Numerous valves are used in the piping and machinery system of the vessel as per the need of the flow pattern of the fluid. All the valves used on vessels have the basic function of regulating the flow of fluid in pipes. Valves are used and applied to all machinery as flow regulating devices. Although valves are known as efficiency reducing device because they reduce the energy in fluid flow, their use is imperative in operations where limited flow is required. Thus, for any aspiring marine engineer it is very important to have a sound knowledge about the construction and working of various types of valves used on ships. Ships require valves to regulate and control pressure and flow of fluids in various systems on board. Valves have the capability of transporting liquids, gases, vapors and slurries or semi-liquid mixtures. Each type of valve has a specific function which includes
- Decrease/increase flow
- Regulate pressure
- Start/stop flow
- Relieve pressure from pipe systems
- Control the direction of flow
Valves are made up of a number of different components; first the valve body which holds all the components of the valve together, then there is a bonnet that covers the opening. The internal parts of the valve comprising of the stem, seating material, package, disc, plug and back rings etc. are together referred to as the valve trim. The discs of the valve are designed to throttle or stop flow and the seat for the discs is provided by the seal rings. Valve stem facilitates the closing of the valves.
Types of Valves
The types of valves used onboard ships are:
- Piston Valves
- Globe Valves
- Needle Valves
- Control Valves
- Diaphragm Valves
- Pinch Valves
- Butterfly Valves
- Gate Valves
- Ball valves
- Knife Gate Valves
- Check Valves
- Hydraulic Butterfly Valves
All the above listed valves are applied in different places and serve various functions. These valves are further categorized into different groups on the basis of their functions. Functions of valves are categorized into 4 main parts, namely:
- Regulation
- Isolation
- Specialized Purpose
- Non-Return
- Regulation: They are used for regulating the flow of fluid. Valves listed in this category are:
- Piston Valves
- Globe Valves
- Needle Valves
- Control Valves
- Diaphragm Valves
- Butterfly Valves
- Pinch Valves
2. Isolation: As the name suggests, they are used for the isolation of fluid. Valves listed in this category are:
- Piston Valves
- Gate Valves
- Ball Valves
- Diaphragm Valves
- Plug Valves
- Butterfly Valves
- Pinch Valves
3. Specialized Purpose: These valves are used for specialized purposes. Valves listed in this category of function are:
- Float Valves
- Knife Gate Valves
- Line Blind Valves
- Multi-Port Valves
- Flush Bottom Valves
- Foot Valves
4. Non-Return: These are commonly used when flow is not allowed to return back after passage. Check Valve is an example for the same.
Now we take a look at some of the important valve used onboard, separately for better understanding.
Gate Valves
These are one of the most common types of valves used onboard any type of vessel. They help in controlling the flow of liquid through the pipes by raising or lowering, similar to a gate. It is important to note that the gate valve can only operate in a no flow or a full flow condition and thus can have only one position. It gives full bore flow without change in direction; it is not suitable for operations which require the valve to be partially open. Gate valves have a simple design and function but also has a number of variations i.e. the rising stem type and the non-rising stem part.

In rising stem gate valve, the stem has threads which mate with the integral thread of the yoke or within the bonnet. When it is operated, the steam rises above the actuator and the valve attached to the stem open up. In non-rising stem type gate valve, the hate or the disc is itself internally threaded and connected to the stem of the valve. The stem threads mate with the disc and the valve will open or close without raising the stem like in rising stem type.
In order to avoid any kind of leakage through the space around the spindle in the gate valve gland packing is used. In the long run gland packing gets damaged and thus has to be changed in regular intervals.
Gate valves are used in applications which require minimum pressure loss and also in applications which require bidirectional flow. The material which is usually used in the making of these valves is cast iron.
Globe Valves
These are linear motion valves designed to start, stop or regulate flow. The disc of the globe valve can completely be removed from the flow path which enables the flow or it can completely close the flow path which shuts the flow. This valve has 3 primary body designs, Tee Pattern (Z- body), Angle Pattern and Wye Pattern (Y-body); namely. These valves usually have rising stems and larger sizes are of the outside screw and yoke construction. Components of globe valve are similar to that of the gate valve. Globe valve has seats in a plane parallel or inclined to the line of flow.
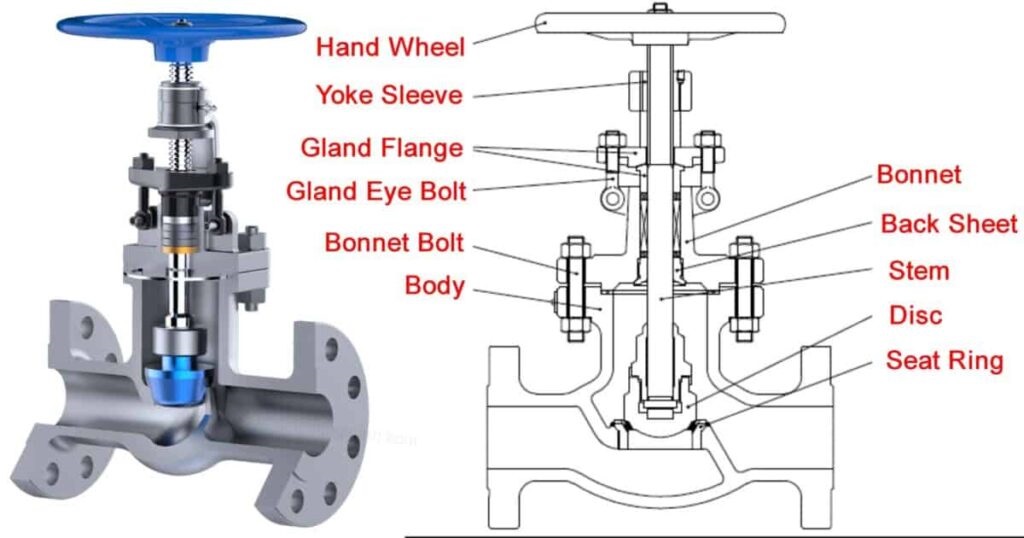
Globe valves are applied in systems where flow needs to be regulated, fuel oil systems which require regulation of flow and leak tightness. They are also used in feedwater, condenser air extraction, chemical feed and extraction drain systems. Globe valves possess various advantages. It has good shut off capability and moderate to good throttling capacity and has a shorter stroke compared to that of the gate valve. Due to the discΒ attached to the stem, globe valve can be used as a stop-check valve.
Butterfly Valves
These are lightweight valves used on vessels which operate with fuel, freshwater, lube oil or chilled water systems. For better understanding of this valve on can imagine a butterfly moving its wings. It is quarter-turn rotational valve which is employed to stop/start and regulate flow. These valves are made on the principle of a pipe damper. The element which controls the flow is a disk of approximately equal diameter to the inside diameter of the adjacent pipe that rotates on a vertical/horizontal axis. The valve is fully open when the disc lies parallel to the piping run and when the disc is perpendicular the valve is shut.

Butterfly valves are well suited for the handling of large flows of fluids at relatively low pressures and for the handling of slurries with large number of suspended solids. These valves possess a number of advantages over globe, plug, gate and ball valves; the most obvious ones being the savings in weight, space and cost. These valves also have a very minimal maintenance cost as there are only a few moving parts.
Relief Valves

These valves are designed specially to relieve pressure inside the pipes. When the pressure inside increases the spring inside the valve opens and relieves pressure. This spring can be adjusted such that the valve opens faster or slower as required. To prevent major damage to equipment, machinery and the worker relief valves release elevated pressures before they become extreme. They can be adjusted and regulated to pop off when internal pressure exceeds predetermined settings. Once the internal pressure reaches to normal level the relief valve closes.
Diaphragm Valves

These are bi directional on/off throttle valves and are used to control fluid flow by regulating the area with which media can enter and exit the valve, effectively changing its velocity and speed. A thin flexible membrane is used to control the opening and closing of the valve thus the name diaphragm valve. These are similar to pinch valves but they use a linear compressor which pushes the diaphragm into contact with the valve body. Diaphragm valves offer both discrete and variable pressure control and can be operated manually as well as automatically. They are also clean, leak-proof, easy to maintain, safe and effective valves which are best suited for moderate pressure and temperature operations which require start/stop fluid control.
Pinch Valves

It is a 2/2 way valve built to shut off or regulate the flow of corrosive, abrasive or granular media. Pinch Valve utilizes pressurized air to open or close the valve. the valve has no restrictions and allows a range of media to pass through the bore when in the open position. The valve consists of a flexible internal rubber sleeve which keeps the media isolated preventing the risk of contamination. These valves are best suited for granular products and are cost effective, reliable and easy to use.
Ball Valves

It is a shut off valve which controls the flow of fluid by means of a rotary ball having a bore. The medium can be blocked or flown through the valve by rotating the ball a quarter turn around its axis. Ball valves are characterized by a long service life and provide a reliable sealing over the life span, even when the valve has not been in use for a long time. In some special versions ball valves are used are control valves, this operation is less common due to the relatively limited accuracy of controlling the flow rate in comparison to other kind of control valves.
Comments are closed