Actuators can automate valves so that no human interaction with the valve package is necessary to cycle the valve. They can be remotely operated and act as shutdown mechanisms in an emergency situation that would be dangerous for human intervention.
At a basic level, an actuator is a control mechanism that is operated by an energy source. This energy—hydraulic pressure, pneumatic pressure, or electric current—moves the internal mechanical parts of the actuator. Actuators can be designed to fail open (in the case of actuator failure, the valve will stay open) or fail close (in the case of actuator failure, the valve will stay closed). They are also distinguished by whether they are for quarter-turn (e.g., ball valves, plug valves) or linear (e.g., gate valves) valve operation.
Types
Double-acting actuators have air or liquid supplied to both sides of the piston with one side at higher pressure, which achieves the movement required to actuate the valve. This configuration uses pneumatic or hydraulic pressure of the air or liquid energy to open and close the valve.
Spring-return actuators have air or liquid supplied to only one side of the piston, and the energy to move the mechanisms comes from a spring on the opposite side. This configuration uses pneumatic or hydraulic pressure of the air or liquid to open or close the valve, and a spring affects the opposite motion.
Pneumatic actuators utilize compressed air to generate the operating energy. These actuators are quick to respond but are not ideal for environments under high pressures because gas is compressible. Pneumatic actuators are available in spring-return and double-acting designs.
- Piston-style pneumatic actuators generate linear force by the air acting on the piston. The conversion of this linear force to torque (for use in rotary valves) is achieved by specific actuator designs.
- Scotch-yoke actuators include a piston, connecting shaft, yoke, and rotary pin. The yoke is offset 45° from the axis of the piston at the two ends of travel and at 90° to the piston shaft when in the midtravel position. The canted scotch-yoke design is ideal for offset butterfly valve actuation.
- Rack-and-pinion actuators output a 180° turn, unlike traditional actuators, which produce a 90° turn of the pinion. This style of actuator is particularly suitable for actuating plug valves.
- Diaphragm-style actuators include a rubber diaphragm and stem in a circular steel housing. This style of actuator is ideal for valves requiring shorter travel, such as diaphragm valves and globe valves.
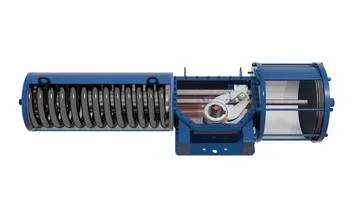
Pneumatic actuator.
Hydraulic actuators use liquid as a means to apply pressure to the actuator’s mechanical components. They can exert a large amount of force because liquid is not compressible but are generally limited in acceleration and speed. Hydraulic actuators are available in spring-return and double-acting designs.
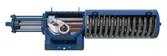
Hydraulic actuator.
- Direct-gas actuators utilize a high-pressure natural gas or nitrogen supply to achieve on-off control of a valve in any natural gas transmission application. Direct-gas actuators are available only in double-acting configurations.
- Piston-style hydraulic actuators, available in scotch-yoke and rack-and-pinion designs, function the same as pneumatic piston-style actuators but utilize liquid instead of gas to generate the operating energy.
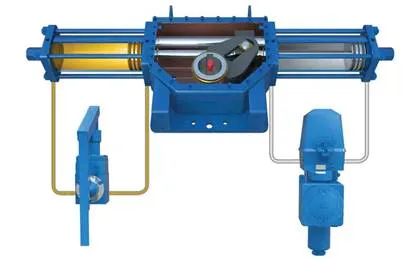
Direct-gas actuator.
Gas-over-oil actuators use high-pressure gas supplied from the pipeline suspended above a hydraulic fluid to move the mechanics of the actuator. Gas-over-oil actuators are available only in double-acting configurations.
Electric actuators use an electric source, such as a battery, to power the actuator. They usually include intricate electrical circuitry. Because of their use of electricity as a power source, they may not be ideal for remote installations.
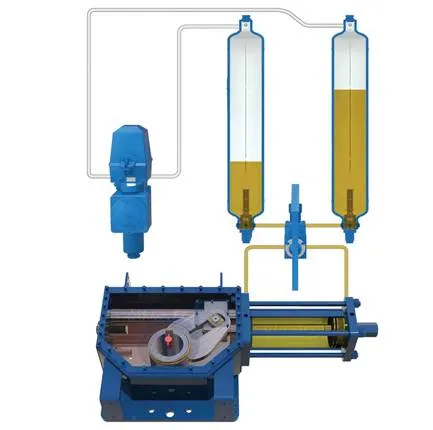
Gas-over-oil actuator.