On a ship, there are hundreds of machinery and systems which help in the day-to-day operations of the vessel. For the smooth functioning of these machines, lubricants are required. Lubricants play a very important role by overcoming and reducing heat, neutralizing acid combustion by-products, reducing friction and preventing scuffing. Reduction in friction is vital, as it reduces the wear and tear between two running surfaces.
Lube oil has various properties that have to be maintained, like viscosity, alkalinity, volatility, oiliness, detergents. It is important to maintain these properties of the lube oil to ensure that it is in good condition. Lube Oil doesn’t actually wear out but its lubrication quality tends to deteriorate with time, this mainly occurs due to contaminants such as dirt, sludge, metals and water to name a few. This contamination happens primarily due to:
- Jacket water leaking
- Cooler leakage
- Fuel contamination through poor atomization of fuel and also unburnt fuel.
- High exhaust temperature
- Burned cylinder oil
- Carbon from incomplete combustion and products of fuel composition
- Scale formation, wear and tear
- Biological Contamination
These contaminations need to be purified, in order to maintain the quality of lube oil, as it directly affects the equipment life and its productivity.
Impure (unpurified) lube oil on-board could prove to be hazardous for both the vessel, and it’s crew. Some of the common complications incurred, owing to impure lube oil are, reduction in the fuel efficiency, case crankcase explosion, reduction in load carrying capacity, corrosion in the metallic parts, formation of acid in trunk type piston engine, and more.
Hence, we require Lube Oil Purifiers on board ships for proper purification of lube oil, with minimum throughput or batch purification in case of heavy contamination.
What is a Lube Oil Purifier? (Definition)
A lube oil purifier is a mechanical device, that is used to separate impurities such as water and solid particles present in lube oil. There are three ways in which purification of lube oil can be performed:
- Centrifugation
- Filtration
- Coalescence
In this article, we would be discussing about the Centrifugation process, as, it is the most commonly used method of lube oil purification on-board vessels.
Reason why Centrifugation is preferred over other methods of purification:
- It removes water along with solid impurities in a single operation.
- Even the small particles are cleaned effectively.
- It requires minimal or very low maintenance which in turn enables for more process uptime.
- The cost of installation is low and the equipment has prolonged life.
A high-speed centrifugal purifier is installed on board ships to get rid of unwanted pollutants and contaminants from the lube oil. On board ships Centrifuges are preferred for lube oil purification. It is a purifier which separates two liquid substances based on the difference in their densities with the help of a gravity disc to separate solid and water.
Construction of Centrifugal Purifier or Centrifuge
The centrifugal purifier consists the following components:
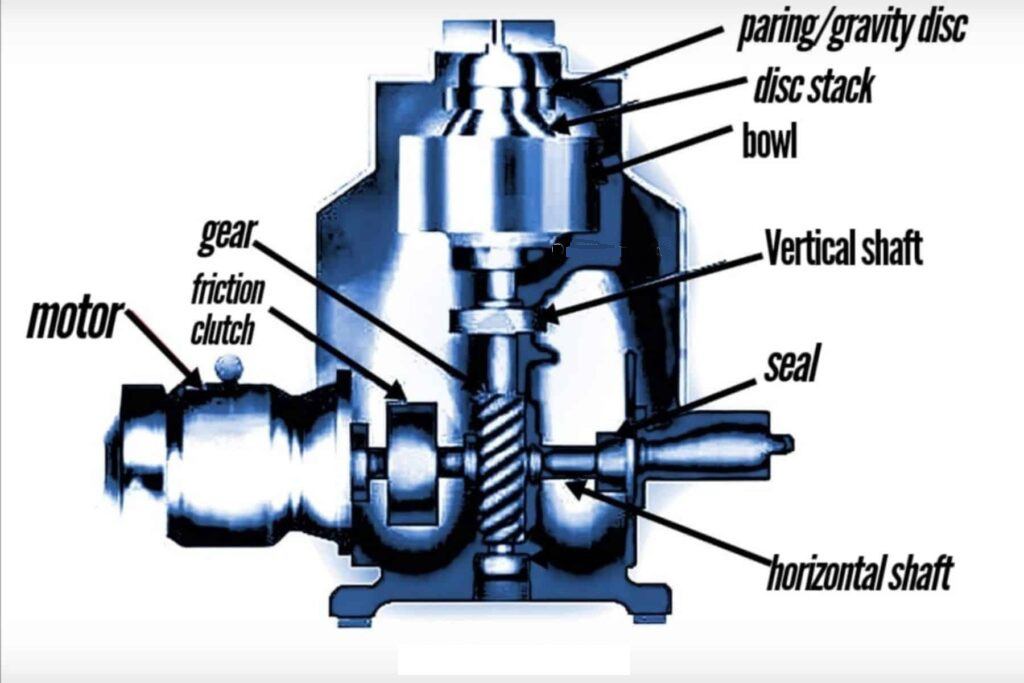
- Electric Motor: This motor is responsible for driving various components of the purifier such as the bowl, tachometer, gear pump via pinion gear and rotating counter.
- Friction Clutch: It is installed on the horizontal shaft so as to safeguard and protect the electric motor from damage as the complete purifier assembly is a bit too heavy for a motor to take the full load form the start without getting overheated. The friction clutch helps in safeguarding against heavy starting current.
- Gear Box: It consists of a friction clutch, motor shaft, the breaking lever, spur gear, worm gear and attached gear pump.
- The Bowl and Disc Stack: The bowl is a solid assembly manufactured of high tensile steel working within the purifier frame with ample space to collect and discharge sludge. On the other hand, disc stacks are incorporated with small holes in order to form the interface line and carry out separation using centrifugal force which causes oil to move inwards and water and other solid particles move outwards.
- Rotating Shaft and Automation: The electric motor with the help of bevel gears drives the bowl so as to produce high speed motor action. The vertical shaft felicitates the rotation of the shaft at a high speed while the spur gear connects with it with a horizontal shaft which is also driven by the motor through clutch plate or friction plate. The centrifugal purifier is provided with a full automation circuit involving three-way valves, detectors, transducers, monitors, solenoid valves, pneumatic valves etc., and a control panel that ensures that the centrifuge fulfills all the criteria required for operation in an automated unmanned condition.
- Gravity Disc and Pairing Disc: This is fitted on the top of the disc stack to create an oil-water interface based on the difference in their particular densities. While the pairing disc is the stationary impeller mounted in a chamber at the bowl’s neck so as to convert rotational energy of the liquid into the pressure head. The size of the gravity disc depends on separation temperature, the density of oil at the temperature and desired throughput of oil and by using of nomogram from the purifier manual; is responsible for setting the location of oil and water interface line variable as per marker’s design and the machinery need.
Working Principle of the Centrifugal Purifier
The centrifuge is one of the most important auxiliary equipment on board ships, which works on the basic principle of separation based on difference in the specific gravities of two different fluids.
The traditional method that is used is gravity separation but it takes time as gravity is the sole force responsible for settling out. Whereas, in a Centrifuge the gravitational force is increased is increased by the centrifugal force (5000 times higher) which increases the power of separation significantly. In purification based on centrifugation the contaminated water is discharged whereas the clean oil is directed back into the process. Particles contained in the separator bowl for later disposal are discharged automatically according to the installed/programmed operations.
Important Parameters
- Density of Oil: Lower the density of the oil better is the purification process.
- Feed Inlet Oil Temperature: The impure lube oil is passed through a heater, which causes an increase in temperature thereby lowering the viscosity, that insures better purification.
- R.P.M (Revolution per Minute): Maximum rpm of the bowl ensures enough centrifugal force of separation.
- Back Pressure: The back pressure varies with the properties of oil such as temperature, density and viscosity of the feed inlet. It needs to be adjusted as it ensures that the oil pairing disc is absorbed in the clean oil on the way of pumping it to the clear oil tank.
- Throughput of Oil Feed: The quantity of oil pumped into the purifier per-hour optimizes the operation, throughput should be minimum.
Checks Required Before Starting the Purifier (Prechecks)
Before starting the centrifuge, one must check:
- If the centrifuge is started after all the overhauling, it must be made sure that all fittings are fitted in a proper and appropriate manner and the bowler hood is properly locked with the help of hinges.
- Oil level in the gear case must be checked and should be made sure that it is half in the sight glass.
- The direction of rotation of the separator must be checked by switching the purifier on and off.
- The brakes must be in released position.
- It must be checked if the lines are set and the valves are open.
The processes are carried out as follows:
The contaminated/impure lube oil is supplied to the center from the settling tank and then with the assistance of centrifugal and gravitational force, the separation between oil and water takes the place of their specific density. Water being heavier, it is thrown out towards the side of the bowl whereas the oil being lighter is positioned at the center. Hence, an interface line known as E-line is formed between water and oil achieved with the help of the gravity disc at the outlet, which is very crucial for correct and proper operation. Numerous gravity discs, also known as regulating discs are provided with the purifier whose diameter is set/changed as per the properties of the lube oil.
Flow rate and temperature of the feed is very important for the process of purification. One stage purification is usually enough for normal oils. On the contrary for oils containing heavy impurities, catalyst mixtures or heavy sludge requires multiple purification with the assistance of set up of paralleled multirole purifies or the purifiers are set in series. Depending upon the automations and operations of the installed system the sludge is discharged either at time intervals or continuously. Systems dedicated to sludge discharge monitor the sludge slide and provide signal upon detection of any sorts of anomaly. Water washing is used to remove/wash off contaminants such as acids and salts from the lube oil. Water is injected into the lube oil before purifying at a rate 3-5% to that of the rate of flow that continuously renews the water seal in the centrifuge. The temperature of water is always maintained 5 degrees Celsius above the temperature of oil, while the temperature of oil is around 75 degrees Celsius.
Steam Jetting is a technique wherein the steam is blown into the engine lube oil which pairs to the purification by removing carbon and much more effectively through coagulation of colloidal carbon.
After Checks
- Temperature, back pressure and throughput should be adjusted whenever required or necessary.
- Gearcase level oil, general leakages, vibrations, motor amperes should be monitored properly.
- De-sludging must be done during the process as per the manual and after the stoppage of the purifier.
- Steam inlets should be shut.
- Brakes should be applied, for a complete shutdown of the centrifuge.
Maintenance
For smooth and accurate functioning of the ship auxiliary maintenance is important. Few ship owners employ a fundamental preventative maintenance policy, whereas the others operate on more sophisticated systems based on condition monitoring. The maintenance of Lube oil purifier depends upon the monitoring and lube oil sampling.
Overhauling must be done at regular intervals. Gravity disc must be chosen as per specifications. The lube oil feed system must be evaluated to ensure optimized operation. The sump tank must be cleaned if there is a case of heavy contamination and fresh oil must be fed to the minimal level. The piping system must be cleaned and the entire engine must be flushed in case solid contaminants are found.
Comments are closed