There are a number of reasons for starting and reversing problems in marine engines. This malfunction is one of the most frightening and dangerous situations to encounter when maneuvering a ships main diesel engine, but it can be avoided through regular maintenance of the air start components.
A ship’s main marine diesel engine is started on compressed air that is controlled by various components of the air start system. It is a well-tried and tested reliable system, but it can go wrong if not properly maintained.
The following sections examine a typical air start system, with the first section providing an overview of the system.
Overview of System
The air start system looks rather complicated, but it is quite simple when you examine it without the safeguards. These are put in place to prevent such occurrences as starting the engine without having a signal from the engine room telegraph, trying to start the engine with the turning gear engaged, or trying to start ahead when the telegraph asks for astern. There are also safety systems incorporated such as a bursting disk and numerous non-return valves in the event of a leaking air start valve.
The next section lists some of the problems that can be encountered when maneuvering.
Problems in Air Start Systems
We shall look at two common problems encountered when maneuvering the main engine: not starting and starting in the wrong direction (reversing instead of starting ahead).
○ Not Starting
As we have seen, there are various interlocks in place to prevent the engine being started until certain criteria are met. If the engine won’t turn over on air, the bridge should be informed then the following checks should be carried out.
○ Check air start supply valves from air receivers are open and that the pressure is 30 bar.
○ Check that the turning gear is disengaged
○ Check that the turning gear and telegraph solenoid valves have actuated. This will supply air to the automatic valve, air distributer, the air manifold, and air start valve.
These are the initial checks that can be quickly carried out. If these are all satisfactory, then the problem lies in the controls ahead/astern solenoids. The air distributer or the air start valve itself may be stuck in the closed position. The ship will need to anchor or be towed alongside for these checks to be carried out.
Engine starts in wrong direction
If the engine starts in the astern instead of ahead direction, the following checks should be carried out.
○ Ensure the air start control moves to reverse mode at the control station. This is a visual check and can be observed when the telegraph rings from ahead to stop then astern. If this does not happen, the solenoid valve may be stuck.
○ The oil and air supply to and from the reversing valve should be checked. A blockage of either will stop the reversing servo motor operating and allowing change over from the astern to ahead position.
This again will take further investigation, so the ship should anchor or remain tied up to the quay.
As this ahead/astern changeover is controlled by lube oil and compressed air and is interlocked with the fuel pumps. These are the usual culprits and the starting point of a thorough investigation. I have experienced this situation only once and fortunately we were leaving port and still tied to quay by stern spring. Once the bridge was informed, a rope from the fo’c’sle was thrown ashore and made fast. This gave us the chance to check for the fault, which turned out to be the oil supply from the crosshead oil supply pipe being blocked.
As I have said before, the maintenance of the air start system components is paramount to the operation of the system.
Main Components of the System
Air supply system
○ Two air compressors
○ Two air start vessels
○ Numerous non-return valves
○ Numerous drain valves
Control system
○ Turning gear out sol v/v
○ Telegraph signal sol v/v
○ Automatic valve
○ Ahead and astern change-over
○ Air distributer
○ Air start valve
Anti-explosion components
○ Air supply to manifold from air vessels non-return valve- this prevents hot gasses from returning to air receivers.
○ Air manifold pressure relief valve – this operates if pressure rises due to heat from gasses.
○ Air supply to air start valve bursting disk – this disk ruptures under increased pressure caused an air start valve leaking back.
Mandatory Safety Precautions
Before we get into the operation of the system in the next section, this is an opportune moment to make a closer examination of the precaution against explosion, which is a very real threat even in today’s modern engines that incorporate the latest in engine management systems.
○ Compressors
The compressor air inlet filters should be positioned in an oil-free zone, i.e. no oil fumes should be present.
The compressed air supply lines to the air receivers must be protected by non-return valves.
○ The air receivers
There are two air receivers, linked by a common discharge pipe to the system. The air from the compressors will contain oil and water (there is no way around this). This mixture ends up in the air vessels as a mist, eventually settling to the bottom of the vessel. It is imperative, and I cannot overstress this, that the mixture be drained from the vessels after every charge, and regularly when maneuvering. The oil also coats the internal of the supply pipes; this too can be reduced by draining the air vessels.
These actions, as well as checking by hand for heat in the air supply pipe between the air start valve and the air manifold, form part of the watch keeper’s duties. Any excess heat here, and the fuel and air to that particular cylinder should be isolated, and the bridge made aware of the situation.
Before we leave the precautions there are many examples of air start system explosions. One of worst ones occurred on the MV Capetown Castle, killing seven engineers. Lloyd’s register recorded 11 such explosions between 1987 and 1998; all down to oil gathering in the receivers and piping and ignited by exhaust gasses. One a year speaks for itself: drain the air vessels regularily and maintain the system.
A sketch showing an air start system where the air start valve is leaking is shown below. Note the pipe that should be checked by hand for overheating;
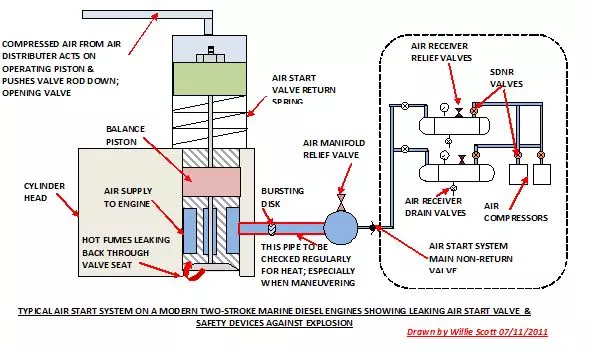
The Operating Principles of Marine Engine Air Start Systems
I have sailed on quite a few marine diesel engines, including B&W, Sulzer, and Stork/Werkspoor. All had variations of the system I am about to describe, but the principles are much the same.
I drew a sketch from memory (45 years ago) but updated it from a very good website referenced at the end of the section. The sketch also appears at the end of the section and can be referred to during the reading of the notes.
We begin then with the bridge ringing down standby on the engine room telegraph. (We used to change over fuel from Heavy Fuel Oil to Modified Diesel Oil for maneuvering.)
1. If in port, ensure turning gear is not engaged.
2. Open both air receivers’ isolation valves and start up a compressor to fill receivers to maximum; drain oily water of reservoirs and also from dead leg on supply pipe work.
3. This allows the compressed air to flow as far as the turning gear solenoid valve. Provided the turning gear is disengaged, this will allow the supply of air at 30 bar to the automatic valve passing though the non-return valve and into the manifold. From here the air is piped to the air chamber in the air start valve. (This is the pipe that will get hot if you have a leaking air start valve.) The valve is held in the shut position by the spring tension.
4. When an ahead or astern movement is rung and answered on the engine room telegraph, the telegraph start signal sol v/v is activated allowing air to the ahead and astern solenoid valves mechanism.
5. The air is now directed to the starting air distributer that is fitted on the end of the camshaft. This enables it to select the appropriate cylinder(s) to supply air to. This will be the relevant cylinder that is just passed TDC and on the downward stroke.
6. The air from the starting air distributer is at 30 bar, and this is injected into the air start valve top piston. This overcomes the spring tension and forces the piston downwards thus opening the valve and introducing the air at 30 bar to the cylinder(s) having been supplied earlier to the air chamber.
7. Depending on the engine make and model, air can be supplied to several cylinders to assist starting. A “slow start” supply can be used if there has been a lapse of half an hour between movements when maneuvering.
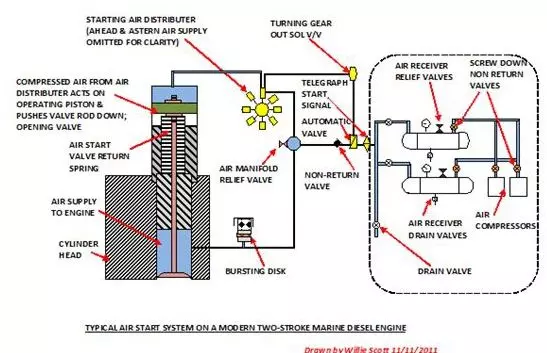
Maintenance of System Components
○ Compressors
Regular inspection of filters, suction and discharge valves, as well as piston and ring checks should be performed at the manufacturer’s recommended periods. Intercooler tube nests should be cleaned ensuring optimum air flow.
○ Air supply Manifold Relief Valve
This should be regularly inspected to ensure that the spring is operating correctly, with the complete overhaul being to manufacturer’s instructions.
○ Air Start Valves
This is the most important component and if not maintained, will begin to stick due to a weak/badly adjusted spring or worn piston rings allowing hot combustion gasses into the compressed air piping.
The valve should be replaced regularly with an overhauled and tested spare, the spare then being stripped and spring, pistons, and rings inspected. The valve is ground into the seat using fine lapping paste before rebuild and bench pressure testing.