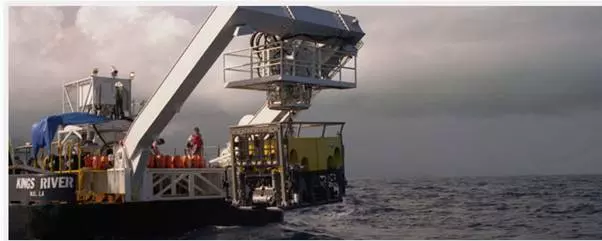
What is it?
The “A” Frame section is moved from the inboard stowed position to the outboard launch position by Hydraulic Luffing Cylinders. The hydraulic luffing cylinders are controlled and operated from a central control point on the “A” Frame base, where all the individual proportional control valves are located, including the controls for winches.
The individual proportional control valves where applicable are fitted with internal motor spools which give excellent control during operation of the winches.
The hydraulic cylinders are fitted with fail safe load holding counterbalance valves, to protect against hydraulic pressure failure during operation. The pivot points on the “A” Frame assembly are fitted with Stainless Steel grease nipples for lubrication purposes.
An electrical top limit switch is installed adjacent to the central fixed sheave which will trip the HPU in the event the dive basket is raised above its normal operating parameter. This additional safety feature protects the basket occupants and equipment.
At Hydraproducts we have incorporated further safety features on our HPU’s with redundancy systems, this will ensure the safety of divers and valuable equipment if the hydraulic unit should ever fail.
Hydraproducts has a wealth of experience in supply and manufacture of bespoke Subsea Marine Hydraulic equipment. We specialize in bespoke projects with emphasis on quality and delivery.
For those seeking to upgrade HPU equipment in order to gain cross-compatibility with different systems, or to improve the systems performance with current equipment, Hydraproducts can provide the necessary expertise to all corners of the world.
For more information on Subsea Hydraulic products please contact the main office.
Hydraulic Power Packs – Introduction to Launch and Recovery Systems
If you’re a hydraulic power engineer and you follow our blog posts, we are now going to take you on a journey deeper into our niche and introduce you to one of our hydraulic power unit related specialist areas, known as LARS or Launch and Recovery Systems.
To understand what’s involved in these machines that are used offshore in marine environments such as on oil rigs, we need to get familiar with the individual components:
Every launch and recovery system is equipped with an umbilical winch. This has to be able to accommodate the entire length and diameter of the remotely operated vehicle umbilical. This winch will typically make use of a level wind mechanism to cater for even spooling of the umbilical cable on to the drum of the winch.
To power the winch there is usually a suitably sized hydraulic winch motor attached that can pull in the remotely operated vehicle (ROV). This is where the hydraulic power pack comes in to play.
A Crane or ‘A’ Frame will need to be able to lift and on-board the ROV. It will also need to be strong enough to be able to accommodate the weight of the vehicle plus its load.
Most often it’s easier to put the ‘A’ frames and the hydraulic power unit HPU together on a dedicated mounting skid base so that they can be easily welded to the deck. Although they are sometimes positioned to be stand-alone units.
It’s a requirement for the LARS to be certified for use. This will generally include a Lloyds witness of the system load tests or DNV design approval. These are required prior to manufacturing. They are something that can cause delay and is most often extra cost.
A bit of a crash course into the world of LARS. We will be featuring more about this fascinating area in our blog posts, so if you’re unfamiliar with the offshore industries, you will have a chance to find out more about them and how we apply our hydraulic power packs in this field.
Comments are closed