For proper working of any 3 phase induction motor, it must be connected to a 3 phase alternating current (ac) power supply of rated voltage and load. Once these three-phase motors are started, they will continue to run even if one of the three-phase supply lines gets disconnected. The loss of current through one of these phase supplies is described as single phasing.
The ship is fitted with hundreds of motor,s which are responsible for running different pumps, machinery, and systems. The critical machinery such as steering gear, main engine, generator, boiler etc. have 3 phase motors attached to them which run one or the other main or auxiliary system for them.
A 3 phase motor of 440V is, in general, the standard frame, squirrel cage induction type designed for AC 440v 3 phase of 60 Hz. Only small capacity motors of 0.4 KW or less, mainly used for lighting and other low power systems, are single phase motor of 220V 60 Hz operation.
Causes of Single Phasing
Single phasing is a power supply-related electrical fault in case of an induction motor. It occurs when one of the 3 phase circuits in a three-phase motor is opened; hence the remaining circuits carry excess current. This condition of Single Phasing is usually caused when:-
– One or more out of the three back up fuse blows (or fuse wire melts if the fuse is of wire type)
– The motor circuit has contactors which supply the current. One of the contactors is open circuited.
– A wrong or improper setting of any of the protection devices provided on the motor can also lead to single phasing
– If contactor routines are not performed regularly, they might get covered or get coated with oxidation layer leading to single phasing.
– The relay contacts for the motor is damaged or broken
– One of the wire for the motor circuit is broken
– Due to equipment failure of the supply system
– Due to the short circuit in one phase of the star-connected or delta-connected motor
– Feeder or transformer fuse blow-up
Effect of Single Phasing
As mentioned earlier, a three-phase motor is an AC motor which is built to operate on a three-phase power source. The construction of both types of a motor is similar as they both have a stator and rotator. The single phase motor does not have a rotating field, but one that reverses 180 degrees. Usually, single phase motors are not self-starting. For that, they use additional provisions like switching out the start winding or a capacitor.
Single phasing problem on a 3 phase induction motor will have the following effects:
– If the motor is in a stopped condition, it cannot be started as a single phase motor cannot be a self-starter (as explained above) and also due to the safety system provided in 3 phase motor to protect it from overheating
– If the single phasing faults occur while the motor is operating, it will continue to run (unless provided by additional safety cut-out system) because of the torque produced by the remaining two phases which is produced as per the demand by the load
– As the remaining two phase are doing additional work of the one default phase, they will be overheated which might result in critical damage to the windings
– The single phasing will lead to increase in the current flow by 2.4 times the average current value in the remaining two phases
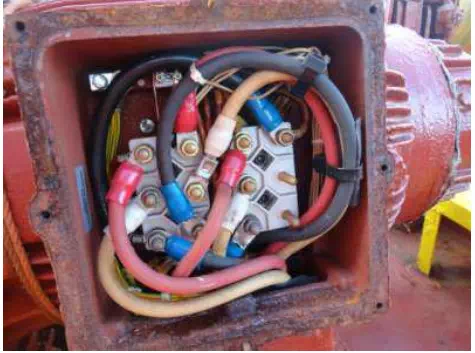
– Single Phasing reduces the speed of the motor, and its rpm will fluctuate
– The noise and vibration from the motor will be abnormal. This is the result of uneven torque produced by the remaining two phases
– Almost all the motor system in the ship has a standby arrangement. If the motor is selected for standby, with single phasing problem – It will not start leading to failure of the related system
– If the problem is not addressed and motor operation is continued, windings will melt due to overheating and can lead to short-circuiting or earthing
– In such condition, if the crew of a ship comes in contact with the motor, he will get an electrical shockwhich can even be fatal. Overheating of winding is primarily due to the flow of negative sequence current.
– It may cause overloading of the power generation machine, i.e. auxiliary engine, and its alternator
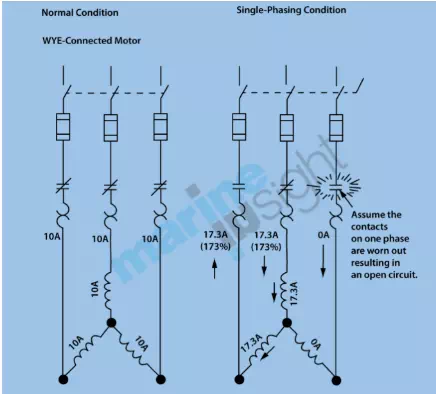
How to Protect Motor from Damage Due to Single Phasing?
Such a condition requires that the motor is provided with protection that will disconnect it from the system before the motor is permanently damaged.
All motors above 500 KW are to be provided with protection devices or equipment to prevent any damage due to single phasing.
The rule stated above does not apply to motors of the steering gear system installed on the ship. Only on the detection of the single phasing, an alarm will be sounded; however, the motor will not stop as the continued operation of the steering motor is essential for safety or propulsion of the ship, especially when the vessel is in congested waters or under manoeuvring.
The most commonly used protection devices for single phasing are:-
1) Electromagnetic Overload Device
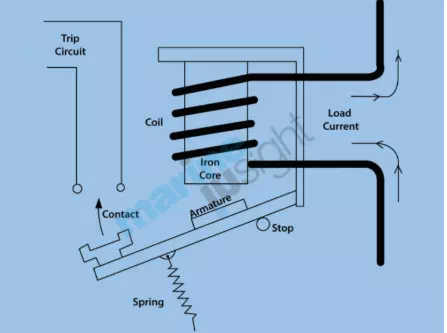
In this device, all the three phases of the motor are fitted with an overload relay. If there is an increase in the value of the current, then this relay activates automatically and the motor trips.
This device works on the principle of the electromagnetic effect produced due to the current.
As the current value increases, the electromagnet in the coil also increases which pulls the relay and activates the trip relay, and the motor is stopped.
The time delay is provided in this system because while starting the motor draws a lot of currents which can trip the motor.
2) Thermistors
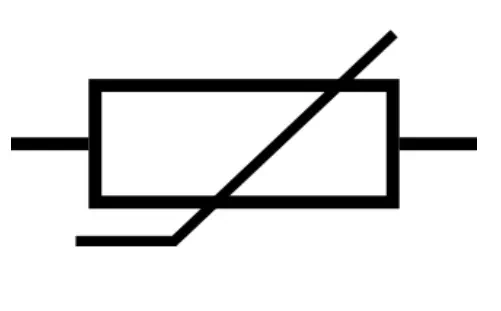
Thermistors are small thermal devices which are used together with an electromagnetic overload relay. The thermistors are inserted in the three windings of the motor. Any increase in the current will cause heating in the windings, which is detected by the thermistors that send signals to the amplifier.
The amplifier is connected to the electromagnetic relay. As soon as a signal is received from thermistor about overheating, this amplifier increases the current value in the coil of an electromagnetic relay which activates the trip and the motor stops or trips.
3) Bi-metal strip
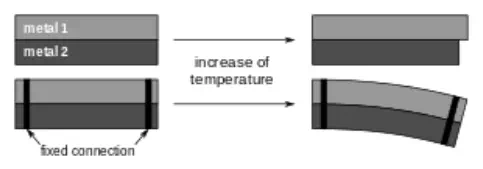
In this method, the bimetallic strip is placed in such a way that it detects the overheating in the circuit. As soon as overheating is detected, this bimetallic strip tries to expand due to two different metal used and because they have a different coefficient of expansion. The strip attempts to bend towards the metal having a high coefficient of expansion and finally completes the trip circuit and the motor trips.
4) Standard motor starter overload protection
It is provided in 3 phase motor to takes care of the single phasing condition. Overload heaters are provided in all the phases which detect any overload in the phase, and if the load goes far above spec for the motor, the heaters trip the starter off before the motor winding is damaged.