Measuring the contents of a tank is a job which most mariners hate to do. For this reason, many gauges and devices have been produced for reducing the man hours of mariners. Read here to learn about the common different types and their construction with detailed pictures of each.
Ships have various tanks as a part of their structure. The usage may vary from ballast purposes to sludge retention. All these tanks store certain liquids whose level (quantity) has to measured and checked on a daily basis. Failure to do so will result in huge devastation, ranging from a pollution incident to stability problems. Instrumentation has now been developed so that manual gauging is no longer required; crew man hours have been saved greatly due to remote gauging techniques. In this article, the different types of tank level measuring techniques used on board ships will be discussed.
Gauge Glass
This is the simplest of all instruments used to measure the level inside a tank. The gauge glass has a long tubular glass which extends from top of the tank to the bottom in length, usually circular in cross section. The tank has openings in the top and in the bottom to extend connections to the circular long tube.
Since the material is usually made of glass, it is very fragile and should be handled with extreme care. Some tanks may also be equipped with plastic gauges. The main dis-advantage of a plastic gauge is that they cannot withstand heat and may discolour soon.
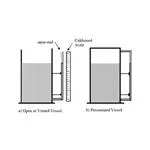
Usually these gauges are equipped with self-closing or auto shut off arrangements. These gauges may tend to break at any time, thus leading to localised flooding of the contained space. For this reason,there is always a safety shut off arrangement, usually at the bottom end of the gauge. These type of gauges are mostly found on small tanks with water or diesel oil. Example: fresh water expansion tanks. The same principle of gauge glass may extend and can be found on boilers. Boilers have water level gauge glasses that are designed to withstand more rigorous working conditions.
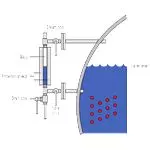
Floats:
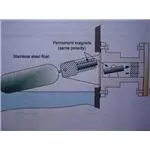
Float type level sensors may be of different types. They may indicate continuous variation in liquid level or just alarm high or low level. Floats are also used for filling a tank when the level drops and stopping filling when the level reaches optimum. These can be witnessed in toilet flush mechanisms and boiler feed tanks.
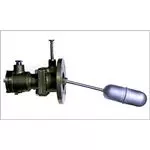
Most tanks have high and low level float indicators provided on the tank walls. When the liquid level in the tank reaches maximum, the float is lifted up by the rising liquid surface. The opposite end of the float device has a magnet which flips another magnet in the fixed body. The magnet’s flipping action makes or breaks the circuit which causes an alarm. They also have a provision for testing the alarm manually.
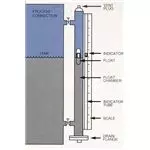
Pressure Based Level Measurement
The head of available liquid in the tank is used and the head is converted into level measurement. As the level inside the tank varies, the head of liquid and thus the pressure varies accordingly, and this is used as reference for indicating the level in the particular tank. For sensing the pressure variation inside the tank, a slack diaphragm pressure sensing device is used. One end of the diaphragm is connected to the open end of the tank where atmospheric pressure acts on it. The other end is connected to the safe bottom-most portion of the tank, enabling the liquid in the tank to exert a corresponding head on the diaphragm. The diaphragm responds to the difference in pressure, which moves a needle calibrated to indicate the level inside the tank.
Bubbler Gauge
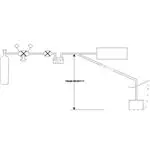
This is one of the famous types found in most of the remote reading gauges. This type is used usually for highly viscous oils like in fuel oil tanks and the cargo tanks of product carriers, etc. Compressed air is admitted at the top of a small diameter tube which is fixed vertically inside the tank. The base of the tube is left open from the tank bottom surface. When compressed air is admitted from the tube top, it bubbles out from the bottom and thus reaches the liquid surface. The air pressure is dependent on the hydrostatic head of liquid present in the tank. This air pressure is measured and calibrated to indicate the tank level continuously. A 3-way valve may also be provided to by-pass the compressed air from the restrictor, thus allowing blowing off the tube inside the tank to avoid any deposits.
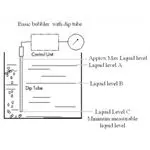
Ultra-Sonic/Microwave Level Sensor:
These devices use ultrasonic or microwaves to determine the ullage level of the liquid in the tank. The device emits microwaves or ultrasonic sound waves, which hit the surface of the liquid inside the tank and bounces back to the transmitter itself. The time taken to receive the signal back is calculated and thus ullage of the tank is determined. Main advantage of this type is there are no moving parts and mainly used for LNG/LPG tankers where manual sounding is not possible.
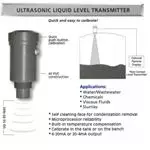
Capacitive Level Sensor:
A capacitor is said to have two plates, separated by a di-electric medium. For measuring tank levels, the capacitance probe acts as a single plate and the tank side wall acts as the second plate. As the liquid level inside the tank varies, the potential between the tank wall and the probe varies accordingly. Thus causes change in current in the circuit and thus it is calibrated for indicating the tank level.
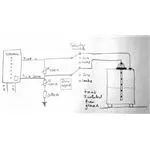