. Fuel Valve/Supply
· Exhaust gas temperature rises due to the enlarged nozzle hole of the fuel injection valve due to poor maintenance or inferior HFO supply.
3. Exhaust Valve Passing
· Valve head or seat badly damaged/worn causing blow-by of exhaust gasses on combustion.
4. Fouling of Exhaust Gas Passageways
· Combustion products build-up on the turbocharger nozzle and the surface of turbine blades, clogging the exhaust gas passage and reducing turbocharger efficiency.
· Clogging also increases back-pressure in the passageways to the turbocharger, restricting the efficient removal of the gasses.
5. Fouling of the Scavenge Air Passageways
· Fouling of the air-side due to oil mist on suction casing and the diffuser of the turbocharger.
· Clogging of cylinder liner scavenge port by combustion products.
6. Leakage of the Scavenge Air.
· Scavenge air supply can leak between the turbo-blowers and scavenge tableau, decreasing air supply pressure to ports.
7. Scavenge Fire
· A fire occurs in scavenging chamber due to build-up of lube-oil being ignited by a spark from a blow-by of piston rings
8. Insufficient /Unsatisfactory HFO Treatment.
· HFO requires extensive treatment through filtration, heat exchangers and centrifuging to remove water and particles.
9. Insufficient Air Supply to Blower
· Blower compressor suction filters clogged
· Insufficient air supply to blower
10. Exhaust Valve Timing Problem
· This can be caused by timing gear slipping of hydraulic/pneumatic supply to operating components