Broadly, offshore structures maybe of two types:
1. Floating – These offshore platforms are floating in free surface and are movable from one location to another. Examples include semi-submersibles, SPAR platforms, Floating-leg platforms, drill-ships, FPSOs(Floating Production, Storage and Offloading systems)
2. Fixed Platforms: They are immobile and fixed permanently to one place. These sorts of offshore units have greater strength and relative durability as compared to floating ones. These are operationally irreversible as once installed they cannot be relocated . Examples are Concrete/Gravity Platforms, Jacket Platforms,Tension-leg platforms(TLPs), Jack-Up Rigs etc.
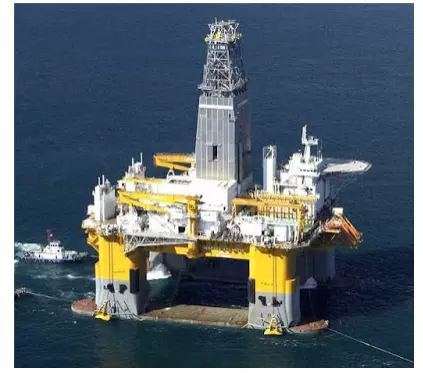
Fig.1:Image of a deep-sea offshore installation |
Surveillance of the sea-bed and that of the underlying rocks helps in the development of the strategic sites for the optimum extraction of the resources. Furthermore, the oceanographic and climatic conditions around that region are assessed. Then the topographic conditions pertaining to that particular region along with the critical risk factors probable to the given sea-state gives the outline for the apt installation for the site. The offshore structures maybe mobilized from one site to another, may be erected after compilation of the raw materials and parts or maybe made from scratch at the purported site itself depending on its nature.
As these offshore structures are high-budget, heavy-duty and long-term projects, umpteen care is taken to ensure its livability in hostile sea state and its long term life span.
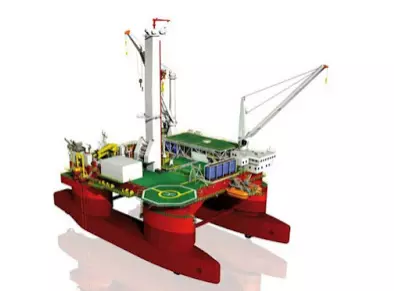
Fig.2:Image of a semi-submersible offshore installation |
Jacket Platforms
These platforms are quite common and comprise of an outer jacket-like structure of welded tubular steel. Steel jackets are vertical sections made of tubular steel members, and are usually piled into the seabed. The pipes are about 1 to 2 m in diameter and have a maximum penetration of about 100 m. They weigh about 20000 tonnes. This external steel jacket has many functions ranging from stability and supporting the entire structure to protecting the internal piping and drill equipment from external disturbances.
Design Parameters
These steel jackets have tapering, truss-like structure with high strength, durability and fatigue resistance.Loading and life cycle apart from diameter, penetration, thickness and spacing are taken into account.
ยท In a typical design , the cross-sectional dimensions are about 70*65 at the seabed and 56*30 at the top.
ยท They have capacities of resisting forces up to 50 MN in compression and 10 MN in tension and has a large vulnerability to lateral loads like expansion and hydrodynamic stresses.
ยท They also have a maximum permissible overturning moment up to 10 GN.m in most cases.
The jacket design and the pile design are the crucial factors in determining the total performance of the structure and the total cost in its design and maintenance can devour up to 40-50% of the total cost estimation.
One point to ponder upon in jacket structure is the protection of the steel from rust and corrosion, a “disease” of all marine vehicles and structures which is principally to be taken care of . This can be done up to a certain extent by using high-grade “stain free” steel and by repeated cathodic protection.
Jack-Up Rigs
Jack-Up drilling rigs are a type of self-elevating, mobile platform capable of raising the hull part which is obviously buoyant above the sea level and penetrating its steel legs into the sea-bed for support for deep sea drilling operations. The name “jack-up” is derived from versatile nature of the legs or jacks which can be suitably jacked above or below the hull accordingly when not in operation and when in operation.
These Legs maybe piled into the sea-bed or maybe placed on large footings for better grip and stability. There maybe three or four legs for jacking up the buoyant hull above the sealevel for operations. After a stipulated time period after termination of the operations at a place, the legs are dismantled from the sea floor and are jacked above the hull and the entire unit is mobilized to another destination maybe to some jetty/port or to another drilling site. They are not self-propelled and usually depend on tugs of Heavy Lift Ships for towing from one place to another.
Well when and where can jack up rigs be used? The answer IS that they maybe used in shallow waters as pre-operation and post-operation mantling and dismantling of the jack ups are very bleakly feasible in deeper waters. The steel legs are of high strength HSS steel and are designed to confront wave dynamics even in rough seas up to a certain limit. Care must be taken for their maintenance in terms of corrosion, fatigue, stresses. In case of sea or external parameters going beyond the tolerance level, these are immediately “jacked up” and are shifted to safer locations or kept in a safe nonoperational, dormant mode.
Jack -Up rigs are used specifically for oil well drilling purposes and has limited or no storage capacity. Storage or bulk transport may be through oil tankers or the multi-purpose FPSOs (Floating Production, Storage and Offloading Units).
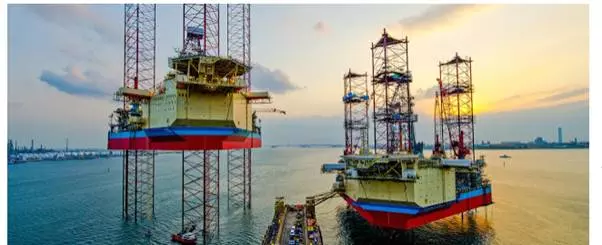
Fig.3: Basic Components of a Steel Jacket Offshore Structure |
Comments are closed