Ships marine diesel engines run on heavy fuel oil (HFO) nowadays a low sulfur content, or marine diesel oil (MDO)The lube-oil coats the revolving and reciprocating components dissipating the heat caused by friction. It is imperative that these systems have adequate centrifuge and filtration systems.
The supply of good quality low sulfur heavy fuel oil is essential to the marine diesel engine combustion process.
Likewise the lubricating oil should be of the correct grade and viscosity when supplied to the different reciprocating and revolving components of the main engine. It is very important that the correct treatment of marine main diesel engine fuel and lube-oils is carried out. This is achieved aboard ship by maintaining the optimum temperatures and pressures of both the fuel and lube oil through the use of pumps, heaters, and coolers.
Cleanliness is of utmost importance as is the regular maintenance and inspection of the lube and fuel oil cleaning components consisting of centrifuges and filters.
In the following sections, these operations will be examined, including the role of the ships watch keeping engineer in maintaining the optimum running conditions of the fuel and lube oil systems.
The Operation of the Centrifuges
There are several types of centrifuges used to remove water and particles from the fuel and lube oil; the most popular being the disc type as made by DeLaval rotating at 7000 revs and, the tubular type by Sharples which rotates at 15000 revs. However we shall look at the disc bowl type which is suitable for marine engine applications.
The centrifuges can be located close to where they are needed or kept together in a centrifuge room. I prefer them to be located in their own room which allows room for maintenance tools, a bench and cleaning troughs, although it can get pretty warm in the centrifuge room as the oil heaters are contained there as well.
Anyway the dirty heavy fuel oil is drawn from the bunkers, passing through several screens and a heater. It then enters centrifuge inlet pipe located at the centre of the top of the upper circular cover. Fresh water is also be supplied through a similar inlet and used to form a seal inside the centrifuge bowl. If a seal is not formed, oil will flow out of the water/sludge outlet.
The centrifuge operates by centrifugal force, the disc assembly spinning round at high revolutions and throwing the water and particles to the outside where they gather in a layer on the inside of the bowl, liquid sludge and water draining away from the lower centrifuge outlet to the sludge tank. The clean fuel oil is forced up the centre bore of the discs exiting at the top ring. It drains from here into the upper centrifuge outlet from where the cleaned oil is piped to the settling or day tanks ready to be supplied via the main fuel pump and filters, up to the main engine fuel pumps and injectors.
A sketch of the fuel oil system is shown below.
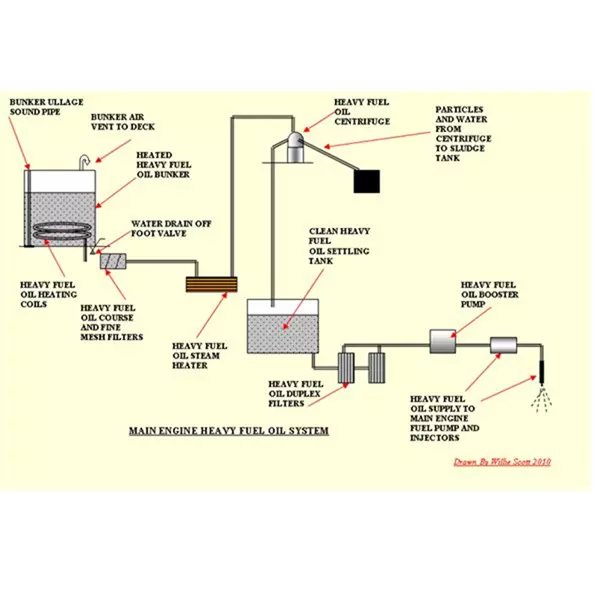
The lube oil is subjected to the same treatment except that it is drawn from the main engine sump and heated before entering the top of the centrifuge. The heater thins the oil making it more amenable to centrifuging. After cleaning it is returned to the main engine sump, in a closed circuit 24 hour constant operation.
A sketch of a typical lube oil system is shown below.
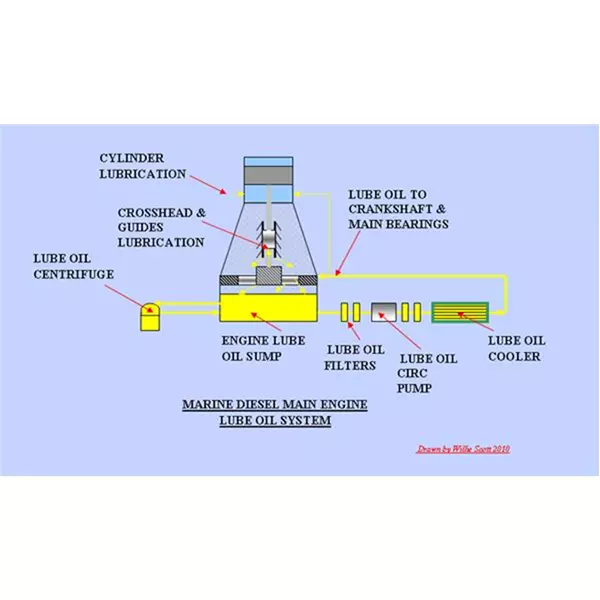
Oil Filters and Screens
Another very important part in maintaining a clean oil supply is the use of a good set of filters on the fuel and lube oil systems.
The fuel oil bunkers have steam heating coils which keep the heavy oil viscous and from here it is drawn through a couple of medium and fine mesh screens through the fuel oil heaters, and through the centrifuge. The clean oil is stored in the settling or day tank being drawn out by the transfer pump which has filters on either the suction or discharge pipework or both.
The lubricating oil is drawn from the sump by the lube oil circulating pump through a set of duplex filters. It is discharged by the pump through a similar set of discharge filters and the main engine lube oil tube cooler, which uses seawater to cool the oil. The cooled, filtered oil is then supplied under pressure to the main engine crankshaft bearings, crosshead bearings and guides before being returned back to the sump.
Screens, Filters and Centrifuge Maintenance
Screens
The screens can be isolated and removed for cleaning. This can be carried out in the centrifuge room and using paraffin or diesel oil to clean the dirt from the mesh.
Filters
Duplex oil filters can be changed over, isolated and cleaned using paraffin or diesel and blown dry with compressed air before assembly. These filters will be very hot – give them time to cool down before stripping them.
Centrifuge Maintenance
1. Ensure the power to the centrifuge is switched off; I used to isolate the power from the control box as well to avoid accidental starting of the drive motor.
2. Remove the bowl cover and remove the disc assembly from the centrifuge bowl. This unit is quite heavy and hard to grip but there is usually a compact lifting device supplied with the centrifuge maintenance tools for this purpose.
3. Use the C spanner to unlock the disc assembly
4. The individual discs can now be released from the assembly and cleaned with paraffin or diesel in a suitable bucket or trough and well dried.
5. The stainless steel conical discs are uniquely numbered so they can be reassembled in the correct order, this is important as the holes in the discs must line up.
6. The sludge can then be scraped from inside surface of the centrifuge bowl and the bowl washed and dried.
7. Everything is then reassembled, taking care with gaskets and disc securing devices.
8. Reinstate power supply and run up the centrifuge, apply a water seal and introduce oil to be centrifuged.
A sketch of a typical centrifuge is shown below.
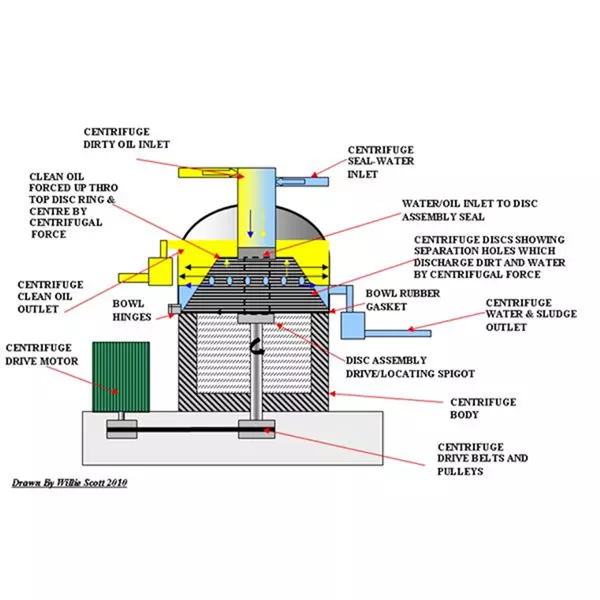
Summary
Fuel and lube oils are the lifeblood of the marine diesel engine and it is imperative that the correct grade of oils are supplied to the ships bunkers and lube oil sumps. Both oils must be maintained in a clean condition being pumped and circulated at the correct temperature and pressure to the relevant engine components, ensuring maximum engine efficiency.
This is achieved through the use of various mesh screens, filters and centrifuges which remove particles and water from the oil.
Watchkeeping engineers maintain the filters and centrifuges and also ensure through the adjustment of heaters and coolers that the oils are kept at their recommended optimum values.