Estimating costs for shipbuilding and repair was carried out in a specialist department by men experienced in hull construction and engine manufacture. Today, it is much the same in most shipyards worldwide.
Britain used to be one of the world’s greatest shipbuilders, building ships for the then extensive Merchant and Royal Navies. Nowadays this industry has moved to the Far East yards who can construct large ships efficiently and cheaper in half the time we used to. However, although the construction methods and materials have changed, the method of estimating will be similar to what it was in my day.
Overview of Construction and Ship’s Repair
I left Harland and Wolff in 1966 to join the Merchant Navy, and it was thirty years before I returned. I was working at Kellogg, Brown, and Root’s construction yard here in the Highlands of Scotland as a Project Engineer when we built the topsides for the Schiehallion, a Floating, Production, Storage Offloading vessel (FPSO), and Harland’s had the contract for building the hull. I followed our completed topside processing modules across the Irish Sea to Belfast, and what a difference I saw on arrival at Harland & Wolff’s yard!
The first thing I saw was the two gigantic cranes, Samson and Goliath, visible for miles around the span the huge dry-dock. The image below from Wiki Commons by Wilson Adams depicts these. (Please click on the image to enlarge.)
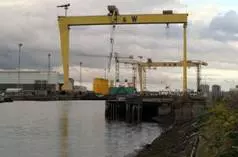
This combination has revolutionized hull construction: the fabrication shops produce large sections of fully welded hull section that are transported by the cranes into the base of the dry-dock and here they are welded together to very efficiently form the hull. Most of the welding is carried out automatically before being heat treated to reduce stresses.
Mild carbon steel plates were normally used for the hull and decks, although a few years ago high tensile steel was used to reduce the plate thickness and therefore save weight. However, this proved to be unsatisfactory for several reasons and we are back to mild carbon steel and alloy plates. Alloys are added at the casting stage before rolling to improve corrosion resistance. This is used almost universally for the double skinned hulls where corrosion previously proved to be a problem in the spaces between the hulls.
Nowadays most tanker ships are twin-hulled, i.e. there are two hulls separated by traversing and vertical beams and stiffeners. This is to comply with pollution legislation in the event of collision or grounding on rocks and for the prevention of the subsequent oil spillages. These spaces can be treated with anti-corrosion coatings and used as double bottom and wing ballast tanks. Below is an image of a supertanker having double hulls from Wiki Commons by PA2 Dan Tremper.
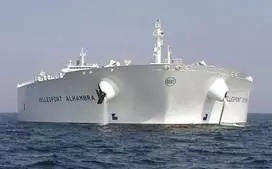
Internal piping is installed into the hull section during construction in the fabrication shop, being joined by pup-pieces, small lengths of pipe, as soon as the hull sections are assembled and welded in the dock.
Bulkheads are also fabricated in the shops and shipped to the dock fully welded within the hull sections.
Accommodation and HVAC can be fitted either in the shops or in the dock. My own experience in offshore constructions accommodation lends towards all the main welding being completed before fitting out the cabins due to fire risk.
Engines are lowered into the engine room by overhead cranes; sometimes this can be accomplished in one piece. In my day we assembled the engines in the engine-works then tested them before stripping them down for transport to the outfitting berth.
As an aside, when I went back to Harland’s, I walked through the old engine-works where I learned all about the Burmeister and Wain diesels so many years ago.
All the bays where the components were machined and assembled lay empty, and all that was left of the testing area was the steel bedplates and the exhaust ducting hanging from the roof of the shop.
Anyway to continue from my ramblings, the drive gear is assembled; the thrust block and prop bearings are aligned before the shaft is dropped in sections and bolted up. We used piano wire in my day, but nowadays laser alignment is the norm. The final prop shaft is pushed through the stern gland and stern tube, then the propeller is fitted to its tapered, keyed shaft and fixed using fine threaded hex nut then the threaded cone is fitted.
Now we are ready to flood the dock and start commissioning the various systems along with the main and auxiliary engines.
Estimating Costs and Preparing the Bid for a New Build
I spent some time in the estimating departments of several Offshore Construction Companies, and although my remit was estimating piping fabrication and mechanical equipment installation and commissioning, I also did a little hull fabrication using welded plates.
Repairs are estimated on their description as supplied by the ship owners that will include the timescale relevant specifications and a set of drawings.
The following examination will include basic estimating techniques of the main components;
○ The hull
○ The engine room
○ Piping and HVAC
○ Electrical equipment
○ Commissioning
○ Labor
The costs associated with producing structural and piping drawings from the client’s design drawings along with the cost to produce the final bid and dry-dock use/launching are an overall cost added to the construction costs.
The Hull
This requires a Material Take Off (MTO) for all the materials used in the hull construction. The estimators are each allocated their own section of the hull, usually by frame numbers, to produce this MTO and include everything from the main plates, longitudinal main girders, and bulkheads right down to the smallest stiffener.
Blasting, painting, and any insulation or fireproofing is added, and the cost of the total steel plate and steel section is then estimated.
○ Welding and NDT (Non Destructive Testing)
There are two basic welds used in welding plates and structural members, fillet and full penetration welding, and also numerous other methods of welding depending on the client’s preference and specifications. These have their own costs for consumables such as the stick rods, rolls of wire, and shielding gas.
The length of these welds are estimated along with the man-hours for manual/automatic welding and the associated stress relieving heat treatment and NDT, including radiography where the full penetration welds are subjected to x-ray are costed.
Assembly of all the fabricated sections will normally be carried out in the dry-dock or on slipways; and there will be standard costs worked out by tonnage of materials for these operations, i.e. use of cranes and opening and closing the dock gates. To flood and empty a dry-dock can cost up to $600,000 by the time you remove the silt then replace the water seals before closing again.
The Engine Room
The manufacturers of a modern ship’s main diesel engines such as Wartsila and MAN-B&W have licensed various shipyards around the world to build these engines and install them in their ships hulls. The costs will be pretty well standardized for the building and installation of the engines along with the auxiliary engines and associated pumps and coolers.
The installation costs will depend on whether the engines can be lifted into the engine room after testing is complete, or as in my day, in sections.
The cylinder heads of modern MAN B&W 2 stroke from Wiki Commons by xtreme machine is shown here.
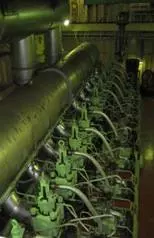
Piping Fabrication and Installation
The piping fabrication isometrics are taken from the design drawing and fabricated to these. The estimate is taken from the drawings in order to ascertain the lengths of pipe, number gaskets and bolts along with the number of fittings and welds. Materials for ships piping are normally cuni-copper/nickel, stainless, and carbon steel, so different NDT is required, including radiography if pipes are high pressure oil or gas.
Magnetic Particle Inspection (MPI) for carbon steel fillet welds is the cheapest method, and usually only a percentage of welds are examined, unless there is a problem found.
Costing is based on the total length and type of materials, number of welds, and number of fittings. Also estimated is the pipe supports fabrication, shot blast, painting and installation, along with the associated hydro-testing required on the completed runs.
HVAC Fabrication, Installation and Testing
Fabrication drawings are made from the clients design drawings, and from these the material required to fabricate the HVAC ducting spools is estimated.
Components such as fans, dampers, and filters are shown on the drawings and costed.
Some HVAC ducting is fabricated from stainless steel, particularly for use in the accommodation and galley, but the majority is from carbon steel sheet.
Once fabricated the carbon steel spools are hot-dipped galvanized before being installed along with the different components and pressure tested for leaks.
Electrical Equipment
The motors for pumps and fans are included with the driven components and normally bought as sets, i.e. “pumpsets.”
The installation of all the other electrical equipment such as switchboards, transformers, control panels, including the electrical cable used to connect them, also need to be estimated.
Labor – Man-hours
There are several methods of working out the man-hours (MHR) required for all the above operations. One method is to use the weight of materials, but most shipyard estimating departments have what is known as “norms” to achieve this very important component of estimating the fabrication of ships.
Commissioning
This includes the following main components: HVAC, piping and pumps, electrical and mechanical equipment, along with main and auxiliary engines.
This can be carried out by the shipyard personnel, but it is quite specialized. At the offshore construction yard, we normally brought the equipment and systems up to a pre-commissioning stage. This included pressure and leak testing, electrical circuit testing and certification, supplying the various mechanical pumps and engines with lubricating oil. These were then handed over, usually by systems, to a subcontracting commissioning engineering company who would prepare their own estimating for these components, and this is then added it to the main bid.
Notes:
1. I have included procurement of the various components and pieces of equipment to add to the estimate, however it is quite normal for the client to procure the equipment and transport it to the shipyard that they have chosen to build their ship.
2. There is often a long lead-in time between receiving equipment before it is required to be installed, so most yards used to have a Preservation of Equipment Procedure. By the amount of queries I have had to several articles I have written on the subject, especially from Engineers looking after stored equipment in high humidity conditions of the Far East Shipyards, this is still the case. This should also form part of the estimation including man-hours, materials used, and warehouse costs in heating and dehumidification.
3. The estimation of ships repair follows along the lines of the construction operations given above. The shipowner normally gives a scope of work with a set of drawings, and from this information it will be decided if any hull repairs will require a dry-docking. Engine repairs are normally carried out at the quayside where cranes and services such as water and power are available.