Over the years there have been significant research and development in the field of propeller designs to ensure safety of goods, passengers and the crew, and at the same time saving a lot of money by increasing its efficiency.
Propulsion systems for surface ships and underwater vehicles have followed the standard propulsion mechanism for many years. Propellers have to be designed in a way to reduce noise and vibrations and hence cavitation to the lowest possible level in order to achieve propeller efficiency. Modifications made in the basic propeller geometries do not change the way we determine and analyse propeller performance
Basically, a propeller design is carried out by one of the two following methods:
ยท First of all, based on the results of the open-water tests on a series of model propellers. The different propellers tested have varied parameters such as number of blades, blade area, pitch ratio etc. Based on these results and the requirement of the vessel, the parameters can be selected to obtain the suitable design.
ยท The second method involves doing the old way! i.e., using the first principle. This involves finding the chord length, section shape, pitch etc., then finding the torque, thrust and the efficiency. This method is used to design propellers which require features other than the regularly designed propellers, like propellers which are needed to work in an uneven wake pattern or which is heavily loaded and liable to cavitation.
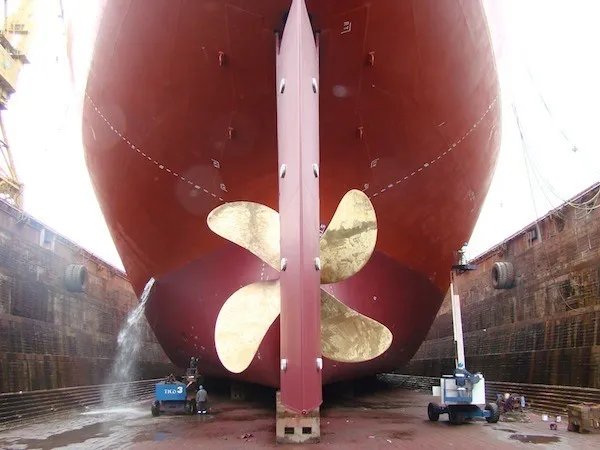
A propeller design should be initiated only after the design criteria is selected. The design criteria acts as a boundary condition to the propeller design. While designing a propeller various factors should be kept in mind so as to design a very efficient propeller. The following are the factors that help in improving the propeller efficiency.
1. Propeller Diameter
It is observed that the speed of the shaft and the propeller diameter are very closely related. A low shaft speed (given diameter) is very beneficial from efficiency point of view. However, it leads to high shaft torque subsequently large shafts and gearboxes. Therefore, while designing the propeller a balance must be found to ensure its performance.
Generally, propulsive efficiency can be increased by installing propellers with large diameters. However, the diameter behind the ship is limited by the draught of the vessel. Optimization of propeller design is done to meet the balance.
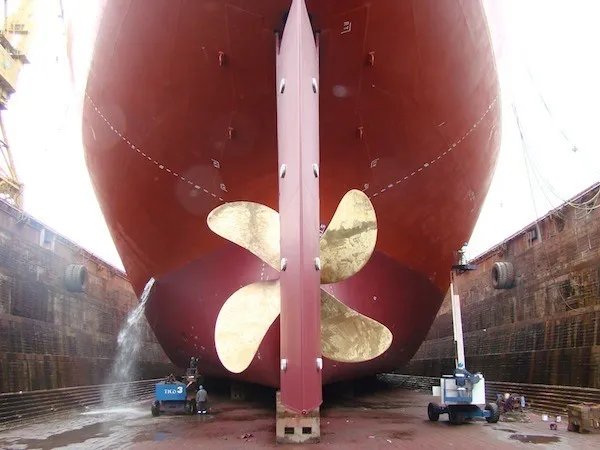
2. RPM
Selection of RPM of the ship plays a very important role in the propeller design. The rotational speed chosen for the vessel must be different from the resonant frequencies of the shaft, hull and other propulsion machinery. It is often seen that low RPM design increases the propulsive efficiency by 10 to 15 percent.
3. Number of blades
The number of blades chosen has an effect on the level of unsteady forces acting on them. Considering the efficiency point of view, optimum open water efficiency increases with increase in the number of blades.
4. Blade Outline
Blade outline plays a very important role in propulsive efficiency. Research and experiments using propellers with various blade areas have shown that efficiency increases by decreasing the blade area. This is because the frictional drag increases with increased blade area. However, it should be kept in mind that the strength of the propeller cannot be compromised by decreasing the area to large extent. Tip of the propeller has to be kept narrower in order to ensure efficient flow of water through the blade.
5. Angle of Attack & Camber
The design of angle of attack of the propeller and its corresponding chamber depends on the design lift which has to be determined by the naval architect. If a larger angle of attack is chosen then the section designed would be less susceptible to pressure side cavitation and more susceptible to suction side cavitation. The reverse also holds true if the angle of attack is decreased.
6. Pitch/Diameter ratio
To achieve the best propulsive efficiency for a given propeller diameter, an optimum Pitch/Diameter ratio is to be found, which again corresponds to a particular design rate of revolution.
Apart from the conventional changes in the parameters of the propeller in order to achieve higher efficiency, there are certain external components which help in improving the flow around the propeller, hence, improving propulsive efficiency. They are as follows โ
7. Stern Tunnels
These devices help in reducing the wake peak effect for ships having V-shaped sterns, thus reducing the effect of vibration. They are horizontal hull appendages placed above the propeller, they deflect the water towards the propeller ensuring even flow through the propeller.
8. Schneekluth ducts
These type of devices redirect the flow to the upper portion of the propeller disk thus equalising the effect of wake and improving hull efficiency. These are also capable of accelerating the flow by means of the aerofoil shape cross section. This is done by creating a low pressure area in front of the duct which is achieved through its design.
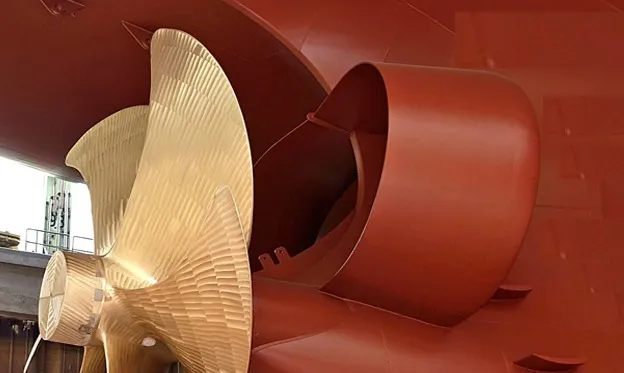
9. Grouches Spoilers
Their function is to redirect the flow horizontally in towards the propeller. They are small curved triangular plates welded in front, top and side of the propeller. These were designed to prevent the formation of keel vortices for U-shaped stern ships.
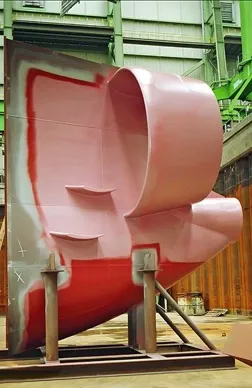
10. Rudder Bulb System
Kappel propeller comprises of smoothly curved extended blade tip towards the suction side of the blade which reduces the energy loss from the tip vortex flow. Integrating a rudder bulb and flaring the Kappel propeller hub cap will provide additional reduction in the energy loss from hub vortex and drag from the hub-rudder profile. The rudder bulb system also reduces cavitation increasing the total efficiency of the propeller assembly. A Kappel propeller and a rudder bulb system is designed for a target ship and accordingly engine is selected as per the power/ rpm requirement. It is important to properly optimize these two parts to achieve improvement in fuel saving, efficiency and reduction in emission.
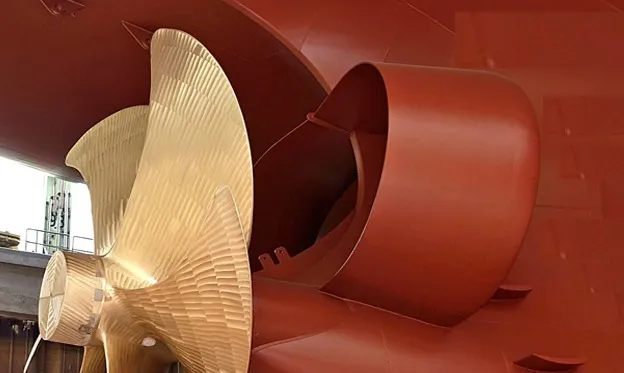
Apart from the points discussed above, it is really important that the designer check for serious cavitation problems at various stages of design.
Comments are closed