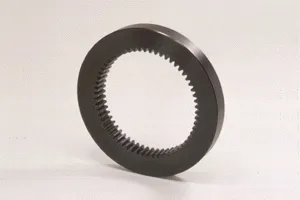
Internal gear is a gear with its teeth cut in the internal surface of a cylinder and meshes with spur gears.
In its manufacturing, because of its shape, the usual hobbing machine used in spur gear production cannot be used. Generally it is made with gear shaper (or gear shaping machine) equipped with a pinion cutter. More recently, the efficiency of internal gear cutting has been improved by a different process called skiving.
As it is seen from the precision class of JIS N9 of KHK’s SIR ring gears, due to the thinness of the ring, it is sometimes difficult to produce high precision. On the other hand, gear grinding to improve precision grade is limited by the number of manufacturers and their available grinding facilities leading to very high cost.
Also, although it is generally too expensive to make helical teeth internal gears, KHK has made it possible to produce them by adopting equipment that can cut them by simply making pinion cutters and not needing helical guides.
Normally, internal gears can be used with the same module spur gears, depending on the number of teeth combinations, but it is necessary to note the possibilities of getting involute, trochoid or trimming interferences. For using KHK’s standard stock gears, please consult the PDF formatted “Technical Information of Internal Gears” section for usable number of teeth combinations.
Internal gears are often used in applications involving planetary gear drives and gear couplings. There are three major types of planetary gear mechanisms: planetary, solar and star types. Depending on the type and the pattern of which shafts act as input and output, many variations of speed transmission ratios and rotational directions are produced.