Large Marine Diesel Engines are started using high pressure compressed air. The air is admitted into the cylinder when the piston is just past TDC and continued until just before the exhaust valve opens. There is always more than one air start valve open: – a situation known as overlap. This ensures that the engine will start in any position. The opening of the main air start valves is controlled by a set of pilot valves located in the air start distributor, which in turn are timed to operate by a drive linked to the main camshaft. In the example shown, a small camshaft is used to control the opening and closing of the air start pilot valves.
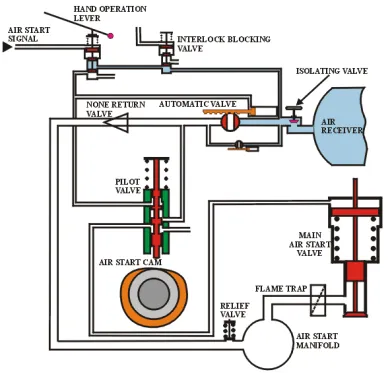
The drawing shows the principle of operation of an air start system. Large air receivers are used to store the compressed air. The diagram shows the isolating valve open so air is being allowed as far as the automatic valve and the air start control valve.
When the engine is required to start, a low pressure air signal is sent to the air start control valve (which can also be hand operated in an emergency). The air pushes a piston down which opens the valve and allows high pressure air to flow to the pilot valve and the automatic valve operating pistons. The pilot valve is forced down onto the cam profile and the automatic valve opens and high pressure air is led to the main air start valves and the pilot valve. When the pilot valve cam follower is on the lowest point on the cam, air flows to the operating piston of the main air start valve for that particular cylinder, opening the valve and allowing high pressure air to flow into the cylinder.
When the pilot valve is lifted by the cam, the pilot valve vents and the main air start valve closes. When the start air signal is taken off the air start control valve, the system vents and the automatic valve shuts.
The animation below shows the sequence of operations.
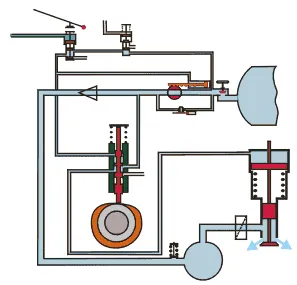
An interlock blocking valve will operate, for instance if the turning gear is left in, and this will stop high pressure air from reaching the air start control valve and thus either the automatic valve or the pilot valve.
A slow turning valve is fitted. This will open instead of the main automatic valve if the engine has been stopped for more than 30 minutes during manoeuvering. It will only supply enough air to turn the engine over very slowly; This is a precaution in case a cylinder has had oil or water leak into it which would cause damage to the engine when starting. If the engine completes a full revolution on the slow turn, then the main automatic valve opens and the engine will start. (note: The operating system for the slow turning has been omitted for simplicity).
International Association of Classification Society rules state:
In order to protect starting air mains against explosion arising from improper functioning of starting valves, the following devices must be fitted:
i. An isolation non-return valve or equivalent at the starting air supply connection to each engine.
ii. A bursting disc or flame arrester in way of the starting valve of each cylinder for direct reversing engines having a main starting manifold.
ii. At the supply inlet to the starting air manifold for non-reversing engines
Devices under (ii) above may be omitted for engines having a bore not exceeding 230 mm.
The system may also be provided with a relief valve.