A freshwater generator is a vital machinery system used on board. It should only be operated by an experienced and trained technician. The technician should carefully study the instruction manual provided by the manufacturer to fully understand the working of the fresh water generator before carrying out maintenance, repair or trying to troubleshoot the equipment.
The maintenance schedule should be followed and checked regularly to avoid any unfortunate circumstances and ensure the smooth operation of the fresh water generator.
Precautions to be taken while operating Fresh Water Generators
1. While operating the freshwater distillate pump for the first time, the distillate present should be discharged overboard the ship for a minimum of 30 minutes.
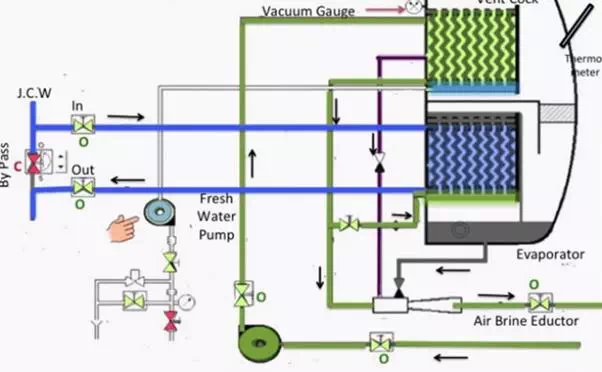
2. Fresh Water Generators should be stopped before the ship comes close to land, port or a river mouth. This is because the seawater in such locations may be contaminated with bacteria which can get mixed in the distillate generated by the machinery. There is hence a high chance that the Fresh Water Generator malfunctions when the ship is in the dirty sea.
3. The bottom blow valve should not be opened to restore atmospheric pressure in the evaporator. If this is done, seawater being used in the heater may be blown up and damage the deflector plates and other parts of the Fresh Water Generator.
4. For testing leakage in the evaporator, the vacuum gauge should be removed, or the main valve should be fully closed.
5. Before carrying out cleaning operations, the technician should carefully read and follow instructions as stated in the manuals provided by the manufacturer.
6. During cleaning and rinsing of the Fresh Water Generator, steam should not be used as the inside surface of the evaporator is covered with a coating material which can get ruined under the action of steam.
7. This coating material should be handled with a lot of care and should be washed off immediately if it comes in contact with skin.
8. To avoid leakages, the bolts securing the tube plates should not be removed or loosened.
9. The Fresh Water Generator should not be heated, and welding by an open flame has to be avoided to protect the coating present on the inside surfaces of the Fresh Water Generator.
10. To move the Fresh Water Generator from one place to another, the lifting holes present on the top cover should be used with wires of sufficient weight carrying capacity as specified in the assembly outline drawings present onboard.
11. The Fresh Water Generator can be damaged if it is run with a valve or cock in closed position installed on the steam drain outlet line. Hence these should not be incorporated on the outlet steam drain line.
The inlet of the ejector pump should always be filled with sea water.
Common Problems Faced in Fresh Water Generators with Possible Causes and Solutions
Low Rate of Distillate Generation
· The heating tubes or the condenser piping are fouled from the inside, and they need to be cleaned.
· Hot water temperature and or flow rate is low and needs to be increased by the operator.
· The cooling water flow rate may be low and needs to be increased according to the given specifications.
Dropping of Evaporation Temperature
· The temperature of hot water is low and needs to be increased to the specified level.
· Hot water flow rate is low and needs to be increased to the specified level.
The vacuum obtained in the evaporator has dropped
· There is an air leak present in the system which should be repaired and then tested at 0.05 MPa to make sure regular operation has been restored.
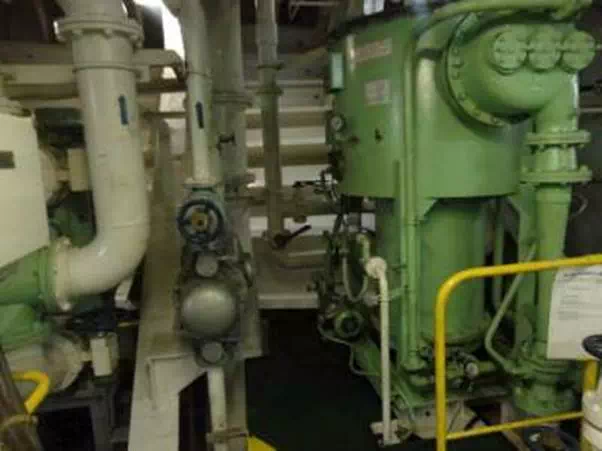
Malfunctioning of Water Ejector
· The nozzle of the ejector has closed partially or fully and needs to be cleaned
· The diffuser has worn out, or corrosion has taken place. It has to be replaced by a new one
· The nozzle has been worn out and needs to be replaced by a spare.
· The pressure at the outlet of the ejector is at 0.08 MPa or higher.
· The ejector outlet piping may be clogged and needs to be checked and corrected. The valve opening of the overboard discharge valve needs to be checked and repaired.
· The pressure at the outlet of the ejector is negative; the overboard discharge valve should be closed up to a certain degree.
The distillate is present in the Sight Glass
· This may indicate failure of the Distillate pump. It should be repaired.
· The outlet valve of the Distillate pump is in the closed position and hence needs to be opened.
· The outlet piping is clogged and needs to be cleaned
· The pump is drawing in air, and the mechanical seal needs to be replaced.
High Salinity of the Distillate
· The rate of generation of the distillate is too high and needs to be decreased by lowering the hot water flow rate.
· The temperature of evaporation is low (50 degrees or such). The vacuum adjusts valve needs to be closed to an extent such that the evaporating temperature increases.
· The Fresh Water Generator has been used in an area where the feed water is dirty and needs to be stopped.
· The reading of the salinity indicator is faulty and has to be checked using the indicator test switch; the electrode needs to be cleaned.
· The piping of the condenser has been damaged and needs to be plugged in appropriately.
Low Feed Water Rate
· The opening of the feed water adjusts valve is not sufficient and needs to be adjusted accordingly to increase the rate of feed water entering the system.
· The feed water orifice may be clogged, and its surface needs to be cleaned. There is insufficient internal pressure in the condenser piping and the condenser cooling water outlet valve needs to be closed to an extent.
High Feed Water Rate
· The feed water adjusts valve has a very large opening and needs to be closed sufficiently.
· The feed water orifice has been worn and needs to be replaced.
Problems Specific to Pumping Systems of FWG
Pump fails to start
· The electrical system or the motor has failed and needs to repair after proper inspection.
· The impeller has seized with the casing ring causing problems in starting the pump. In this case, the impeller and/or casing ring need to be repaired or replaced after carrying out inspections. After doing so, the centring of the pump and motor needs to be checked. The eccentricity of the shafts should be checked. Inspection of the bearings, balancing on the impeller and shaft coupling should be carried out.
The pump does not operate at the required head or capacity
· The pump is drawing in air through the suction system and this needs to be checked and tightened.
· The strainer at the suction pipe is clogged and has to be cleaned.
· The passage at the impeller is clogged and has to be cleaned. After carrying out the cleaning operations, the pumping system, including the casing, impeller, etc. should be inspected for any damage. The piping systems, including the suction and discharge, should be cleaned and if required, the strainer has to be replaced.
· The motor has been run in the reversed direction, and the wires need to be correctly connected.
· The motor speed has dropped, and the electrical system needs to be checked for faults.
· The clearing ring clearance has increased and needs to be replaced. The impeller should be inspected for damage and replaced if required. After doing so, the centring, shaft couplings, eccentricity and the ball bearing should be inspected for proper operation.
Water Flows after starting the pump but stops abruptly
· Air may be trapped in the system, and the piping needs to be corrected. The air outlet valve should hence be checked, and the suction pipe should be inspected.
· The stuffing box is drawing in air, and the mechanical seal needs to be inspected and repaired or replaced.
Overloaded Motor
· There is damage to the bearing and it needs to be replaced. After doing so, the centring of the motor and pump, the lubrication, shaft couplings, eccentricity and the ball bearing should be inspected for proper operation.
· The pump and motor are misaligned; hence the centring needs to be adjusted, followed by a proper inspection.
· The shaft has been deformed and needs to be replaced followed by proper inspection of the machinery.
· The motor or electric system us at fault and needs to be repaired and checked after inspection.
· The discharge volume is high and needs to be checked and altered according to the pump specifications.
The Pump begins to vibrate during operation
· The impeller is not balanced correctly and needs to be repaired or replaced.
· The Bearing has been damaged and needs to be replaced
· The motor is misaligned with the pump, and the centring has to be adjusted.
· The Shaft has been deformed and needs to be replaced.
· The pump has been incorrectly installed, and this needs to be corrected by the onboard technicians after carrying out investigations.
· If any of the above actions are performed, the centring of the motor and pump, the lubrication, shaft couplings, eccentricity and the ball bearing should be inspected for proper operation.
Overloaded Bearing
· The bearing may be assembled incorrectly or poorly; this needs to be checked and adjusted after which inspections need to be carried out. Fresh lubrication should be given to the system.
· The thrust experienced by the bearing is more than its specifications, and the impeller may need to be repaired or replaced. After doing so, the casing ring needs to be inspected. The balance hole of the impeller needs to be checked for blockage.
· The Bearing has been damaged and needs to be replaced
· The motor is misaligned with the pump and the centring has to be adjusted.
· The Shaft has been deformed and needs to be replaced.